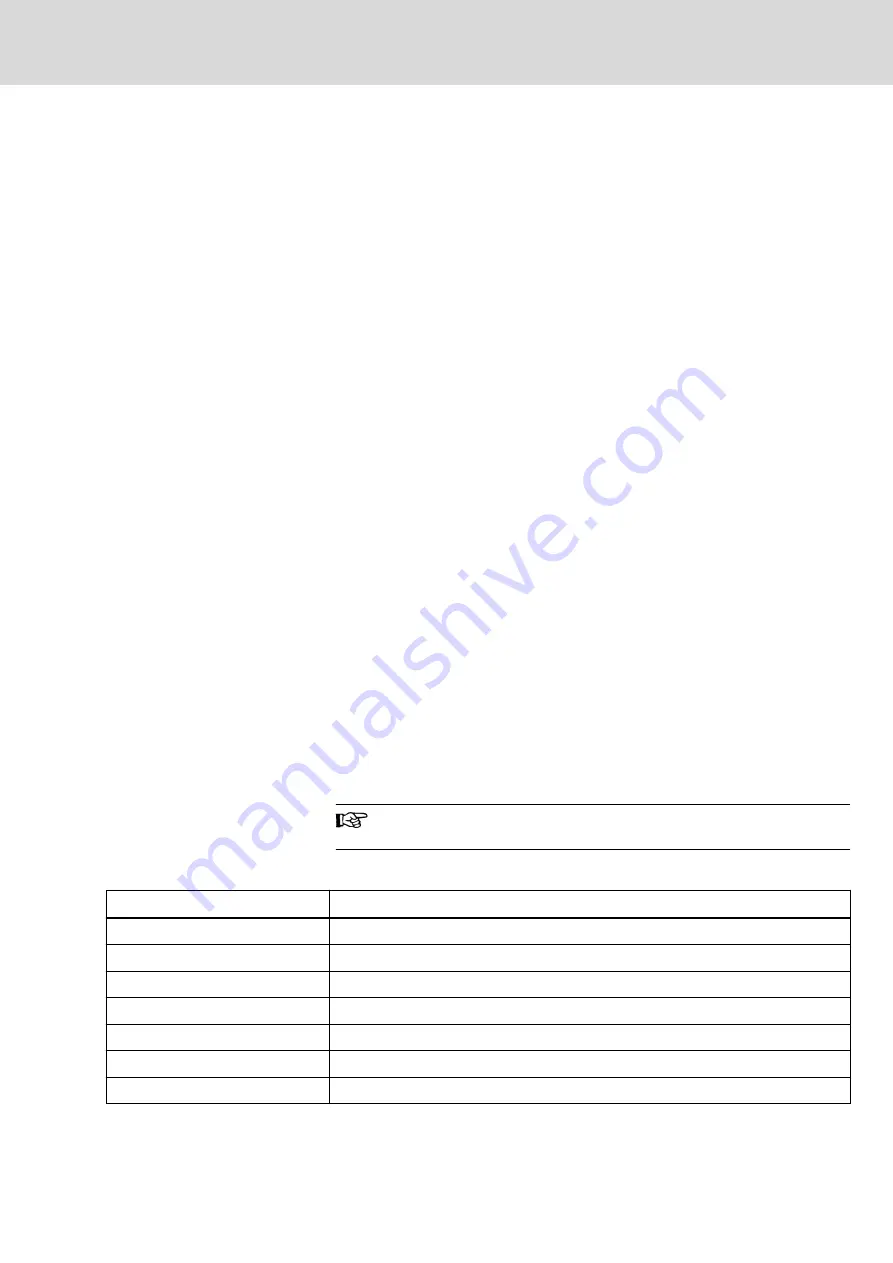
●
The affected task is immediately aborted.
●
All PLC variables in the affected task remain frozen to facilitate debug‐
ging.
●
Other tasks run to their end and are not called any more (like "PLC
STOP"). If a task does not reach its natural end in double its cycle time,
it is aborted.
●
When the PLC has control over the drive, the drive is switched off (inter‐
nal system control ON).
●
The error is also displayed on next login.
●
The PLC cannot be set to RUN any more -> an error is signaled on the
first attempt. The RUN state of the PLC then is only possible after a
warm restart of the PLC.
Troubleshooting compilation errors
The easiest way to troubleshoot compilation errors is with a connected (even
subsequently) programming system. Errors (as well as warnings and notifica‐
tions) are displayed in the "Messages" window with a short description. Dou‐
ble-clicking a message leads to the point in the source text which caused the
message.
Troubleshooting runtime errors
Runtime errors can be read in plain text in parameter "P-0-1365, PLC error
message".
If no programming system is available, the error can be located offline by
reading the text of "P-0-1365, PLC error message".
See also "
"
Errors detected by functions or function blocks
The individual function blocks have outputs which can be used for error han‐
dling:
●
"Error": An error bit (BOOL)
●
"ErrorID": An error number (ENUM type, few values)
●
"ErrorIdent": An error code with extended error information
"Error"
The "Error" output is BOOL type. The rising edge of "Error" signals that an
error has occurred while processing the function block.
"ErrorID"
The "ErrorID" output is ERROR_CODE type. When an error has occurred at
the function block, the error classification can be seen at the "ErrorID" output.
The ERROR_CODE type is defined in the "CommonTypes" li‐
brary of each device.
The table below shows the possible error codes (ErrorID) and their causes:
ErrorID
Cause of error
NONE
No error
INPUT_INVALID
Value outside of programmable range of values, e.g., axis number 30000
INPUT_RANGE
Value outside of currently possible range of values, e.g., axis 5 not configured
RESOURCE
Function not enabled, "MoveRelative" with "Open Loop" or hardware not found
CALCULATION
Calculation error, e.g., overflow in PID controller
COMMUNICATION
Communication error, e.g., failure in communication to external devices
STATE_MACHINE
Current state of state machine prevents or prohibits further processing
DOK-INDRV*-MLD3-**VRS*-AP02-EN-P
Bosch Rexroth AG
73/267
Rexroth IndraDrive Rexroth IndraMotion MLD (2G) as of MPx-18
Basic functions of Rexroth IndraMotion MLD
LSA Control S.L. www.lsa-control.com [email protected] (+34) 960 62 43 01