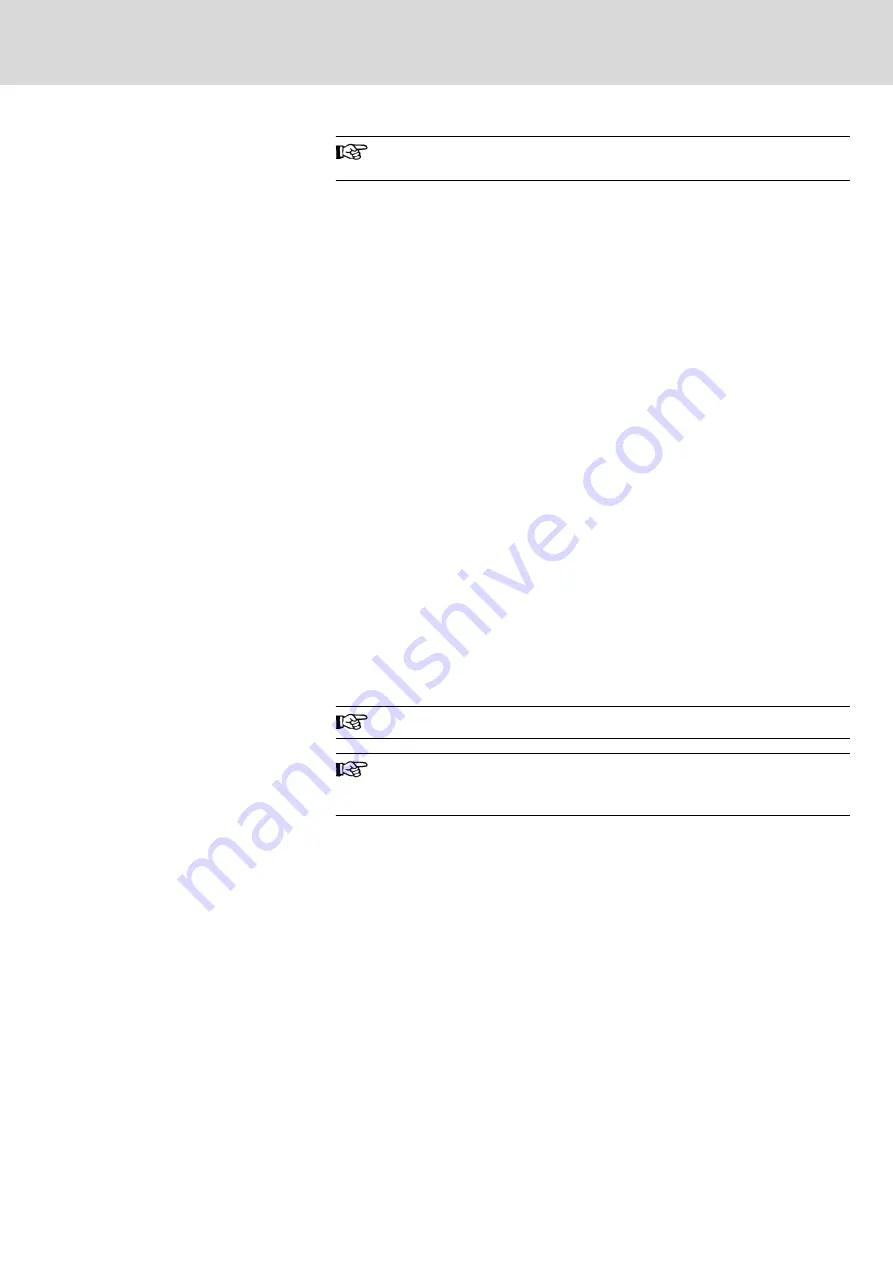
CCD in MLD-M system mode currently supports CCD cycle times
of 1 ms, 2 ms and 4 ms.
Application
The time a periodic PLC task (motion task) is called in the CCD master axis
should be linked to the CCD cycle (MS channel). This is why the MLD-M sys‐
tem mode and "permanent MLD control" have to be activated in the CCD
master axis.
The motion task in synchronism with CCD is only used in conjunction with the
MLD-M system mode. In MLD-M system mode, the MLD-M of the CCD mas‐
ter axis controls the master axis (local slave) itself, as well as the remote ax‐
es. This often requires processing actual values of all axes latched at the
same time, as well as writing command values that take effect in all axes at
the same time. This consistent data exchange is achieved with the motion
task in synchronism with CCD in conjunction with the "AxisData" structure.
Example
A milling head is to be moved in three dimensions with MLD-M. To achieve
proper milling results, the control unit (MLD-M) has to know the actual posi‐
tion values of all axes involved in the motion relative to the same time (T4) so
that it can calculate the corresponding command values. These calculated
command values have to be transmitted to all axes at the same time so they
take effect at the same time. A task synchronized with the CCD clock is re‐
quired to ensure this occurs. The real-time data are exchanged via the "Axis‐
Data" structure.
Timing
With MLD, the motion task in synchronism with CCD runs between CCD AT
processing and CCD MDT processing.
The real-time data of the "AxisData" structure are updated before the start of
the task and after the end of the task. The actual values are read after CCD
AT processing and the command values are written before CCD MDT pro‐
cessing. This way consistent data can always be accessed or written using
the "AxisData" structure within the motion task in synchronism with CCD. The
values written via the axis data structure take effect in the axes at the same
time.
Only one "external event" motion task can be used at a time.
Both types of motion tasks are always running. However, they are
only synchronized once cyclic data are exchanged via the master
communication or via CCD.
Diagnostics and error messages in
relation to a motion task
●
PLC errors
If the boot project was loaded incorrectly, this is signaled in P-0-1365
and IndraWorks ("Log" tab page of the device editor).
●
Drive error: F6010 PLC runtime error
Error F6010 is triggered, e.g., if an error occurs while the boot project is
loading. Possible errors in conjunction with a motion task are the PLC
errors (see "F6010" in the Reference Book for diagnostic messages)
mentioned above.
●
Transition command errors
–
C0241 Incorrect motion task parameterization
–
C0266 Incorrect CCD phase switch
Please refer to the Reference Book for diagnostic messages for
possible causes and remedies for the C0266 transition command
error.
DOK-INDRV*-MLD3-**VRS*-AP02-EN-P
Bosch Rexroth AG
63/267
Rexroth IndraDrive Rexroth IndraMotion MLD (2G) as of MPx-18
Basic functions of Rexroth IndraMotion MLD
LSA Control S.L. www.lsa-control.com [email protected] (+34) 960 62 43 01