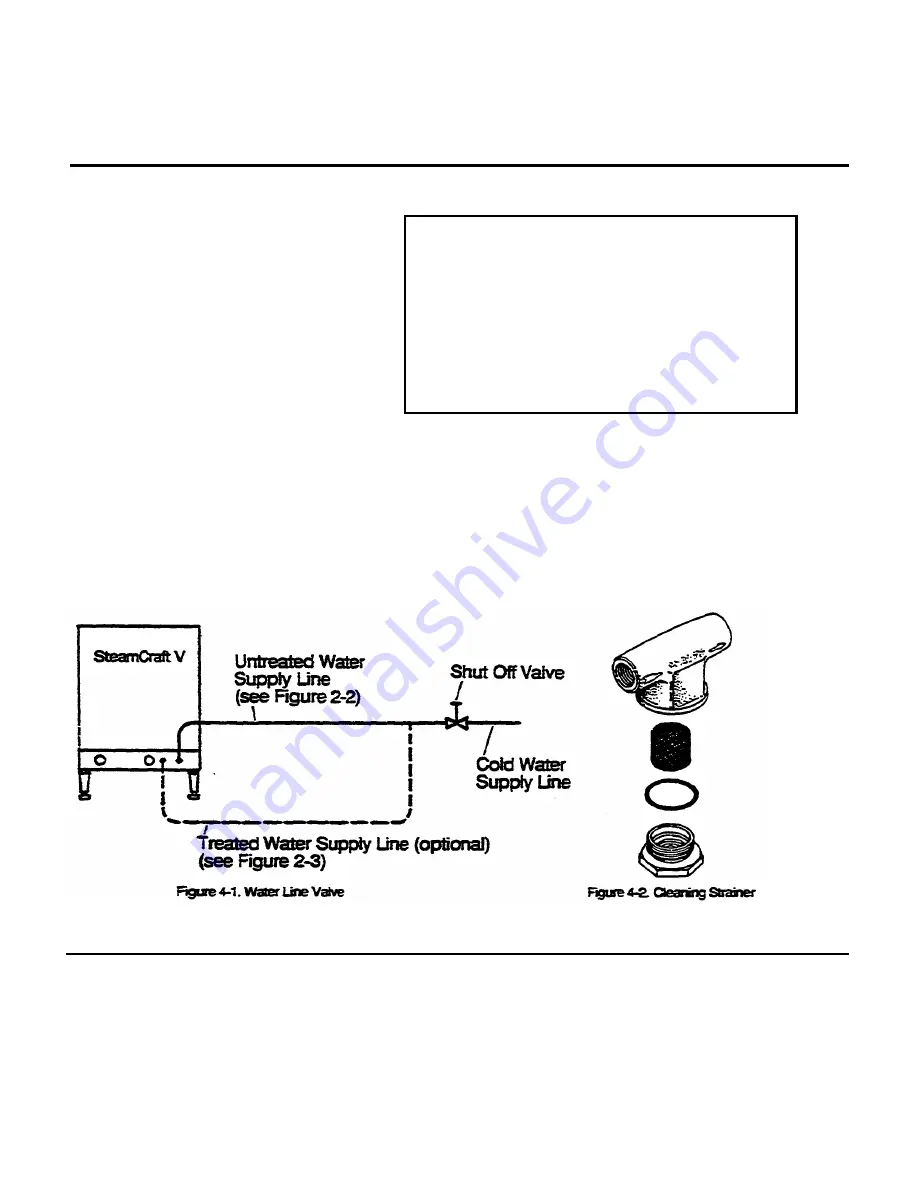
Page 48
CET-16 Service Manual
WEEKLY MAINTENANCE
WARNING
The steamer is equipped with a drain screen i
n
the back
of the cooking compartment. The steamer should never
be operated without the screen in place. This screen
prevents large food particles from entering and possibly
blocking the drain fine. Any blockage of the drain fine
may cause a slight buildup of back pressure in the
compartment resulting in steam leaks around the door
gasket. It also may adversely affect the convection
action of the steam in the compartment, which is neces-
sary for optimum performance.
1
.
Make sure the drain screen and drain line are not blocked. Pour USDA
approved drain cleaner through drain once a week.
2
.
Inspect for steam generator scale weekly. The frequency of steam
generator descaling depends upon water quality and daily steam
generator drain and washout. If steam generator scale buildup is a
frequent problem, install a water treatment system for the steamer. See
Water Quality Requirements on page 6.
3. Regardless of use, steam generator should be descaled at least once a
month. See Steam Generator Descaling Procedure below.
YEARLY MAINTENANCE
Clean the water line filter at least once a year as follows:
1. Close the valve in the steamer water line
.
Refer to figure 4-1.
2.
Unscrew the filter from the bottom of the strainer which is located in
back of the steamer. Refer to figure 4-2.
Printed 4/90
Summary of Contents for SteamCraft V
Page 56: ...Page 54 CET 16 Service Manual Figure 5 1 Block Diagram Printed 4 90...
Page 59: ...CET 16 Service Manual Page 57 Figure 5 2 Control Board Printed Circuit Board Printed 4 90...
Page 73: ...Page 72 CET 16 Service Manual Figure 6 1 MAJOR COMPONENT GROUPS...
Page 80: ...CET 16 Service Manual Page 79 Figure 6 6 ELECTRICAL COMPONENTS ASSEMBLY Printed 4 90...
Page 82: ...CET 16 Service Manual Page 81 Figure 6 7 FAN ASSEMBLY Printed 4 90...
Page 84: ...CET 16 Service Manual Page 83 Figure 6 8 CONDENSER AND DRAINAGE SYSTEMS Printed 4 90...
Page 86: ...CET 16 Service Manual Page 85 Figure 6 9 STEAM GENERATOR ASSEMBLY Printed 4 90...
Page 88: ...CET 16 Service Manual Page 87 Figure 6 10A DOUBLE WATER INLET ARRANGEMENT Printed 4 90...
Page 90: ...CET 16 Service Manual Page 89 Figure 6 10B SINGLE WATER INLET ARRANGEMENT Printed 4 90...