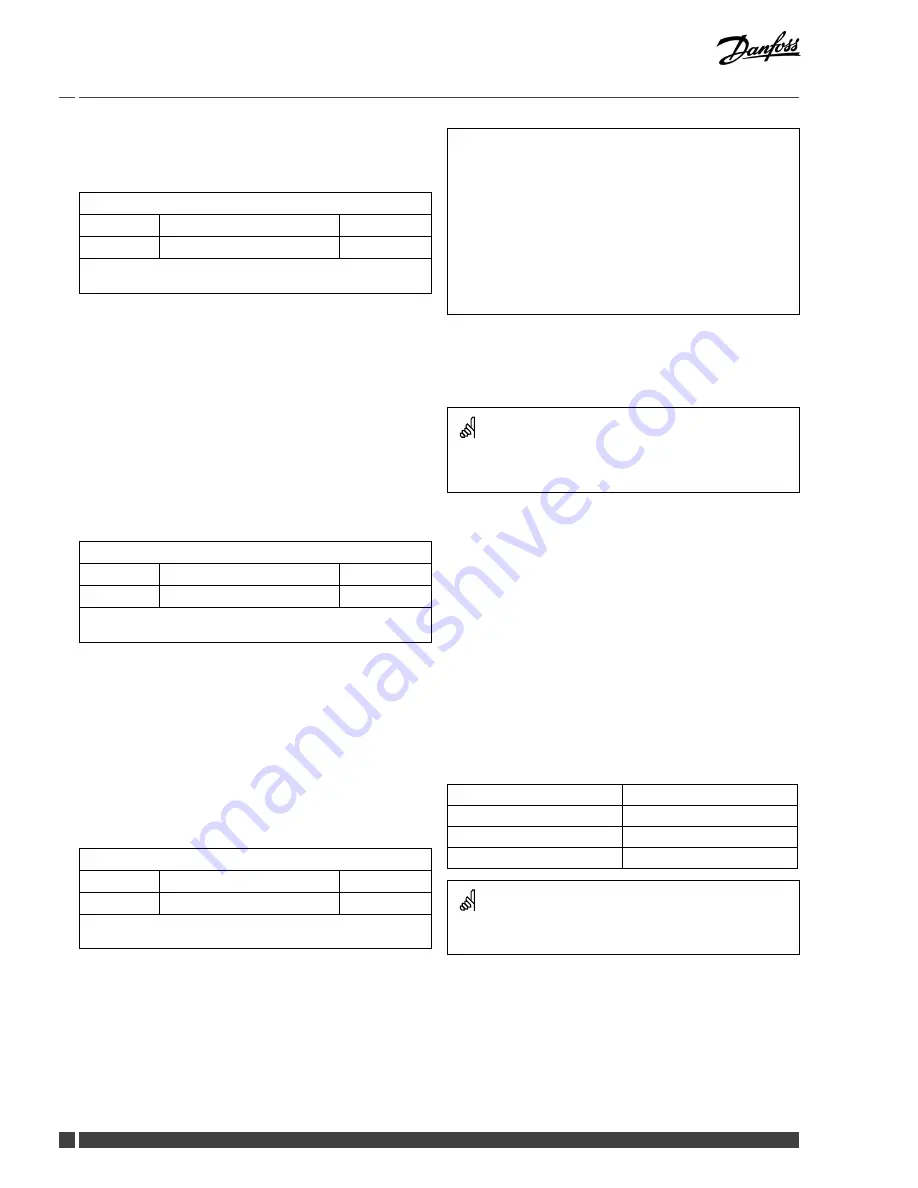
Installation Guide
ECL Comfort 210 / 310, application A214 / A314
MENU > Settings > Control par.
MENU > Settings > Control par., cool.
MENU > Settings > Control par. 1
MENU > Settings > Control par. 2
M run (running time of the motorized control valve)
1x186
Circuit
Setting range
Factory setting
All
*
*
‘M run’ is the time in seconds it takes the controlled component to move
from fully closed to fully open position.
* See Appendix “Parameter ID overview”
Set the ‘M run’ according to the examples or measure the running
time by means of a stop watch.
How to calculate the running time of a motorized control valve
The running time of the motorized control valve is calculated using
the following methods:
Seated valves
Running time = Valve stroke (mm) x actuator speed (sec. / mm)
Example:
5.0 mm x 15 sec. / mm = 75 sec.
Rotating valves
Running time = Turning degrees x actuator speed (sec. / degr.)
Example:
90 degr. x 2 sec. / degr. = 180 sec.
MENU > Settings > Control par.
MENU > Settings > Control par., cool.
MENU > Settings > Control par., fan
MENU > Settings > Control par., inlet
MENU > Settings > Control par., outlet
MENU > Settings > Control par., P circ.
MENU > Settings > Control par., P refill
MENU > Settings > Control par. 1
MENU > Settings > Control par. 2
Nz (neutral zone)
1x187
Circuit
Setting range
Factory setting
All
*
*
When the actual flow / duct temperature is within the neutral zone, the
controller does not activate the motorized control valve.
* See Appendix “Parameter ID overview”
Set the acceptable flow /duct temperature deviation.
Set the neutral zone to a high value if you can accept a high
variation in flow temperature.
The neutral zone is symmetrical around the desired flow / duct
temperature value, i.e. half the value is above and half the value is
below this temperature.
MENU > Settings > Control par.
MENU > Settings > Control par., cool.
MENU > Settings > Control par. 1
MENU > Settings > Control par. 2
Min. act. time (min. activation time gear motor)
1x189
Circuit
Setting range
Factory setting
All
*
*
The min. pulse period of 20 ms (milliseconds ) for activation of the gear
motor.
* See Appendix “Parameter ID overview”
Setting example
Value x 20 ms
2
40 ms
10
200 ms
50
1000 ms
The setting should be kept as high as acceptable to increase the
lifetime of the actuator (gear motor).
136
DEN-SMT/DK
VI.GU.A2.02
Danfoss District Energy