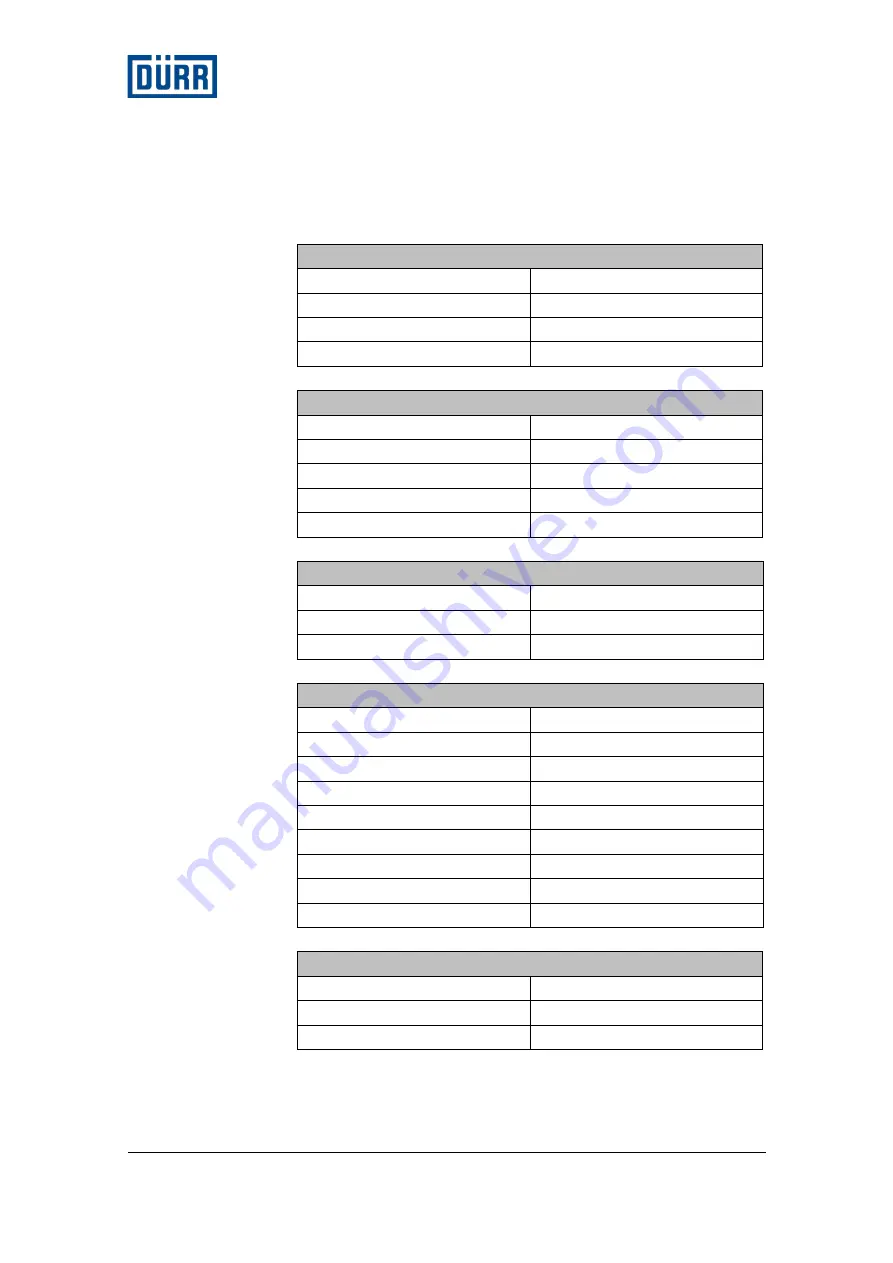
Operating Manual
© Dürr Systems AG
142 / 156
EcoBell2 SL EC - Rotating Atomizer with External Charging
Technical Data
Document No.: MRA00001EN
Version:: 07
•
As of:: 01/2020
11
Technical Data
Dimensions and weight
Length (without bell disk)
283 mm
Flange diameter
165 mm
Electrodes diameter
244 mm
Weight
6.5kg
Air consumption at 6 bars dynamically
Motor air
100 – 730Nl/min
Motor bearing air
approx. 50 Nl/min
Shaping air 1
450Nl/min max.
Shaping air 2
440Nl/min max.
Typical operating range of shaping air
100 – 350Nl/min
Rotational speed
Maximum
70000 ± 500 RPM
Usable range
8000 – 70,000 RPM
Typical range
15,000 – 55,000 RPM
Compressed air, dynamic
Control air valves, min.
6 bar
Control air valves, max.
8 bar
Motor air, min
6 bar
Motor air, max
8 bar
Break air
6 bar
Motor bearing air, min
6 bar
Motor bearing air, max
7 bar
Shaping air, min.
6 bar
Shaping air, max
8 bar
Paint flow rate
Max. outflow rate
700ml/min
At a rotational speed of 70,000 RPM
400 ml/min max.
Typical range
80 – 350ml/min