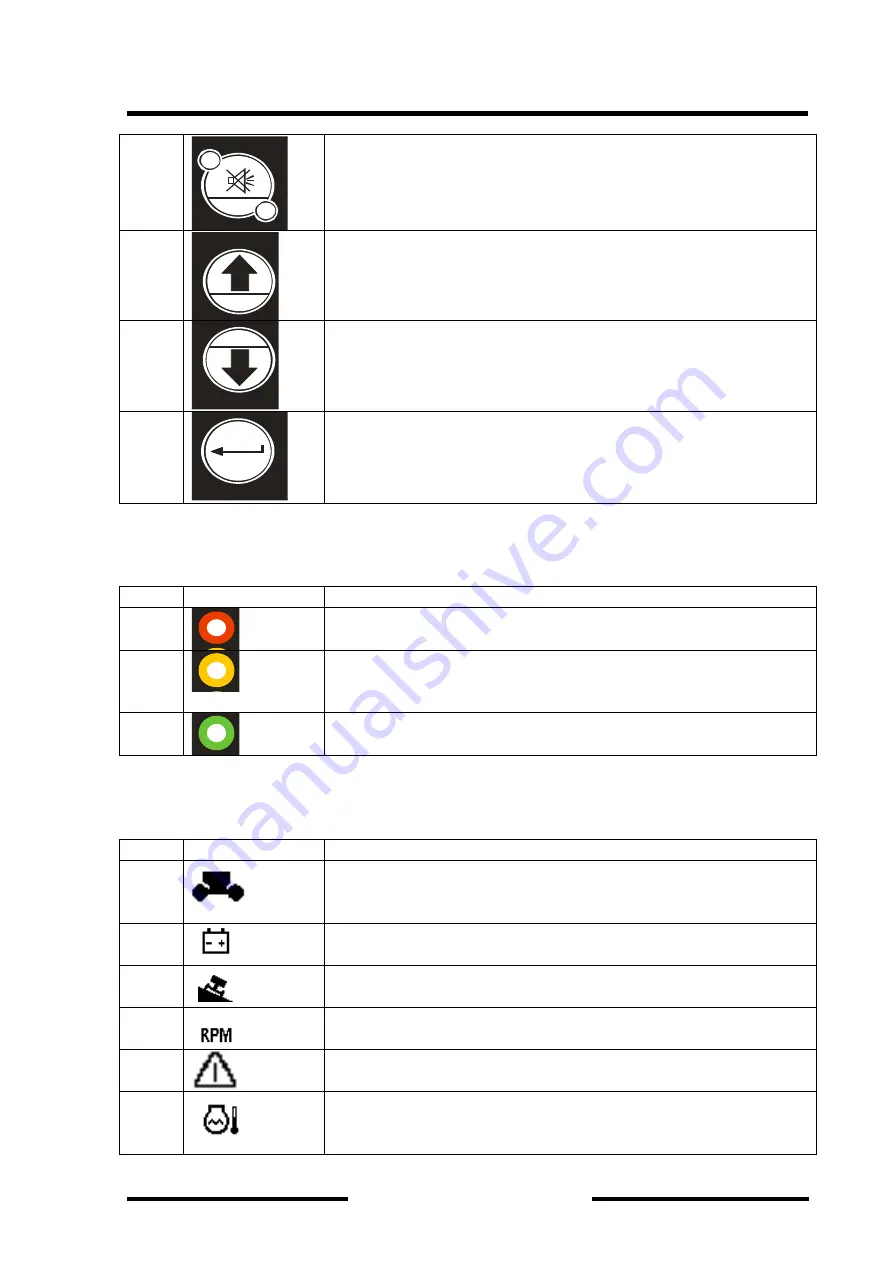
Operation & Maintenance Manual Section4-Machine Controls and Indicators
Dingli Machinery
4-13
1
Enter
ACT
a
r
h
l
STOP
Index
+
-
It is used to adjust the display panel contrast, press one time
2
Enter
ACT
a
r
h
l
STOP
Index
+
-
Go back to up class menu or display item. It is used to choose
previews item when adjust the display menu
3
Enter
ACT
a
r
h
l
STOP
Index
+
-
Go down to the next display item. It is used to choose next item
when adjust the display menu
4
Enter
ACT
a
r
h
l
STOP
Index
+
-
It is used to confirm you choosing when make adjusting for the
control display
Indicator Light Description:
Item
Name & Figure
Description
1
Enter
ACT
a
r
h
l
STOP
Index
+
-
It is a red indicator light. It indicates that there are some warnings
when it is illustrated.
2
Enter
ACT
a
r
h
l
STOP
Index
+
-
It is a yellow indicator light. It indicates that the driving motor is
in minor display and the machine can be drove in High speed
when it is illustrated.
3
Enter
ACT
a
r
h
l
STOP
Index
+
-
It is a green indicator light. It indicates that the footswitch is
depressed when it is illustrated.
The Icon in the Graphic Display Zone Description:
Item
Name & Figure
Description
1
The ground control station indicator. It would be shown when the
selected key switch is turned to the ground control station.
2
Indicate that the engine is turn off.
3
Indicate that the machine chassis is inline and the degree more
that 3 degree.
4
Indicate that the engine is in High speed working status.
5
Indicate that the emergency button is depressed down.
6
Indicate that the engine coolant temperature is more105 degree.
Stop the engine immaterially and make a troubleshooting.
Summary of Contents for BA14J-AWD
Page 1: ...Operation Maintenance Manual Table of Contents Dingli Machinery i Series 1 ...
Page 51: ...Operation Maintenance Manual Section4 Machine Controls and Indicators Dingli Machinery 4 17 ...
Page 52: ...Operation Maintenance Manual Section4 Machine Controls and Indicators Dingli Machinery 4 18 ...
Page 53: ...Operation Maintenance Manual Section4 Machine Controls and Indicators Dingli Machinery 4 19 ...
Page 84: ...Operation Maintenance Manual Section8 Schematics Dingli Machinery 8 2 ...
Page 85: ...Operation Maintenance Manual Section8 Schematics Dingli Machinery 8 3 ...
Page 86: ...Operation Maintenance Manual Section8 Schematics Dingli Machinery 8 4 ...
Page 87: ...Operation Maintenance Manual Section8 Schematics Dingli Machinery 8 5 ...
Page 88: ...Operation Maintenance Manual Section8 Schematics Dingli Machinery 8 6 ...
Page 89: ...Operation Maintenance Manual Section8 Schematics Dingli Machinery 8 7 ...
Page 90: ...Operation Maintenance Manual Section8 Schematics Dingli Machinery 8 8 ...
Page 91: ...Operation Maintenance Manual Section8 Schematics Dingli Machinery 8 9 ...
Page 92: ...Operation Maintenance Manual Section8 Schematics Dingli Machinery 8 10 ...
Page 93: ...Operation Maintenance Manual Section8 Schematics Dingli Machinery 8 11 ...
Page 94: ...Operation Maintenance Manual Section8 Schematics Dingli Machinery 8 12 ...
Page 95: ...Operation Maintenance Manual Section8 Schematics Dingli Machinery 8 13 ...
Page 96: ...Operation Maintenance Manual Section8 Schematics Dingli Machinery 8 14 ...
Page 97: ...Operation Maintenance Manual Section8 Schematics Dingli Machinery 8 15 ...