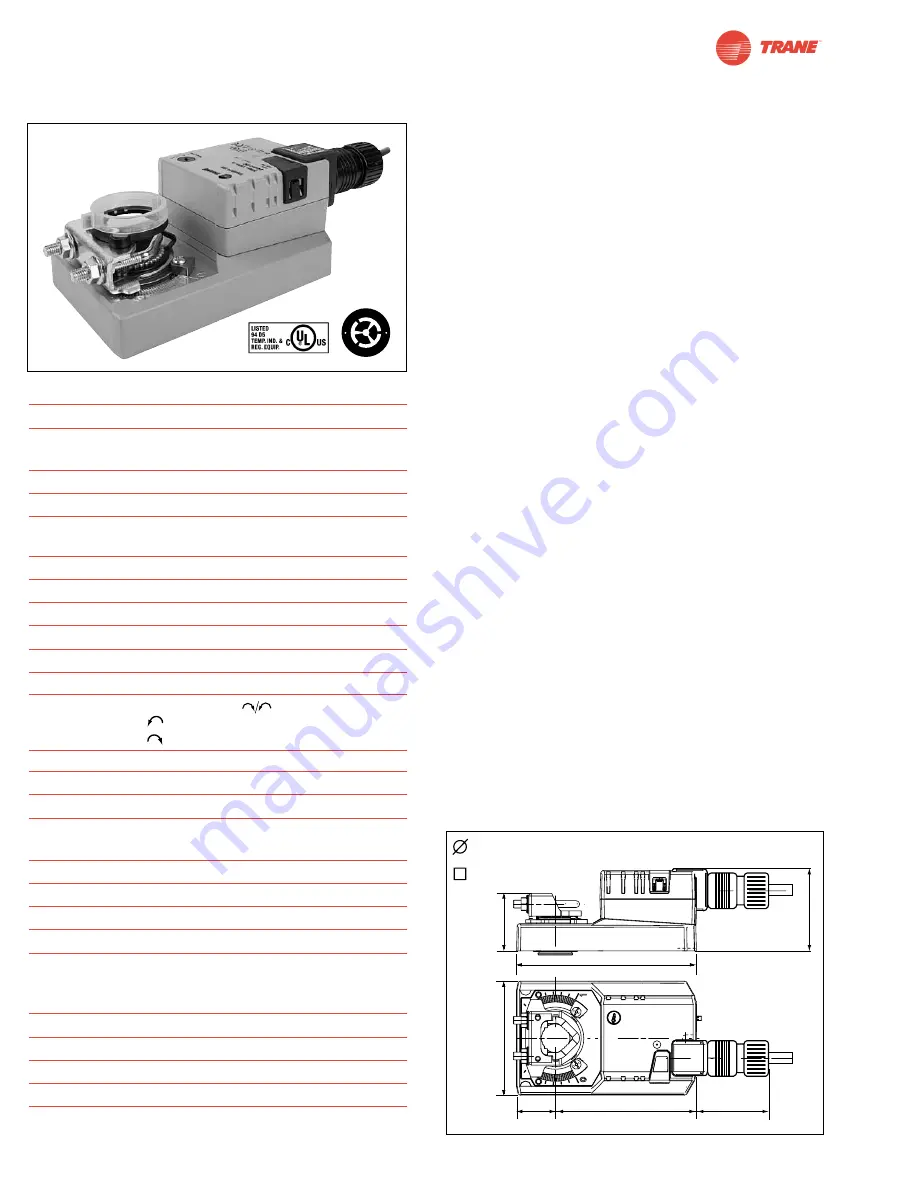
84
I20683 - Subject to change.
TAMB24-SR
Proportional Control, Non-Spring Return, Direct Coupled, 24V, for 2 to 10 VDC and 4 to 20 mA
Technical Data
TAMB24-SR
Power Supply
24 VAC ± 20% 50/60 Hz
24 VDC ± 10%
Power Consumption
2.5 W (0.4 W)
Transformer Sizing
5 VA (Class 2 power source)
Electrical Connection
3 ft, 18 GA plenum rated cable
1/2” conduit connector
Overload Protection
electronic throughout 0° to 95° rotation
Operating Range Y
2 to 10 VDC, 4 to 20 mA
Input Impedance
100k
Ω
(0.1 mA), 500
Ω
Feedback Output U
2 to 10 VDC (max 0.5 mA)
Angle of Rotation
max. 95°, adjust. with mechanical stop
Torque
180 in-lb [20 Nm]
Direction of Rotation
reversible with switch. Actuator will move:
=
CCW with decreasing control signal (10
➞
2V)
=
CW with decreasing control signal (10
➞
2V)
Position Indication
reflective visual indicator (snap-on)
Manual Override
external push button
Running Time
95 seconds, constant independent of load
Humidity
5 to 95% RH non condensing
(EN 60730-1)
Ambient Temperature -22°F to +122°F [-30°C to +50°C]
Storage Temperature -40°F to +176°F [-40°C to +80°C]
Housing
NEMA 2/IP54
Housing Material
UL94-5VA
Agency Listings
cULus acc. to UL 60730-1/-2-14 and
CAN/CSA C22.2 No.24, CE according
to 73 / 23 / EEC
Noise Level
<45dB(A)
Servicing
maintenance free
Quality Standard
ISO 9001
Weight
2.2 lbs [1000 Kg]
Torque min. 180 in-lb for control of damper
surfaces up to 45 sq ft.
Application
For proportional modulation of dampers in HVAC systems.
Actuator sizing should be done in accordance with the
damper manufacturer’s specifications.
The actuator is mounted directly to a damper shaft up to 1.05”
in diameter by means of its universal clamp, 1/2” self-centered
default. A crankarm and several mounting brackets are
available for applications where the actuator cannot be direct
coupled to the damper shaft.
The actuator operates in response to a 2 to 10 VDC, or with
the addition of a 500
Ω
resistor, a 4 to 20 mA control input
from an electronic controller or positioner. A 2 to 10 VDC
feedback signal is provided for position indication or
master-slave applications.
Operation
The actuator is not provided with and does not require any
limit switches, but is electronically protected against overload.
The anti-rotation strap supplied with the actuator will prevent
lateral movement.
The TAMB series provides 95° of rotation and a visual indicator
indicates position of the actuator. When reaching the damper or
actuator end position, the actuator automatically stops. The gears
can be manually disengaged with a button on the actuator cover.
The TAMB24-SR… actuators use a sensorless brushless DC
motor, which is controlled by an Application Specific
Integrated Circuit (ASIC). The ASIC monitors and controls the
actuator’s rotation and provides a digital rotation sensing
(DRS) function to prevent damage to the actuator in a stall
condition. Power consumption is reduced in holding mode.
Add on auxiliary switches or feedback potentiometers are
easily fastened directly onto the actuator body for signaling
and switching functions
For all accessories, see pages 110 and 132.
Dimensions
(All numbers in brackets are in millimeters.)
5.47” [139]
2.2
”
[56]
2.49
”
[63.4]
4.3” [109]
1.18”
[30]
3.46
”
[88]
1/2” to 1.05” [13 to 26]
1/2” Centered (Default)
3/8” to 11/16” [10 to 17]
2” [50.8]
D122
©
H
A
LOM
O
B
r
u
s
hle
s s D C
M
o
to
r
Summary of Contents for TRANE TAF Series
Page 7: ...Notes Work Pad 7 I20683 Subject to change...
Page 27: ...27 I20683 Subject to change TAF Notes Work Pad...
Page 57: ...57 I20683 Subject to change TLF Notes Work Pad...
Page 73: ...73 I20683 Subject to change TTF Notes Work Pad...
Page 98: ...98 I20683 Subject to change Notes Work Pad...
Page 165: ...165 I20683 Subject to change Wiring Guide Notes Work Pad...
Page 166: ...Notes Work Pad 166 I20683 Subject to change...