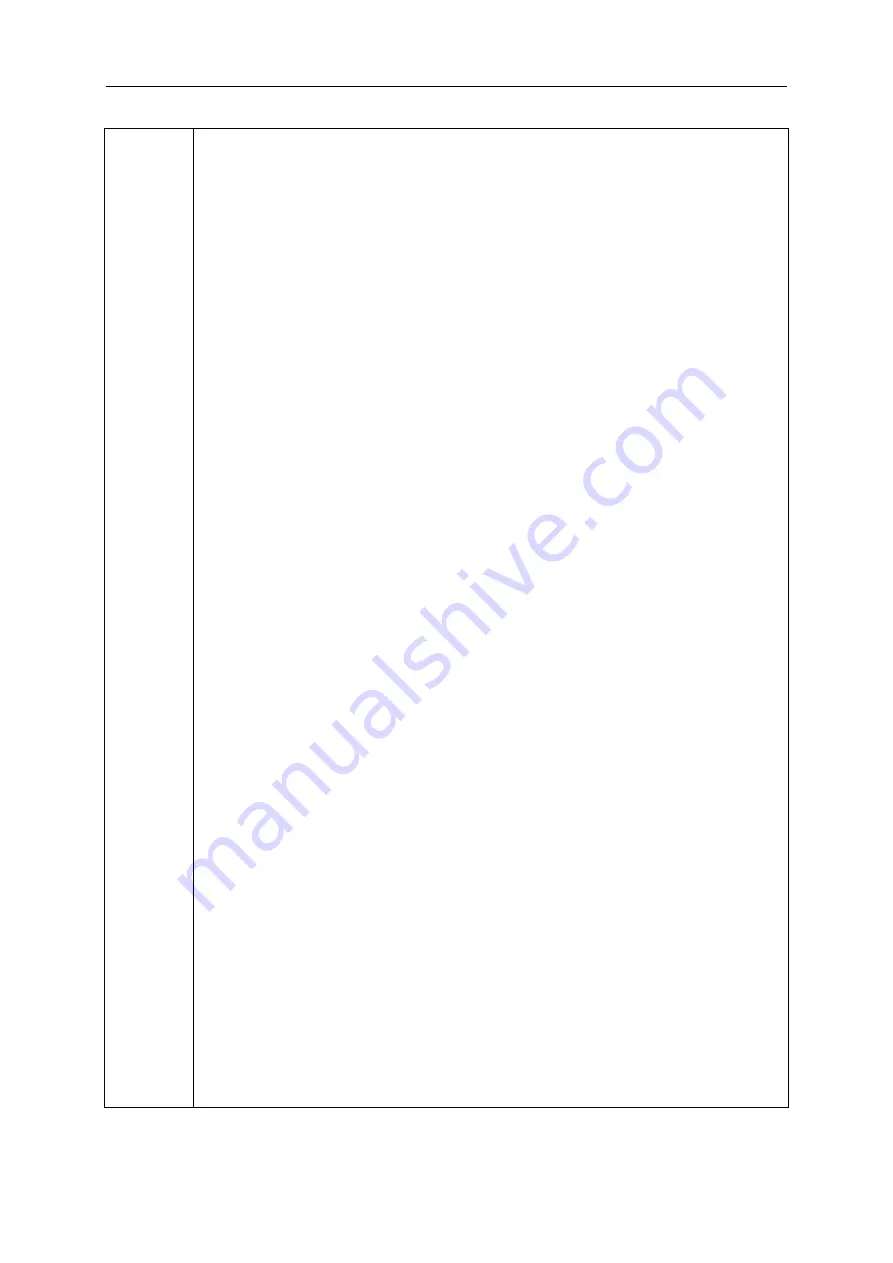
Electrical Operation and Maintenance Manual for Control Cabinet of EC2-S Industrial Robot
11
switch must be immediately pressed and robot exits the work area from the preset
evacuation route.
9. Both the operator and the supervisor must continuously monitor the robot for any
abnormal movement, collisions, or squeezing during check and maintenance.
Meanwhile, please confirm the safety passage for the operator is clear for evacuation.
10. If it is necessary to remove the safety fence during check and maintenance, please
take adequate safety measures:
•
Place the robot and peripheral devices properly.
•
Lock/calibrate the power and switch to avoid the power being turned on or the
switch being turned to automatic mode mistakenly.
•
Reinstall the safety fence and confirm all safety measures, functions remain the
same when check and maintenance are completed.
11. Only use parts supplied by EFORT for replacement. Be sure to use teaching mode
and move the robot as slow as possible in check and maintenance.
12. Turn off the control power supply and wait at least seven minutes for replacement
of the drive module and power supply module. Then start the replacement and remove
connectors after confirming the output voltage of the power supply is 0V. The heat sink
or regenerative generator may main hot right after the stop of the movement.
Therefore, please be cautious do not touch any hot part.
13. Please support the robot arm with proper lifting device before removing any servo
motor of joint axis. The removal causes fail of the brake mechanism of the axis.
Without reliable support, the arm falls. Please be aware same dangers occur if you
press any axis brake release switch on the control cabinet.
14. The robot must remain the same posture before and after the maintenance. Please
record posture data before the replacement of parts.
15. Check and record the location, connector number, installation method, and set data
of the printed circuit board or cable at the beginning of the replacement process, so
they can be recovered properly. The locking mechanism of the connector must be
locked tightly after it is inserted. Never touch the pins of the connector.
16. If compressed air or water is supplied, please cut off the supply source and release
the remaining pressure in pipelines before repair.
17. Please confirm all the protective devices function properly after check and
maintenance.
18. EFFORT will not be liable for any change or modification without authorization.
19. Numerous back-up batteries are built in the robot arm and control cabinet. Misuse
will cause burn, overheat, explosion, eruption, leak, etc. Therefore, the following
protocols must be strictly followed.
Summary of Contents for EC2-S
Page 2: ......
Page 4: ......
Page 10: ......
Page 34: ...EFORT INTELLIGENT EQUIPMENT CO LTD 24 15 19 21 front left side panel bottom plate 16 17 20 18...
Page 84: ...EFORT INTELLIGENT EQUIPMENT CO LTD 74...
Page 85: ...Electrical Operation and Maintenance Manual for Control Cabinet of EC2 S Industrial Robot 75...
Page 86: ...EFORT INTELLIGENT EQUIPMENT CO LTD 76...
Page 87: ...Electrical Operation and Maintenance Manual for Control Cabinet of EC2 S Industrial Robot 77...
Page 88: ...EFORT INTELLIGENT EQUIPMENT CO LTD 78...
Page 89: ...Electrical Operation and Maintenance Manual for Control Cabinet of EC2 S Industrial Robot 79...
Page 90: ...EFORT INTELLIGENT EQUIPMENT CO LTD 80...
Page 91: ...Electrical Operation and Maintenance Manual for Control Cabinet of EC2 S Industrial Robot 81...
Page 92: ...EFORT INTELLIGENT EQUIPMENT CO LTD 82...
Page 120: ......