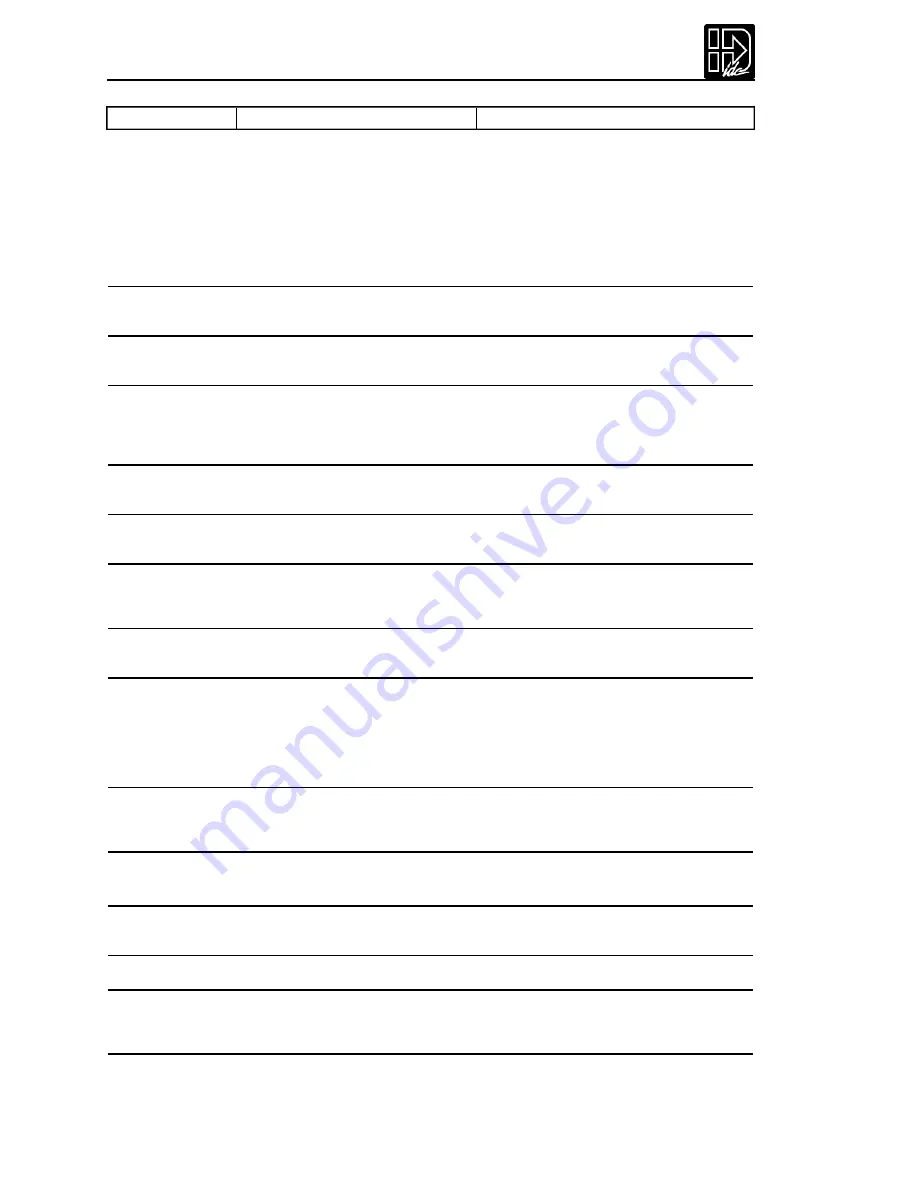
B8961 and B8962 User Manual
138
Symptoms
Probable Causes
Possible Remedies
RMS Shutdow n
Mechanical jam,amplifier shut down to
Check for binding or reduce
prevent motor overheating.
acceleration and duty cycle.
Vertical or constant force application
Contact IDC’s application dept.
causing false RMS fault.(DSP V1.6
only)
Load correct file via Servo Tuner.
RMS current limit exceeded.
Check for binding or reduce
acceleration and duty cycle.
Wrong motor file loaded.
Select the correct motor model AND
voltage from SETUP/MOTOR/TYPE.
“Hit a Limit”
Limit switches improperly wired or
EOT inputs must be connected to
error message
not connected
COM via a jumper wire or a NC
switch before motion can take place.
Motor moves the
Drive and control resolution
Check the distance units and the Gear
wrong distance
don’t match
Ratio setting in the
EDIT/SETUP/MECH menu.
Controller doesn’t
The keypad has been disabled
Check the dipswitch settings on the
respond to keypad
back of the keypad to selectively
inputs
disable keypad functionality.
Check for “keypad disable”input
configuration.
Controller doesn’t
OPTO positions default to inputs.
Configure as output from the
recognize OPTO
EDIT/SETUP/I/O menu.
inputs
No motion occurs
Correct motor type not selected.
Select the correct motor and voltage from
when programs are
Motor type defaults to NONE.
the SETUP/MOTOR/TYPE menu.
run
Homing moves are
Home switch active level set
Change home switch active level from the
very slow, don’t
incorrectly
SETUP/HOME/SWITCH menu.
follow commanded
velocity
Final homing position Homes to the Z-channel on the motor
Move the switch,the motor with respect to
is not located over
encoder
the switch,or run in OPEN LOOP MODE.
the home switch
Motor will not
Drive not enabled.
Check for drive faults with the keypad or the
move/has no
the SS command.
torque
End of travel limit switches are active
D ri ve re q u i res Norm a l ly Closed limit sw i t ch e s .
Inputs should be jumpered if not being used.
The MOTOR/TYPE selection is wro n g .
The default dri ve confi g u ration is “ N O N E .”
Select the correct motor and vo l t age from the
S E T U P / M OTOR/TYPE menu .
Motor “ j e rk s ”o n
Hall effect sensors mis-wire d
C h e ck fe e d b a ck cabl i n g
p ower up
W rong motor type selected
Select the correct motor and vo l t age from the
S E T U P / M OTOR/TYPE menu .
Motor “ w h i n e s ”
H i g h ly resonant mechanical system
S t i ffen the mechanical tra n s m i s s i o n
Tuning para m e t e rs are set too “ h o t ”
Reduce the gain para m e t e rs . K
i
is often a
s t rong contributor to this instab i l i t y.
Motor won’t change One EOT limit switch is active
Check limit switch wiring or motor/actuator
direction or moves
position.
only in one direction
Motor moves in the
Control and Drive directions conflict
Change the direction from the
wrong direction
with each other
SETUP/MOTOR/DIR menu.
Motor runs hot
High accelerations and duty cycles.
Reduce duty cycle.Motor heating is not
IDC motors are rated
normally a problem unless it causes
up to a case temp of 100C,and are
Thermal Shutdowns.
protected by a thermostat.
Summary of Contents for B8961
Page 111: ...109 Chapter 7 Programming with Serial Communication...
Page 132: ...B8961 and B8962 User Manual 130...
Page 136: ...B8961 and B8962 User Manual 134 B8961 and B8962 Hardware Connections...
Page 137: ...135 Chapter 8 Hardware Reference B8961 and B8962 Input and Output Schematics...
Page 138: ...B8961 and B8962 User Manual 136 Connecting IDC Limit Switches to the B8961 2...
Page 156: ...B8961 and B8962 User Manual 154...