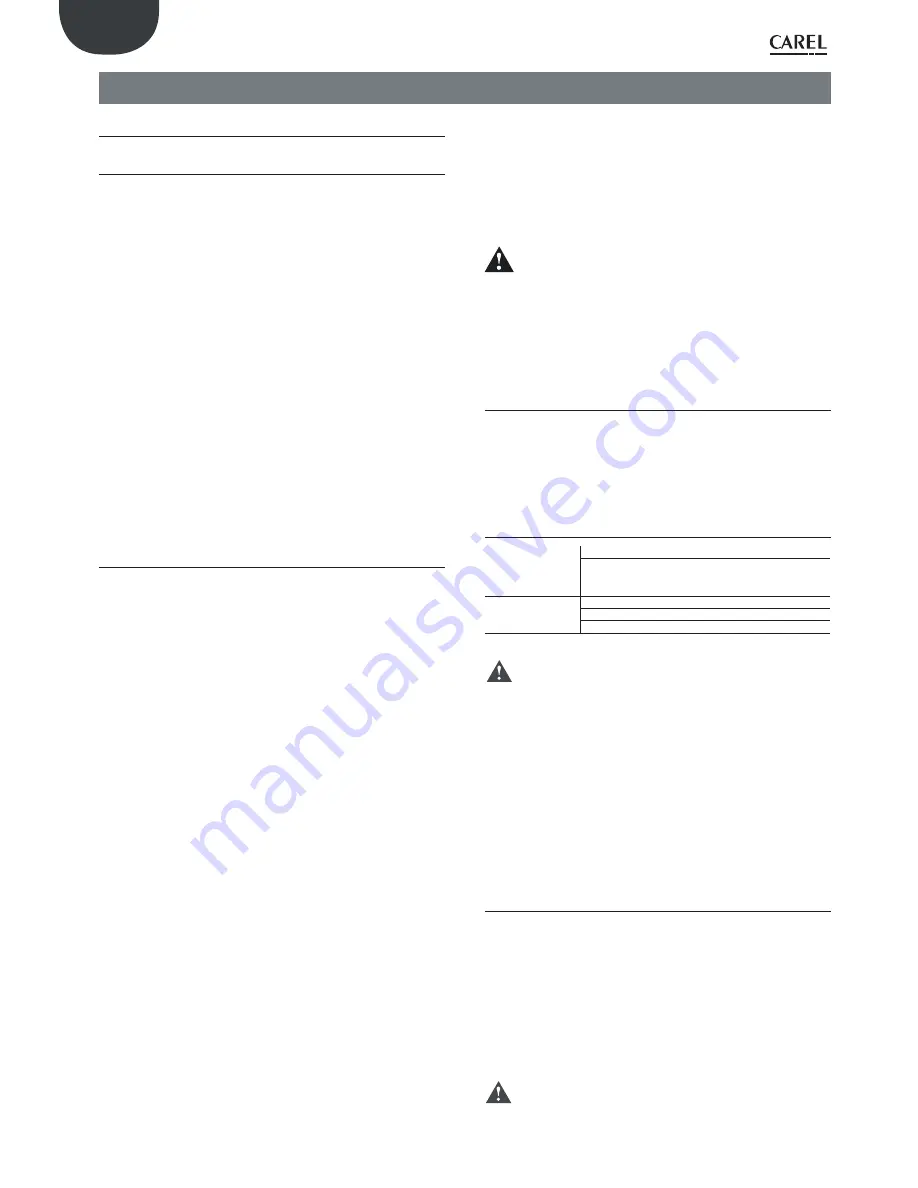
22
ENG
pRack +0300025EN rel. 1.3 - 17.12.2015
3.
INSTALLATION
3.1 General installation instructions
3.1.1 Installation
procedure
Environmental conditions
Avoid assembling the pRack pR300 and the terminal in environments with the
following characteristics:
•
temperature and humidity that do not conform to the rated operating
data of the product;
•
strong vibrations or knocks;
•
exposure to aggressive and polluting atmospheres(e.g.: sulphur and
ammonia fumes, saline mist, smoke) so as to avoid corrosion and/or
oxidation;
•
strong magnetic and/or radio frequency interference (therefore avoid
installing the units near transmitting antennae);
•
exposure of the pRack pR300 to direct sunlight and to the elements
in general;
•
large and rapid fl uctuations in the room temperature;
•
environments containing explosives or mixes of fl ammable gases;
•
exposure to dust (formation of corrosive patina with possible oxidation
and reduction of insulation).
Positioning the instrument inside the panel
The position of the instrument in the electrical cabinet must be chosen
so as to guarantee correct physical separation of the instrument from
the power components (solenoids, contactors, actuators, inverters, …)
and the connected cables. Proximity to such devices/cables may create
random malfunctions that are not immediately evident. The structure of
the panel must allow the correct fl ow of cooling air.
3.1.2 Wiring
procedure
When laying the wiring, “physically “ separate the power part from the control
part. The proximity of these two sets of wires will, in most cases, cause
problems of induced disturbance or, over time, malfunctions or damage
to the components. The ideal solution is to house these two circuits in two
separate cabinets. Sometimes this is not possible, and therefore the power
part and the control part must be installed inside the same panel. For the
control Signals, it is recommended to use shielded cables with twisted wires.
If the control cables have to cross over the power cables, the intersections
must be as near as possible to 90 degrees, always avoiding running the
control cables parallel to the power cables.
•
Use cable ends suitable for the corresponding terminals. Loosen
each screw and insert the cable ends, then tighten the screws. When
the operation is completed, slightly tug the cables to check they are
suffi
ciently tight;
•
separate as much as possible the sensor Signal, digital input and serial
line cables from the cables carrying inductive loads and power cables
to avoid possible electromagnetic disturbance. Never insert power
cables (including the electrical cables) and probe Signal cables in
the same conduits. Do not install the sensor cables in the immediate
vicinity of power devices (contactors, circuit breakers or similar);
•
reduce the path of the sensor cables as much as possible, and avoid
spiral paths that enclose power devices;
•
avoid touching or nearly touching the electronic components fi tted
on the boards to avoid electrostatic discharges (extremely damaging)
from the operator to the components;
•
if the power transformer secondary is earthed, check that the earth wire
corresponds to the wire that runs to the controller and enters terminal
G0; this applies to all the devices connected to the pRack pR300;
•
do not secure the cables to the terminals by pressing the screwdriver
with excessive force, to avoid damaging the pRack pR300;
•
for applications subject to considerable vibrations (1.5 mm pk-pk
10/55 Hz), secure the cables connected to the pRack pR300around 3
cm from the connectors using clamps;
•
if the product is installed in industrial environments (application of the EN
61000-6-2 standard) the length of the connections must be less than 30 m;
•
all the very low voltage connections (analogue and 24 Vac/Vdc digital
inputs, analogue outputs, serial bus connections, power supplies)
must have reinforced or double insulation from the mains network;
•
in residential environments, the connection cable between the pRack
pR300 and the terminal must be shielded;
•
there is no limit to the number of cables that can be connected to an
individual terminal. The only limitation concerns the maximum current
crossing each terminal: this must not exceed 8 A;
•
the maximum cross-section of the cable that connected to a terminal
is 2.5 mm
2
(12 AWG);
•
the maximum value of the twisting torque to tighten the screw on the
terminal (torque tightening) is 0.6 Nm;
Important:
•
Installation must be performed according to the standards and
legislation in force in the country where the device is used;
•
for safety reasons the equipment must be housed inside an electrical
panel, so that the only accessible part is the display and the keypad;
•
in the event of malfunctions, do not attempt to repair the device, but
rather contact the CAREL service centre;
•
the connector kit also contains the stick-on labels.
3.1.3
Anchoring the pRack pR300
The pRack pR300is installed on a DIN rail. To fasten the unit to the DIN rail,
press it lightly against the rail. The rear tabs will click into place, locking
the unit to the rail. Removing the unit is just as Simple, using a screwdriver
through the release slot to lever and lift the tabs. The tabs are kept in the
locked position by springs.
3.2 Power
supply
Power supply to the
pRack pR300 S, M;
L (controller with
terminal connected)
28…36 Vdc +10/-20% or24 Vac +10/-15% 50…60 Hz;
Maximum current P= 15 W (power supply Vdc). P=40 VA
(Vac)
Power supply to
the pRack pR300
Compact
DC power supply: 48 Vdc (36 Vmin…72 Vmax)
AC power supply: 24 Vac +10/-15 %, 50/60 Hz
Maximum current P=11W, P=14VA, Imax=700mA
Tab. 3.a
Important:
•
power supplies other than those specifi ed seriously damage the system;
•
in the installation, it is recommended to supply just one pRack pR300
controller using a class 2 safety transformer - 100 VA for the models
with built-in driver, and 50 VA for the pRack S, M, L models;
•
the power supply to the pRack pR300 controller and terminal (or
pRack pR300 controllers and terminals) should be separated from the
power supply to the other electrical devices (contactors and other
electromechanical components) inside the electrical panel;
•
if the power transformer secondary is earthed, check that the earth wire
corresponds to the wire that runs to the controller and enters terminal
G0. This applies to all the devices connected to the pRack pR300;
•
a yellow LED indicates that power is connected to the pRack pR300.
3.3 Universal
inputs/outputs
Universal inputs/outputs are distinguished by the letter U...
They can be confi gured from the application program for many diff erent
uses, such as the following:
•
passive temperature probes: NTC, PTC, PT100, PT500, PT1000;
•
active pressure/temperature/humidity probes;
•
ratiometric pressure probes;
•
current inputs, 0 to 20 mA or 4 to 20 mA;
•
voltage inputs, 0 to 1 Vdc or 0 to 10 Vdc;
•
voltage-free contact digital inputs and fast digital inputs;
•
analogue outputs, 0 to 10 Vdc;
•
PWM outputs.
Important:
•
the universal inputs/outputs cannot be used as digital outputs.
Summary of Contents for PRK300D0E0
Page 2: ......
Page 4: ......
Page 6: ...6 ENG pRack 0300025EN rel 1 3 17 12 2015...