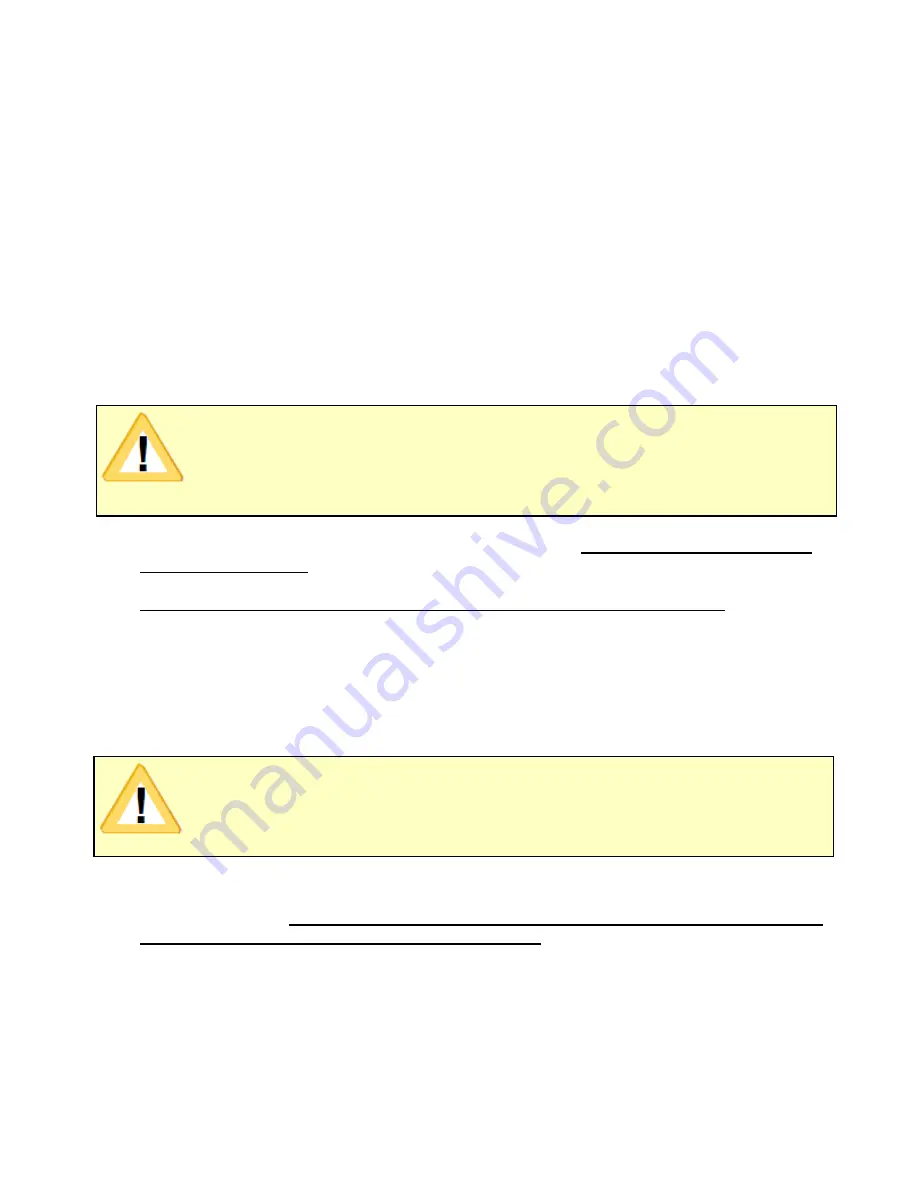
SCWD-QS (12/16)
Page 40
2) Evacuation
Refer to Figure 25 and the following procedure:
1. Carefully vent any pressurized nitrogen charge from the compressor unit and system.
2. After venting the pressurized system, use a good quality gauge manifold and a non-permeable
hose set as shown in Figure 25. If possible, use two Schrader core removal tools. Install one
on the discharge line access port and the other on the initial charging port. Removal of the
Schrader cores will reduce the time to achieve the desired vacuum.
3. Attach a good quality digital vacuum gauge with an isolation valve to the liquid line service
valve access port as shown in Figure 25.
4. Use a well maintained, high quality vacuum pump with an isolation valve, rated at 7 cfm or
greater connected to the gauge manifold. Ensure that the vacuum pump oil has been changed
prior to initiating the evacuation process to avoid contamination.
5. Fully open the LP and HP valves and both service valves. Reference Figure 25.
6. Open the vacuum pump isolation valve and start the pump.
Evacuate the system down to
400 MICRONS or less
as read on the digital vacuum gauge. After 400 microns or less has
been achieved, isolate the vacuum pump. Wait 5 minutes and read the digital vacuum gauge.
The system pressure must not exceed 500 MICRONS WITHIN 15 MINUTES.
If it does,
continue the evacuation to remove any remaining non-condensibles in the system. A dry
system will hold 500 microns for 15 minutes.
A procedure often used to evacuate a system, known as the triple evacuation method, is
detailed in the section of this manual entitled
Triple Evacuation
.
Local codes may require other evacuation criteria, in which case the local codes take
precedence over the evacuation requirements described above.
7. When the system has been successfully evacuated, close the LP and HP valves on the
manifold gauge set.
Do not remove the manifold gauge set or hoses, as air will be drawn
into the system and defeat the evacuation process.
IMPORTANT!
DO NOT ENERGIZE THE COMPRESSOR WHILE THE SYSTEM IS UNDER
VACUUM. THIS WILL CAUSE DAMAGE TO THE COMPRESSOR.
IMPORTANT!
DO NOT CHARGE THE SYSTEM UNTIL THE CONDITIONS OF STEP #6
ARE COMPLETED!
Summary of Contents for SCWD-024-1C
Page 15: ...SCWD QS 12 16 Page 15 Figure 7 SCWD Compressor Unit Electrical Schematic Diagram 230 1 60...
Page 16: ...SCWD QS 12 16 Page 16 Figure 8 SCWD Compressor Unit Electrical Schematic Diagram 230 3 60...
Page 17: ...SCWD QS 12 16 Page 17 Figure 9 SCWD Hydronic Heating Cooling Water Heating Sytem Application...
Page 20: ...SCWD QS 12 16 Page 20 Figure 11 SureStart Mode of Operation...
Page 31: ...SCWD QS 12 16 Page 31 Figure 14 Disassembled Plug Connector...
Page 38: ...SCWD QS 12 16 Page 38 Figure 23 SCWD Internal Flow Schematic...
Page 39: ...SCWD QS 12 16 Page 39 Figure 24 SCWD Piping...
Page 41: ...SCWD QS 12 16 Page 41 Figure 25 Evacuation of SCWD System...
Page 43: ...SCWD QS 12 16 Page 43 Figure 26 Initial Charge of SCWD System...
Page 45: ...SCWD QS 12 16 Page 45 Figure 27 Final Charge of SCWD System...
Page 48: ...SCWD QS 12 16 Page 48 Figure 31 Start Up Process...