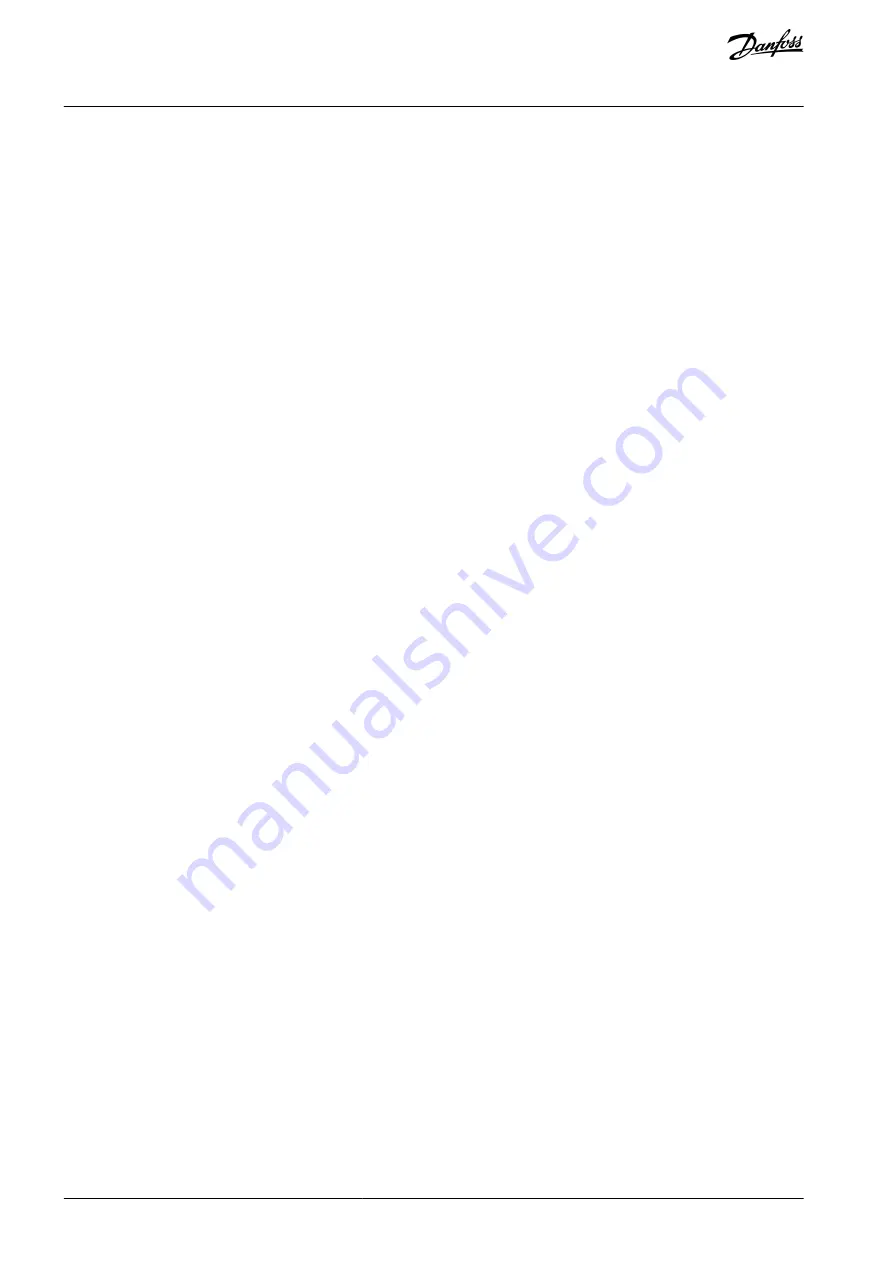
•
•
•
•
•
•
•
•
•
•
•
•
There is a mismatch of the resolver/ motor pole pair number. Resolver pole pair number (if >1) is not matching the motor pole pair
number.
Troubleshooting
Check that OPTBC parameter “Resolver Poles” and possible Gear Ratio parameters in application match motor pole count.
12.10.112 Fault 43 - Encoder fault, Subcode S9 - Missed Start Angle
Cause
Encoder zero positioning identification run has not been made.
The encoder start angle is missing.
Troubleshooting
Make encoder identification run.
12.10.113 Fault 43 - Encoder fault, Subcode S10 - Sin/Cos encoder feedback is missing
Cause
Problem detected in encoder signals.
For the closed loop control, encoder modes "EnDat only" or "SSI only" (absolute channel only) are not allowed.
Troubleshooting
Do a check of the wiring, jumper settings, and encoder mode.
Change OPTBE “Operating mode” parameter is either "EnDat+SinCos", "SSI+SinCos" or "SinCos only", or avoid using closed loop
control.
12.10.114 Fault 43 - Encoder fault, Subcode S11 - Encoder angle is drifting
Cause
Error angle between the angle read from the absolute channel and the angle calculated from the incremental channels.
Troubleshooting
Check the encoder cable, cable shield, and grounding of the cable shield.
Check the mechanical mounting of the encoder and make sure that the encoder is not slipping.
Check the encoder parameters (for example, encoder ppr).
12.10.115 Fault 43 - Encoder fault, Subcode S12 - Dual speed supervision fault
Cause
Encoder speed supervision. The difference between the encoder speed and estimated speed is too large. Dual speed supervision:
Estimated speed and encoder speed difference is too high (0.05 x f
n
or minimum motor nominal slip frequency). See variable Esti-
matedShaftFrequency.
Troubleshooting
Check the encoder speed signal ShaftFrequency vs. EstimatedShaftFrequency.
If the ShaftFrequency is incorrect, check the encoder, cable, and encoder parameters.
If the EstimatedShaftFrequency is incorrect, check the motor parameters.
12.10.116 Fault 43 - Encoder fault, Subcode S13 - Encoder angle supervision fault
Cause
The estimated shaft position error (estimated angle - encoder angle) is more than 90° electrical.
See variable EstimatedAngleError.
Troubleshooting
Repeat the encoder ID run (absolute encoders).
Check the mechanical mounting of the encoder and make sure that the encoder is not slipping.
Check the encoder ppr number.
Check the encoder cable.
12.10.117 Fault 43 - Encoder fault, Subcode S14 - Encoder estimated missing pulse fault, switch
from the CL ctrl to the OL sensorl
Cause
Problem detected in encoder signals.
AQ275638903263en-000601 / DPD00910
190 | Danfoss A/S © 2022.12
Specifications
VACON® NXS/NXP Air-cooled
Operating Guide