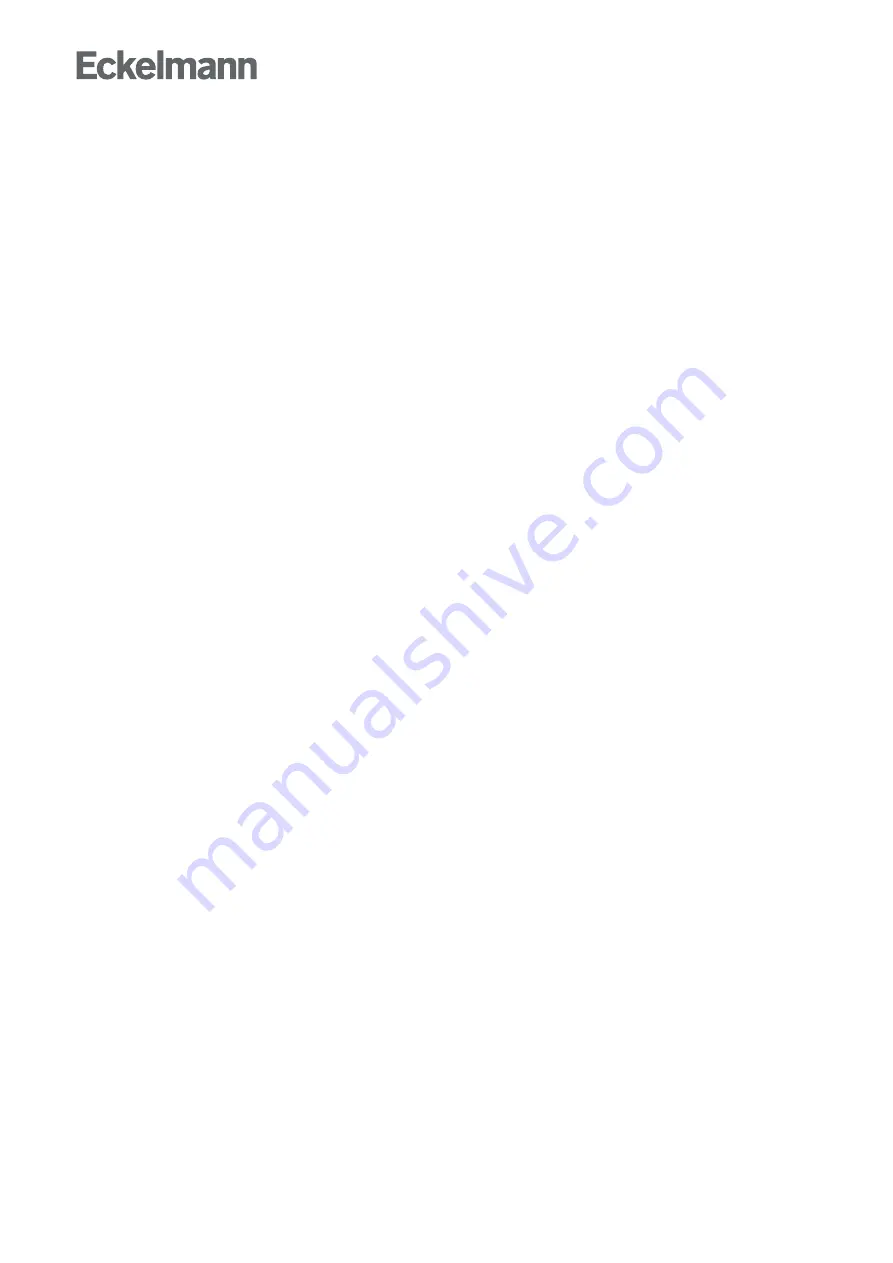
Firmware V3.15
21.04.2021
41/401
1.
2.
3.
4.
5.
•
•
•
•
•
•
The slaves, with respect to the parameter “
M/S Abt Fkt
” are set to “
Slave
”. The parameter “
M/S CAN Adr.
”
must
be set to the CAN address of the master controller, and that for all participating slave controllers.
Application special case - Synchronisation of both defrost zones
If the M/S CAN address on a slave is set to “—“, then a defrost via internal and external defrost timers is
possible. This enables both zones of the respective controller to be synchronised so that they return to cooling
simultaneously following the defrost.
Short guide
Set which controllers should defrost or switch to cooling together. Define one of the controllers as the defrost
master.
Configure the defrost master (e.g. controller with CAN address 11) as follows: under 2 Setpoints - 2 Defrost
- 1 Zone 1:
1. Set M/S Abt. Fkt.Master and
2. M/S CAN Adr. to "--"
Configure all slaves as follows: under 2 Setpoints – 2 Defrost – 1 Zone 1:
1. Input M/S Abt. Fkt Slave and
2. M/S CAN Adr. (CAN address of the master, e.g. 11)
Configure defrost on the master,
1. safe defrost time and defrost times or external defrost in menu 3 Clock - 2 Defrost timer (note: during
master / slave operation, the controller always reacts to the external defrost timer even if defrost timer has
been set to INT).
2. defrost termination temperature, wait time and drip time for zones 1 and 2 in the menus 2-2-1 and 2-2-2
(note: the slaves adopt the wait time and the drip time from the corresponding zones of the master. If the
master should operate in single-zone mode, a slave in two-zone mode adopts the wait time and drip time
from zone 1 of the master for for both zones).
Check whether the sensor for the defrost termination temperature (R1.x) is connected and is supplying
plausible values.
Necessary measures for the parametrisation of the master/slave defrost via CAN bus
The safe defrost time of the master is also applicable for the slave controllers. Possibly deviating values set
at the slave controllers are not taken into account:
The wait and drip times of the master are also applicable for the slave controllers. Possibly deviating values
set at the slave controllers are not taken into account:
The initiation of a defrost (manual, external, internal, CAN) on a slave node is not permitted and will be
prevented.
Exception: Slaves with the M/S CAN address = “—“ can have external defrost sources (see Special
Application Case).
The defrost on demand only functions on the master. Any possibly parametrised defrost on demand for the
slave controllers will be ignored.
The defrost termination temperature must be set individually for each slave controller.
Status values
The total number of controllers participating in the master/slave process is displayed in menu 1-3 (parameter
"
M/S Anz. Sl.
"). The number is recalculated with each reset and setting of the parameter "
M/S Abt Fkt
" to
"
Master
".
In addition, menu 1-3 also displays the last UA that did not give any feedback to the master during defrost
(parameter "M/S verl. Sl."). If the defrost proceeded without error, this value is "--".
If a defrost is requested at the master (defrost timer, manual or external) and the master itself has already
reached the defrost termination temperature, it does not defrost and defrosting of the slaves is not initiated at
all.
Behaviour of a Master/Slave CAN slave when it receives a defrost request from a master and the defrost
condition is not fulfilled (slave too warm): the slave does not defrost and does nor cool while the cooling
remains blocked by the master.
Summary of Contents for UA 400
Page 26: ...Firmware V3 15 21 04 2021 26 401 Solenoid valve Relay for Solenoid Valve 1 ...
Page 172: ...Firmware V3 15 21 04 2021 172 401 Service Mode 6 7 2 SERVICE MOD ...
Page 244: ...Firmware V3 15 21 04 2021 244 401 ...
Page 361: ...Firmware V3 15 21 04 2021 361 401 FANS 2 Pos XXXXX Fan Delay Fan delay ...
Page 372: ...Firmware V3 15 21 04 2021 372 401 ...