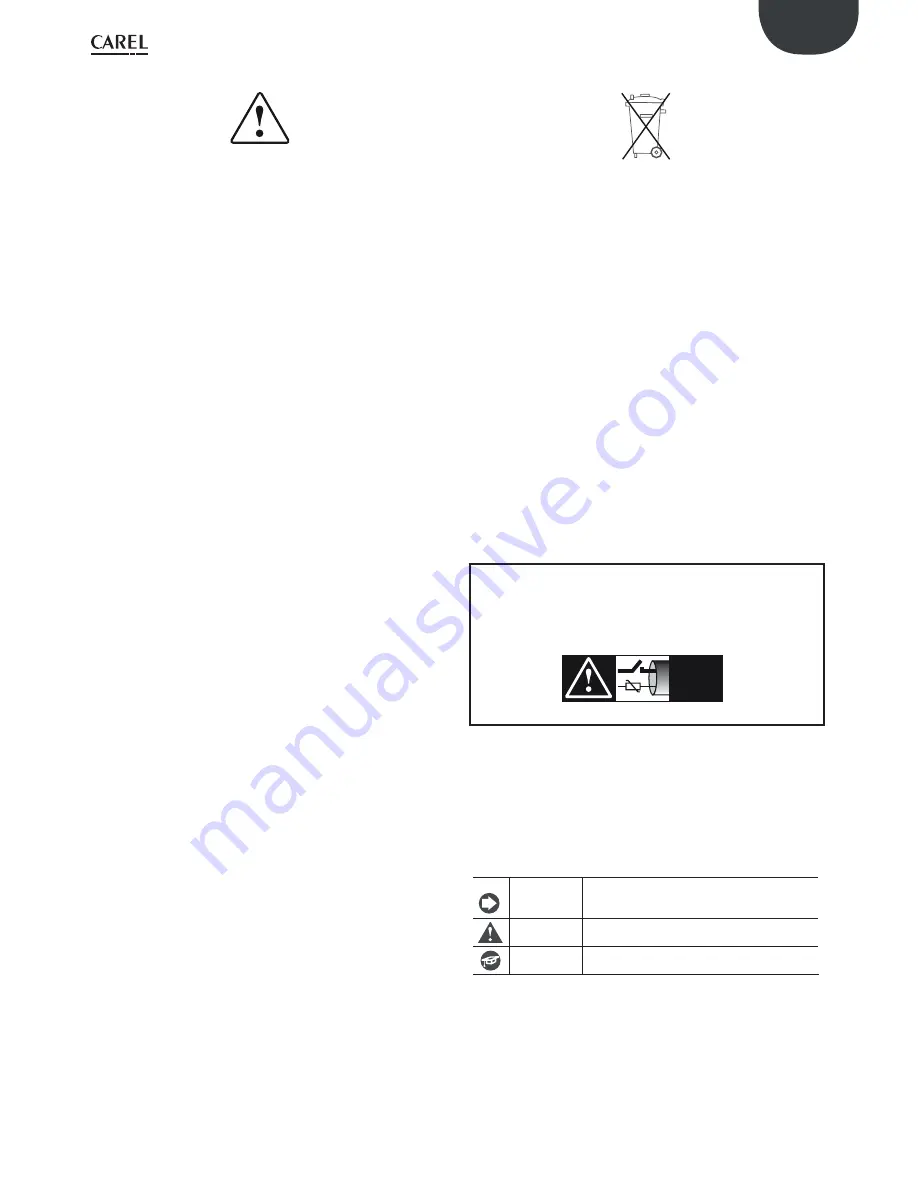
3
ENG
pRack +0300025EN rel. 1.3 - 17.12.2015
IMPORTANT
CAREL bases the development of its products on decades of experience in
HVAC, on the continuous investments in technological innovations to products,
procedures and strict quality processes with in-circuit and functional testing on
100% of its products, and on the most innovative production technology available
on the market. CAREL and its subsidiaries nonetheless cannot guarantee that all
the aspects of the product and the software included with the product respond
to the requirements of the fi nal application, despite the product being developed
according to start-of-the-art techniques.
The customer (manufacturer, developer or installer of the fi nal equipment) accepts
all liability and risk relating to the confi guration of the product in order to reach
the expected results in relation to the specifi c fi nal installation and/or equipment.
CAREL may, based on specifi c agreements, act as a consultant for the positive
commissioning of the fi nal unit/application, however in no case does it accept
liability for the correct operation of the fi nal equipment/system.
The CAREL product is a state-of-the-art product, whose operation is specifi ed in the
technical documentation supplied with the product or can be downloaded, even
prior to purchase, from the website www.CAREL.com.
Each CAREL product, in relation to its advanced level of technology, requires setup
/ confi guration / programming / commissioning to be able to operate in the best
possible way for the specifi c application. The failure to complete such operations,
which are required/indicated in the user manual, may cause the fi nal product to
malfunction; CAREL accepts no liability in such cases.
Only qualifi ed personnel may install or carry out technical service on the product.
The customer must only use the product in the manner described in the
documentation relating to the product.
In addition to observing any further warnings described in this manual, the
following warnings must be heeded for all CAREL products:
• Prevent the electronic circuits from getting wet. Rain, humidity and all types of
liquids or condensate contain corrosive minerals that may damage the electronic
circuits. In any case, the product should be used or stored in environments that
comply with the temperature and humidity limits specifi ed in the manual.
• Do not install the device in particularly hot environments. Too high temperatures
may reduce the life of electronic devices, damage them and deform or melt the
plastic parts. In any case, the product should be used or stored in environments
that comply with the temperature and humidity limits specifi ed in the manual.
• Do not attempt to open the device in any way other than described in the
manual.
• Do not drop, hit or shake the device, as the internal circuits and mechanisms
may be irreparably damaged.
• Do not use corrosive chemicals, solvents or aggressive detergents to clean the
device.
• Do not use the product for applications other than those specifi ed in the
technical manual.
All of the above suggestions likewise apply to the controllers, serial boards,
programming keys or any other accessory in the CAREL product portfolio.
CAREL adopts a policy of continual development. Consequently, CAREL reserves
the right to make changes and improvements to any product described in this
document without prior warning.
The technical specifi cations shown in the manual may be changed without prior
warning.
The liability of CAREL in relation to its products is specifi ed in the CAREL general
contract conditions, available on the website www.CAREL.com and/or by specifi c
agreements with customers; specifi cally, to the extent where allowed by applicable
legislation, in no case will CAREL, its employees or subsidiaries be liable for any
lost earnings or sales, losses of data and information, costs of replacement
goods or services, damage to things or people, downtime or any direct, indirect,
incidental, actual, punitive, exemplary, special or consequential damage of any
kind whatsoever, whether contractual, extra-contractual or due to negligence, or
any other liabilities deriving from the installation, use or impossibility to use the
product, even if CAREL or its subsidiaries are warned of the possibility of such
damage.
DISPOSAL
INFORMATION FOR USERS ON THE CORRECT HANDLING OF WASTE
ELECTRICAL AND ELECTRONIC EQUIPMENT (WEEE)
In reference to European Union directive 2002/96/EC issued on 27 January 2003
and the related national legislation, please note that:
1. WEEE cannot be disposed of as municipal waste and such waste must be
collected and disposed of separately;
2. the public or private waste collection systems defi ned by local legislation must
be used. In addition, the equipment can be returned to the distributor at the
end of its working life when buying new equipment;
3. the equipment may contain hazardous substances: the improper use or
incorrect disposal of such may have negative eff ects on human health and on
the environment;
4. the symbol (crossed-out wheeled bin) shown on the product or on the
packaging and on the instruction sheet indicates that the equipment has been
introduced onto the market after 13 August 2005 and that it must be disposed
of separately;
5. in the event of illegal disposal of electrical and electronic waste, the penalties
are specifi ed by local waste disposal legislation.
Warranty on the materials:
2 years (from the date of production, excluding
consumables).
Approval:
the quality and safety of CAREL INDUSTRIES Hqs products are
guaranteed by the ISO 9001 certifi ed design and production system.
WARNING:
separate as much as possible the probe and digital input signal
cables from the cables carrying inductive loads and power cables to avoid
possible electromagnetic disturbance.
Never run power cables (including the electrical panel wiring) and signal
cables in the same conduits.
NO POWER
& SIGNAL
CABLES
TOGETHER
READ CAREFULLY IN THE TEXT!
Key icone
NOTE:
to bring attention to a very important subject; in
particular, regarding the practical use of the various
functions of the product.
IMPORTANT:
to bring critical issues regarding the use of the
pRack pR300 to the attention of the user.
TUTORIAL:
some simple examples to accompany the user in
confi guring the most common settings.
Summary of Contents for PRK300D0E0
Page 2: ......
Page 4: ......
Page 6: ...6 ENG pRack 0300025EN rel 1 3 17 12 2015...