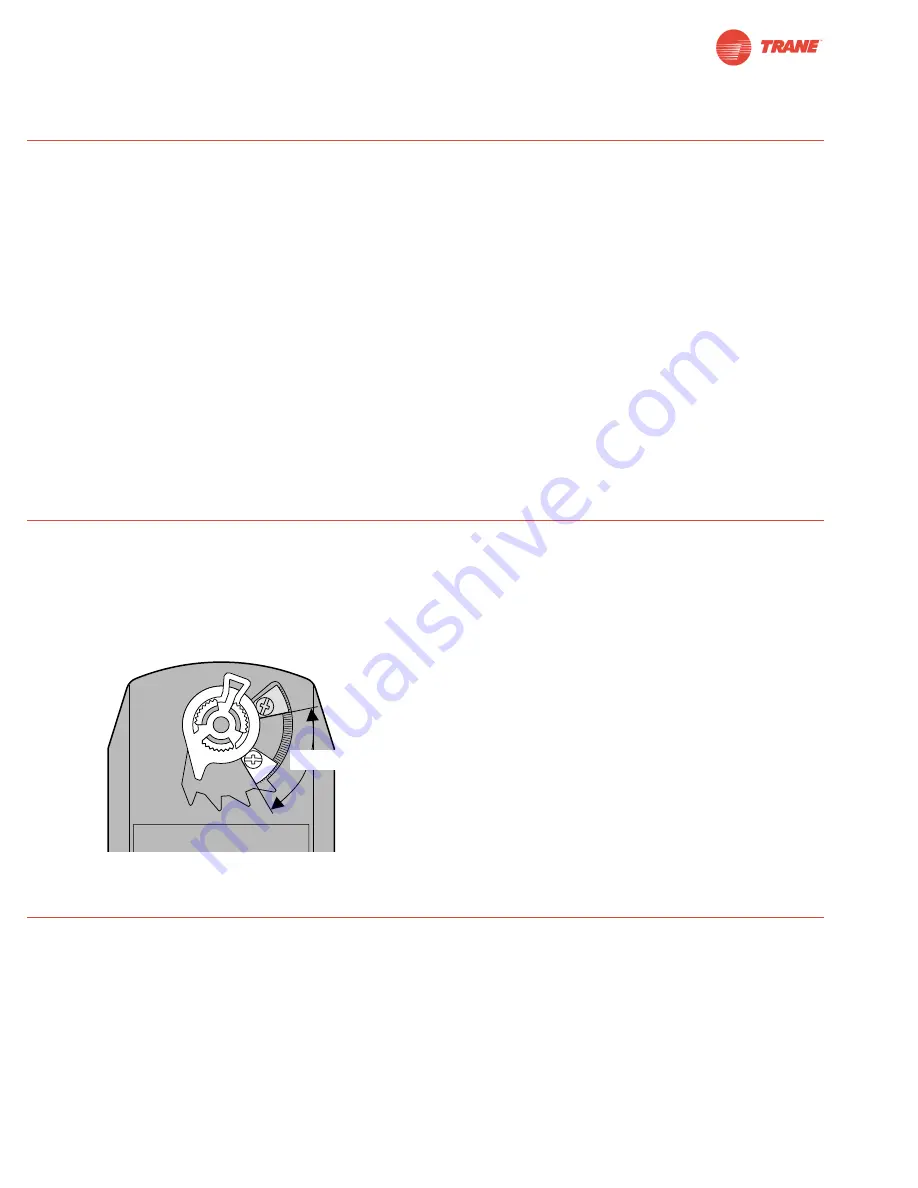
68
I20683 - Subject to change.
The TTF actuators are provided with an adjustable stop to
limit the rotation of the actuator. This function works in
conjunction with the universal clamp or the optional position
indicator. The adjustable stop is needed when rotation of less
than 95° is required. The TTF actuator can be indefinitely
stalled, in any position, without harming the actuator.
Using the Universal Clamp:
1. Loosen the end stop fastening screw using a #2 Phillips
screwdriver.
2. Move the stop block so the bottom edge of the block lines
up with the number corresponding to the desired degrees
of rotation (example: 45 degrees of rotation = .5).
3. Lock the block in place with the fastening screw.
4. Check the actuator for proper rotation.
Using the IND-TF Position Indicator with Adjustable Stop:
Note: preferred method if short shaft mounting is used.
1. With the actuator in its fail-safe position, place the IND-TF
Position Indicator so that it points to the 0 degree position.
2. Loosen the end stop fastening screw using a #2 Phillips
screwdriver.
3. Move the stop block so the bottom edge of the block lines
up with the number corresponding to the desired degrees
of rotation (example: 45 degrees of rotation = .5).
4. Lock the block in place with the fastening screw.
5. Check the actuator for proper rotation.
37...100%
Mechanical Angle of Rotation Limiting
Installation Instructions
Quick-Mount Visual Instructions for Mechanical Installation
TTF24-3 and TTF24-SR actuators have a direction of rotation
switch on the cover labeled “CW-CCW”. Switch position indicates
start point. For the TTF24-SR, with the switch in position “CW”, the
actuator rotates clockwise with a decrease in voltage or current.
With the switch in position “CCW”, the actuator rotates counter-
clockwise with a decrease in voltage or current.
The TTF24-3 and TTF24-SR actuators rotate clockwise when the
switch is in the “CW” position and power is applied to wire #3.
When power is applied to wire #4 the actuator rotates counter
clockwise.
Rotating the direction of rotation switch to “CCW” reverses the
control logic.
During checkout, the switch position can be temporarily
reversed and the actuator will reverse its direction. This allows
the technician a fast and easy way to check the actuator oper-
ation without having to switch wires or change settings on the
controller.
When the check-out is complete, make sure the
switch is placed back to its original position.
Direction of Rotation Switch
Initialization of the TTF24-SR
When power is applied, the internal microprocessor recognizes
that the actuator is at its full fail-safe position and uses this
position as the base for all of its position calculations. This
procedure takes approximately 15 seconds. During this time
you will see no response at the actuator. The microprocessor
will retain the initialized zero during short power failures of up
to 25 seconds. When power is applied during this period, the
actuator will return to normal operation and proceed to the
position corresponding to the input signal provided. For power
failures over 25 seconds, the actuator will be at its fail-safe
position and will go through the start up initialization again.
Motor Position Detection (TTF24-SR)
Brushless DC motors eliminate the need for potentiometers for
positioning. Inside the motor are three “Hall Effect” sensors.
These sensors detect the spinning rotor and send pulses to the
microprocessor which counts the pulses and calculates the
position to within 1/3 of a revolution of the motor.
Overload Protection
The TTF, on-off actuators are electronically protected against
overload. The TTF, on-off actuator have an internal current
limiter which maintains the current at a safe level which will not
damage the actuator while providing adequate holding torque.
The TTF24, modulating, actuators (TTF24-SR, TTF24-3) are
protected against overload by digital technology located in the
ASIC. The ASIC circuitry constantly monitors the rotation of the
brushless DC motor inside the actuator and stops the pulsing to
the motor when it senses a stall condition. The motor remains
energized and produces full rated torque during stall conditions.
The actuator will try to move in the direction of the stall every 2
minutes, for a period of 32 minutes. After this, the actuator will
try again every 2 hours.
Operational Information for TTF Actuators
Summary of Contents for TRANE TAF Series
Page 7: ...Notes Work Pad 7 I20683 Subject to change...
Page 27: ...27 I20683 Subject to change TAF Notes Work Pad...
Page 57: ...57 I20683 Subject to change TLF Notes Work Pad...
Page 73: ...73 I20683 Subject to change TTF Notes Work Pad...
Page 98: ...98 I20683 Subject to change Notes Work Pad...
Page 165: ...165 I20683 Subject to change Wiring Guide Notes Work Pad...
Page 166: ...Notes Work Pad 166 I20683 Subject to change...