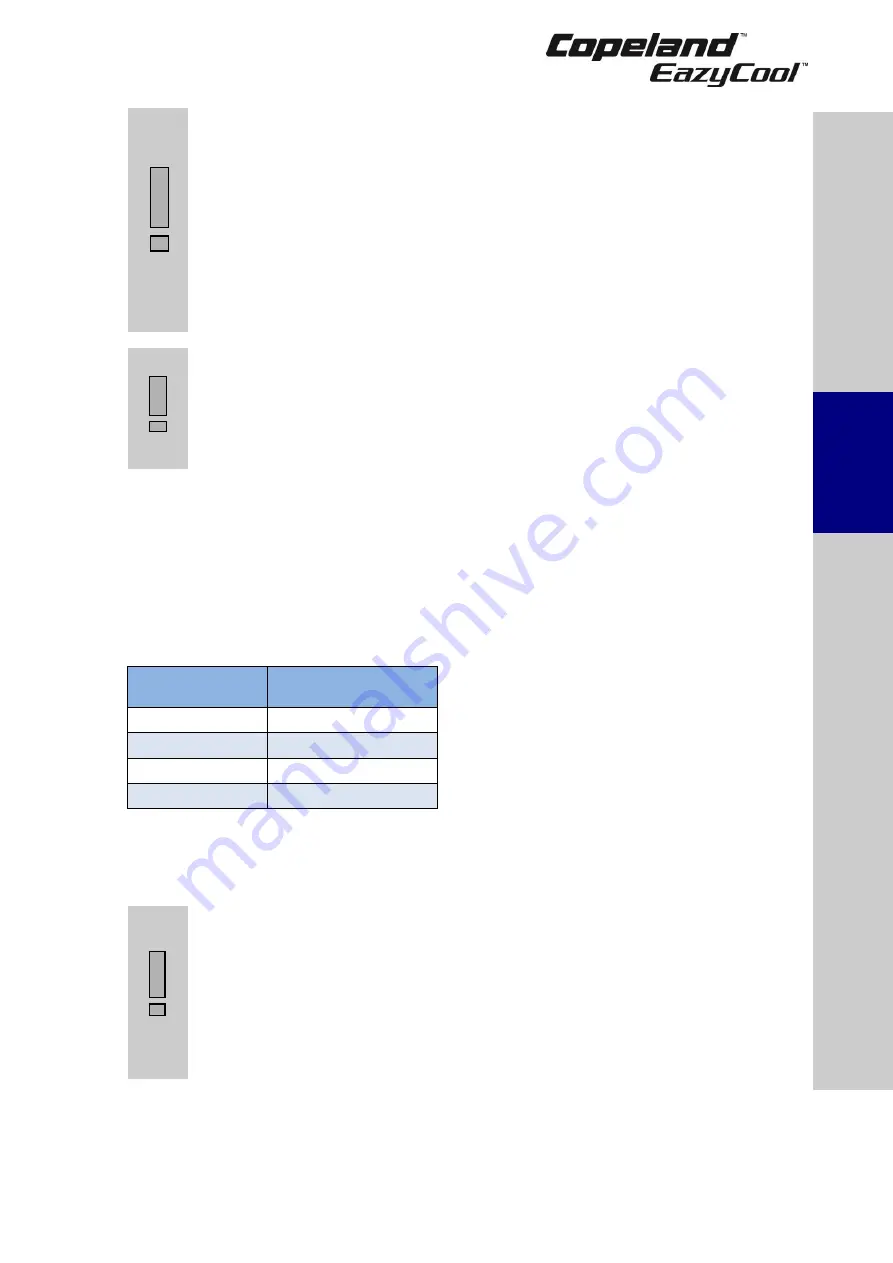
C6.1.6/0117-1017/E
33
IMPORTANT
Tubing quality! Installation contamination!
All interconnecting piping
should be of refrigeration grade, clean, dehydrated and must remain capped
at both ends until installation. Even during installation, if the system is left for
any reasonable period of time (say 2 hours), pipes should be re-capped to
prevent moisture and contaminant from entering the system.
Connection sizes! Unsuitable refrigerant flow rate!
Do not assume that the
service connection sizes on the unit (at the service valves) are in fact the
correct size to run your interconnecting refrigeration pipes. The service valve
sizes have been selected for convenience of installation and in some cases
(larger units) these may be considered too small. However, for the very short
pipe run within our units these service connection sizes are adequate. All
interconnecting piping should be sized to satisfy the duty required.
IMPORTANT
Absence of insulation on the liquid line in ZXLE units! Air moisture
condensation and lack of performance!
Moisture will condensate on the
liquid line and cause water droplets. The liquid line can pick up additional heat
from the ambient which will adversely affect the sub-cooling desirable for the
liquid refrigerant before it enters the expansion valve. Insulate both the suction
and liquid interconnecting piping between the ZX unit and the evaporator.
The pipe should be sized to ensure optimum performance and good oil return. The sizing must also
take into account the full capacity range through which this particular unit will need to operate.
Pipe runs should be kept as short as possible, using the minimum number of directional changes.
Use large radius bends and avoid trapping of oil and refrigerant. This is particularly important for the
suction line. The suction line should ideally slope gently towards the unit. Recommendation slope is
1/200 to 1/250. Upper and lower oil traps, double risers and reduced pipe diameters may be required
for suction lines where long vertical risers cannot be avoided.
All pipes should be adequately supported to prevent sagging which can create oil traps. The
recommended pipe clamp support distance is shown in
Table 29
below:
Tube size
Max distance between
2 clamp supports
12.7 mm (1/2 inch)
1.20 m
16.0 mm (5/8 inch
1.50 m
22.0 mm (7/8 inch)
1.85 m
28.5 mm (1 1/8 inch)
2.20 m
Table 29: Maximum distance between 2 clamp supports
NOTE: It is strongly recommended to insulate both the suction and liquid interconnecting
piping between the ZX unit and the evaporator.
3.3.2 Brazing
recommendations
IMPORTANT
Blockage! Compressor breakdown!
Maintain a flow of oxygen-free nitrogen
through the system at very low pressure during brazing. Nitrogen displaces
the air and prevents the formation of copper oxides in the system. If allowed
to form, the copper oxide material can later be swept through the system and
block screens such as those protecting capillary tubes, thermal expansion
valves, and accumulator oil return holes.
Contamination or moisture!
Bearing failure!
Do not remove the plugs until
the compressor is set into the unit. This minimises any entry of contaminants
and moisture.
▪
Remove the discharge connection cap.
▪
Remove the suction connection cap.
▪
Open both valves mid-way. Care should be taken to avoid the holding charge releasing too
quickly.
▪
Be sure tube fitting inner surface and tube outer surface are clean prior to assembly.
S
afet
y
inst
ru
ctio
n
s
P
ro
d
u
ct
d
es
cr
ipt
ion
Inst
all
atio
n
S
tar
ting
up
&
o
p
er
atio
n
Ma
int
enan
c
e &
repai
r
Cer
tif
ica
tion
&
a
p
p
ro
va
l
Dismant
ling
&
d
ispo
sa
l