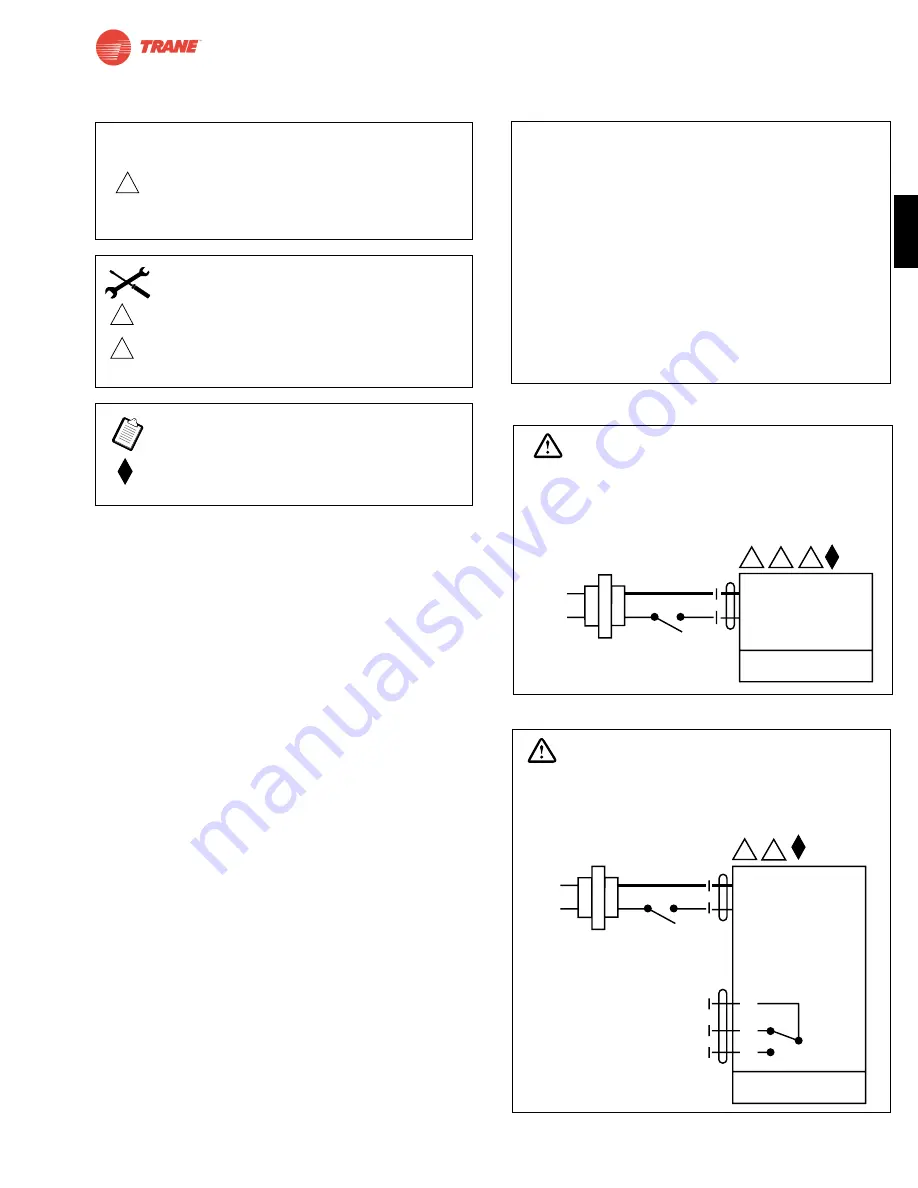
31
I20683 - Subject to change.
TNF
TNF24 (-S)
On-off, Spring Return Fail-Safe, 24 V
Wiring Diagrams
TNF24 Typical Specification
On-off spring return damper actuators shall be direct
coupled type which require no crankarm and linkage and
be capable of direct mounting to a jackshaft up to a 1.05”
diameter. The actuators must be designed so that they may
be used for either clockwise or counterclockwise fail-safe
operation. Actuators shall be protected from overload at all
angles of rotation. If required, one SPDT auxiliary switch
shall be provided having the capability of being adjustable.
Actuators with auxiliary switches must be constructed to
meet the requirements for Double Insulation so an electrical
ground is not required to meet agency listings. Actuators are
UL listed and CSA certified and be manufactured under ISO
9001 International Quality Control Standards. Actuators
shall be as manufactured by Belimo.
1 Common
2 + Hot
2
24 VAC Transformer
TNF24
Line
Volts
3
5
WARNING
Live Electrical Components!
During installation, testing, servicing and troubleshooting of this product, it maybe
necessary to work with live electrical components. Have a qualified licensed electrician
or other individual who has been properly trained in handling live electrical components
perform these tasks. Failure to follow all electrical safety precautions when exposed
to live electrical components could result in death or serious injury.
1 Common
2 + Hot
2
24 VAC Transformer
TNF24-S
Line
Volts
3
S1
S2
S3
NC
NO
5° to 85°
WARNING
Live Electrical Components!
During installation, testing, servicing and troubleshooting of this product, it maybe
necessary to work with live electrical components. Have a qualified licensed electrician
or other individual who has been properly trained in handling live electrical components
perform these tasks. Failure to follow all electrical safety precautions when exposed
to live electrical components could result in death or serious injury.
On-off wiring for TNF24
On-off wiring for TNF24-S
W454
W455
INSTALLATION NOTES
3
5
Actuator may also be powered by 24 VDC.
Actuators with plenum rated cable do not have
numbers on wires; use color codes instead.
Actuators with appliance cables use numbers.
APPLICATION NOTES
Meets cULus or UL and CSA requirements without
the need of an electrical ground connection.
CAUTION
2
Equipment damage!
Actuators may be connected in parallel. Power con-
sumption and input impedance must be observed.
Summary of Contents for TRANE TAF Series
Page 7: ...Notes Work Pad 7 I20683 Subject to change...
Page 27: ...27 I20683 Subject to change TAF Notes Work Pad...
Page 57: ...57 I20683 Subject to change TLF Notes Work Pad...
Page 73: ...73 I20683 Subject to change TTF Notes Work Pad...
Page 98: ...98 I20683 Subject to change Notes Work Pad...
Page 165: ...165 I20683 Subject to change Wiring Guide Notes Work Pad...
Page 166: ...Notes Work Pad 166 I20683 Subject to change...