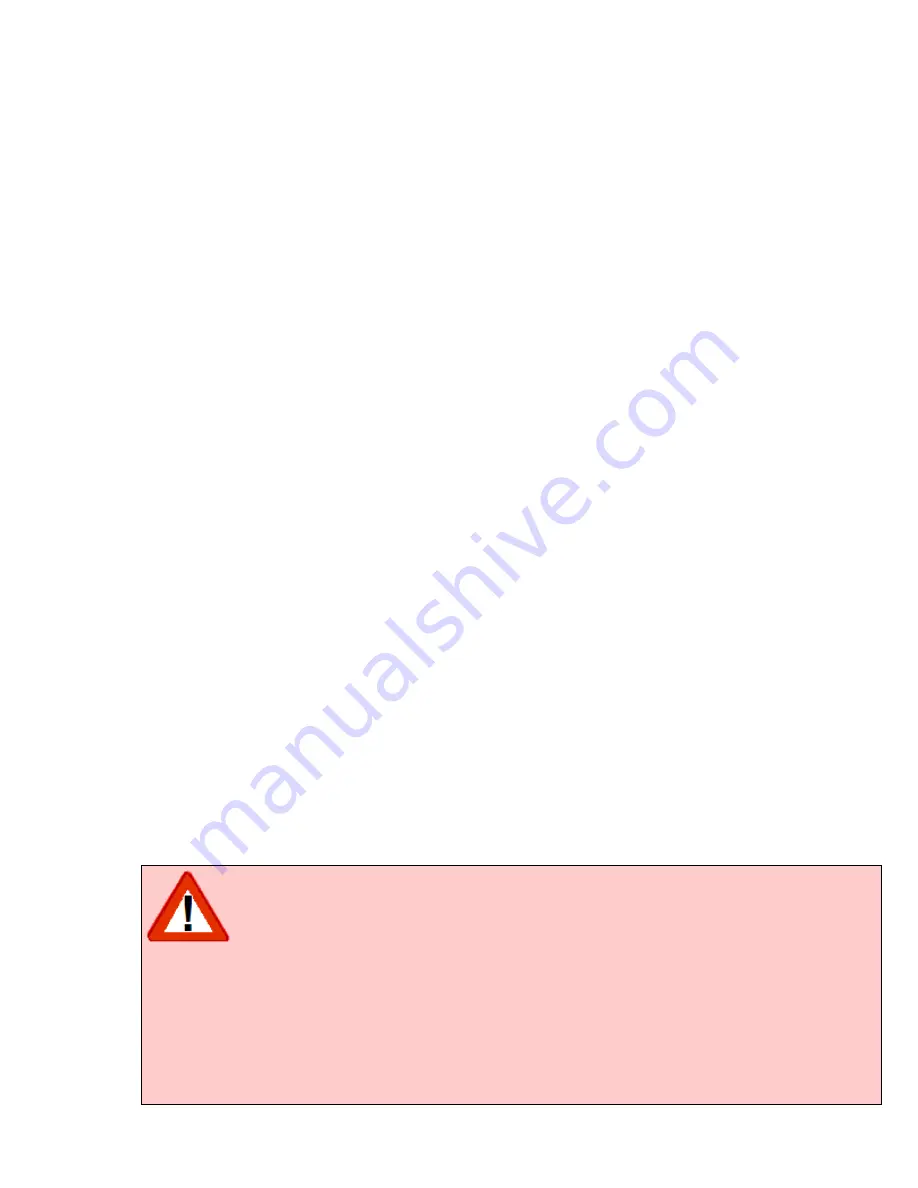
SCWD-QS (12/16)
Page 24
The components are as follows:
1.
Circulating Pump:
The recommended circulating pump can be purchased from EarthLinked
as part of the Pump kit (PU-KIT) composed of the Pump, Pump Flange Set and Pump
Mounting Brackets. Any field supplied pump must supply a
design (minimum) water flow
rate of 3 gpm per nominal ton
of refrigeration for the system to perform properly. This
flow
rate will be adjusted upward
to maintain system heat transfer performance for the specific
antifreeze mixture. See the section entitled
Antifreeze Protection
for details.
To determine the appropriate hydronic antifreeze solution flow rate through the compressor
unit heat exchanger, begin by fastening thermocouples securely on the water supply and
water return copper stub outs of the compressor unit, isolating them from the ambient air, in
locations shown in Figure 12a. After the system has run for 10 minutes, determine the
temperature differential between the hydronic supply temperature and the return
temperature.
The solution water flow rate is correct if the temperature
differential is in the
range of 4°F to 7°F.
Flow rate can be increased or decreased by adjusting the hydronic
supply isolation valve.
2.
Three-Way Zone Valve:
This electrically operated zone valve is a commercially available
hydronic system component that directs the hydronic fluid flow in response to the system
operating mode, either heating or cooling.
3.
Strainer:
Models ST-1836 (for 1.5 thru 3.0 ton systems) and ST-4272 (for 3.5 thru 6.0 ton
systems) are 20 mesh, brass, inline strainers, available from ETI and necessary to trap
particles and maintain proper flow through the brazed plate heat exchanger channels.
4.
Temperature Controller:
Model HHK-1872 is a hydronic heating controller and Model CWK-
1872 is a chilled water temperature controller. These digital controllers can be mounted
remotely and come with a Sensor Wire 6.5 feet long, Immersion well, thermal paste and are
available from ETI.
5.
Hydronic Buffer Tank:
The GSTE Series Hydronic Buffer Tanks are available from ETI in 60,
80 and 119 US Gallon capacities, and are designed for use with the EarthLinked
®
geothermal
systems. They are equipped with a 4.5 kW supplemental heater which satisfies the ETI
requirement for a minimum of 20% supplemental heat.
6.
Other Plumbing Components and Parts:
Gate valves, unions, copper pipe, pipe insulation,
etc. meeting USA industry and local code standards are commercially available through
plumbing supply outlets.
All plumbing installations are to be in accordance with the applicable local and national codes.
To protect the brazed plate heat exchanger
from damage during cooling operation when
the heat exchanger is producing chilled water, a factory installed thermal switch at the outlet of
the heat exchanger will turn the compressor OFF when the chilled water temperature drops to
38°F. An auxiliary lower temperature thermostat is available. It is field-ordered and installed.
WARNING!
The heat exchanger must be isolated from the water system when the
system undergoes a “superchlorination” or “shock chlorination”
flushing process. Closing the isolation valves prior to initiating the
system flushing process isolates the heat exchanger. The water
entering the heat exchanger after the system flushing must not exceed a
chlorine level consistent with the local municipal water purification
standards. Failure to isolate the heat exchanger will damage the heat
exchanger causing system failure. Allowing highly chlorinated water to
enter the heat exchanger will void the EarthLinked
®
Limited Warranty.
Summary of Contents for SCWD-024-1C
Page 15: ...SCWD QS 12 16 Page 15 Figure 7 SCWD Compressor Unit Electrical Schematic Diagram 230 1 60...
Page 16: ...SCWD QS 12 16 Page 16 Figure 8 SCWD Compressor Unit Electrical Schematic Diagram 230 3 60...
Page 17: ...SCWD QS 12 16 Page 17 Figure 9 SCWD Hydronic Heating Cooling Water Heating Sytem Application...
Page 20: ...SCWD QS 12 16 Page 20 Figure 11 SureStart Mode of Operation...
Page 31: ...SCWD QS 12 16 Page 31 Figure 14 Disassembled Plug Connector...
Page 38: ...SCWD QS 12 16 Page 38 Figure 23 SCWD Internal Flow Schematic...
Page 39: ...SCWD QS 12 16 Page 39 Figure 24 SCWD Piping...
Page 41: ...SCWD QS 12 16 Page 41 Figure 25 Evacuation of SCWD System...
Page 43: ...SCWD QS 12 16 Page 43 Figure 26 Initial Charge of SCWD System...
Page 45: ...SCWD QS 12 16 Page 45 Figure 27 Final Charge of SCWD System...
Page 48: ...SCWD QS 12 16 Page 48 Figure 31 Start Up Process...