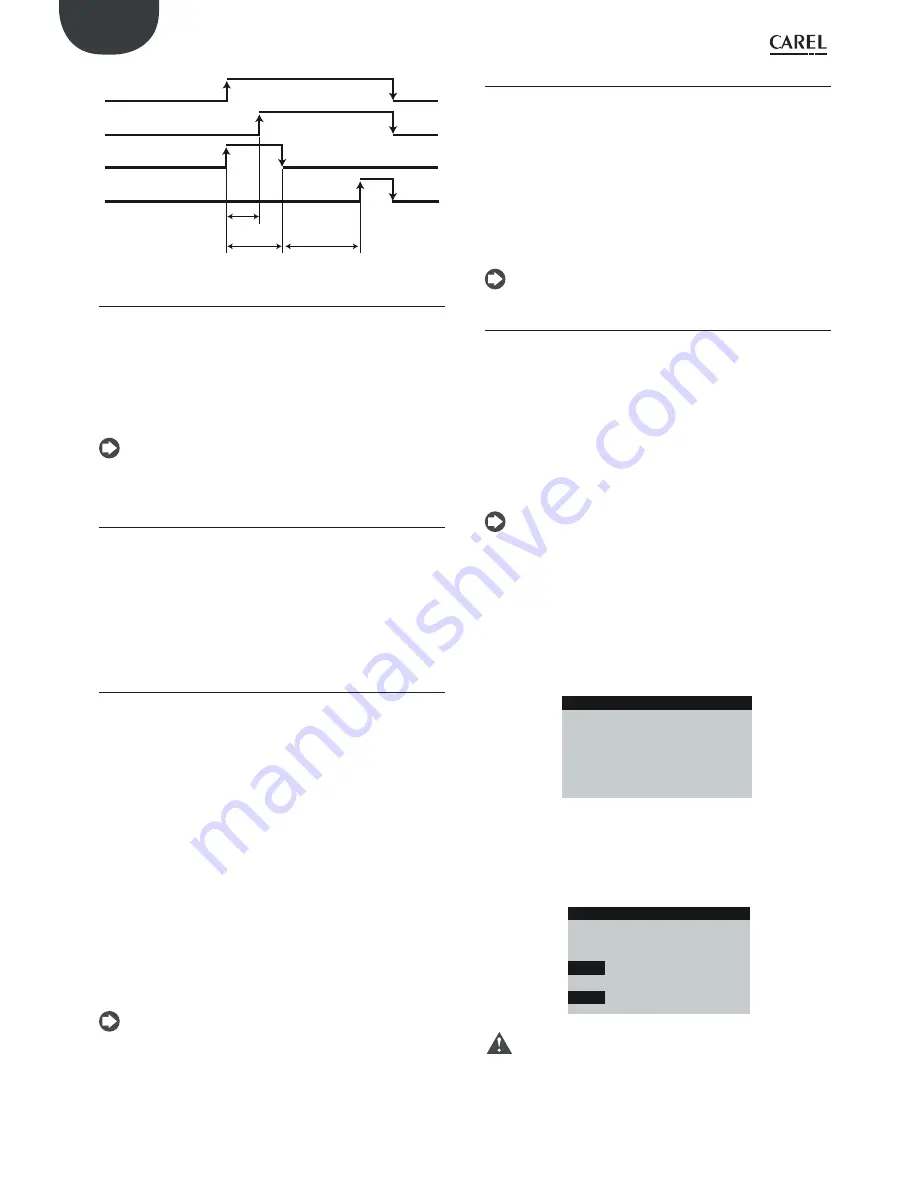
38
ENG
pRack +0300025EN rel. 1.3 - 17.12.2015
Compressor request
Line
Star-line delay
Part-winding
Delta
Delay
Start-delta
delay
Fig. 6.o
6.3.5 Safety
times
pRack pR300 can manage common safety times for each compressor:
•
Minimum on time
•
Minimum off time
•
Minimum time between consecutive starts
In addition, pRack pR300 can manage the specifi c times for Digital Scroll™
compressors and screw compressors; for the descriptions see paragraphs
6.3.10 and 6.3.11. The related parameters can be set in main menu branch
C.a.f/C.b.f.
Note:
for two lines, a further delay can be set between starts of the
compressors on diff erent lines, so as to avoid Simultaneous starts.
See paragraph 6.6.6 for the detailed description of the synchronisation
function for two lines (DSS).
6.3.6 Balancing
pRack pR300 can control any balance valves in parallel with the
compressors.
This function can be used to activate a communicating solenoid valve
between compressor suction and discharge, for a set time, before each
individual compressor starts. In this way, the suction and discharge
pressure can be balanced and the compressor can be started in more
favourable conditions.
The balancing function can be enabled and the related activation time
set in main menu branch C.a.f/C.b.f.
6.3.7 Economizer
pRack pR300 can activate the economizer function to boost compressor
effi
ciency by injecting vapour. Some of the liquid is taken from the
condenser, expanded through a valve and then sent to a heat exchanger
to cool the liquid leaving the condenser. The resulting superheated
vapour is injected into a special section of the compressor.
The function can be enabled and the related parameters set in main
menu branch C.a.f.
The function can be enabled and the related parameters set in main
menu branch C.a.f.
The economizer is only effi
cient for high compressor activation capacities,
typically over 75 %, therefore the economizer function control valve is
only activated when exceeding a set threshold.
As the economizer tends to increase the condensing pressure, this needs
to be controlled to ensure the high condensing pressure alarm is not
generated. In addition, the injection of vapour decreases the discharge
temperature and so this value also needs to be monitored.
Consequently, the three conditions for activation of the economizer
function are:
•
Capacity above a set threshold
•
Condensing pressure below a set threshold (with reset diff erential)
•
Discharge temperature above a set threshold (with reset diff erential)
Note
: the function can be activated on a maximum of 6
compressors.
6.3.8 Liquid
injection
As an alternativ
e to the economizer, pRack pR300 can manage the
injection of liquid into the compressors (the two functions are alternative,
as the point of vapour injection into the compressor is the same).
The function can be enabled and the related parameters set in main
menu branch E.d.a.b/E.d.b.b.
Liquid injection is used to protect the compressor, and in fact decreases
the discharge temperature.
Operation is Similar to the economizer function, with the diff erence that
the expanded liquid is not sent to a heat exchanger, but rather directly
into the compressor. The function is only activated when the compressor
is on and the discharge temperature exceeds a set threshold (with
diff erential).
Note
: the function can be activated on a maximum of 6
compressors.
6.3.9 Manual
operation
pRack pR300 can manage 3 diff erent compressor manual operating
modes:
•
Enabling / disabling
•
Manual management
•
Output test
Enabling / disabling is managed in main menu branch C.a.f/C.b.f., while
manual management and the output test can be activated in main menu
branch B.b or B.c.
Enabling / disabling is used to temporarily exclude the compressors from
operation, to allow, for example, repair or replacement. The disabled
compressors are also excluded from rotation.
Note
: enabling is the only compressor manual operating mode
that can be activated when the unit is on.
Both manual management and the output test are enabled by parameter
and remain active for a set time after the last button is pressed, after
which the unit returns to normal operating mode.
Manual management is used to switch the compressors on or off
without observing the control needs, however still considering any safety
devices (alarms, safety times, starting procedures) and respecting the set
confi guration of the inputs/outputs.
The activation screen resembles the one shown in the fi gure and is used
to override the outputs relating to the operation of the selected device,
e.g. compressor 1:
Manual mng. Bba02
Digital
output
board1
Compressor 1
Force to:
OFF
The output test is used to activate or deactivate the outputs (where
necessary setting an output percentage for the analogue outputs),
without observing any type of safety feature.
The activation screen resembles the one shown in the fi gure and is used
to override the outputs on the pRack boards, in the order they physically
appear on the board (without links to the devices):
Test DO Bca10
Digital
output
board1
D01
NO OFF
D02
NO OFF
Important:
manual mode and the output test can only be
activated with the unit off .
Both manual mode and above all the output test must be used with
special care and by expert personnel to avoid damage to the devices.
Summary of Contents for PRK300D0E0
Page 2: ......
Page 4: ......
Page 6: ...6 ENG pRack 0300025EN rel 1 3 17 12 2015...