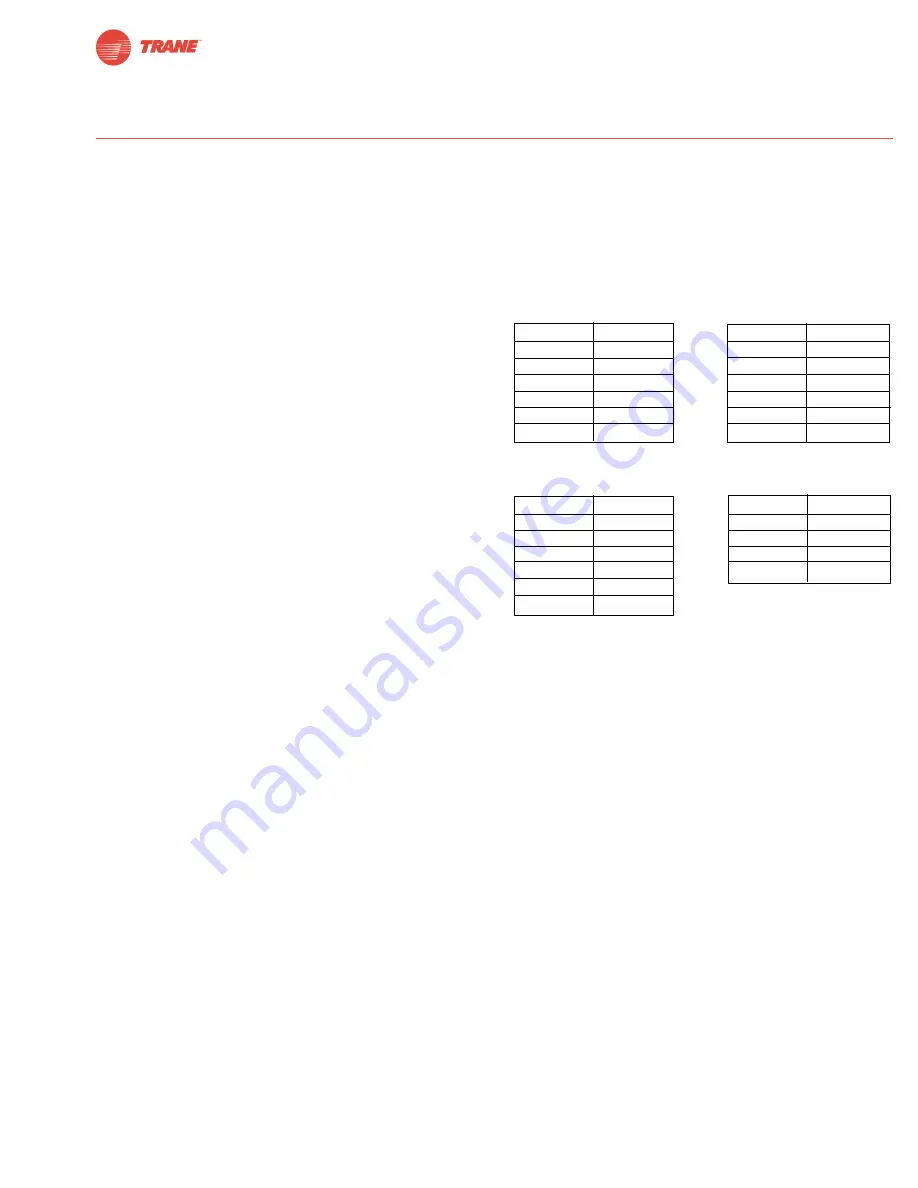
105
I20683 - Subject to change.
Operation
Wiring
General Wiring Instructions
WARNING The wiring technician must be trained and
experienced with electronic circuits. Disconnect power supply
before attempting any wiring connections or changes. Make
all connections in accordance with wiring diagrams and follow
all applicable local and national codes. Provide disconnect
and overload protection as required. Use copper, twisted pair,
conductors only. If using electrical conduit, the attachment to
the actuator must be made with flexible conduit.
Always read the controller manufacturer's installation
literature carefully before making any connections. Follow
all instructions in this literature. If you have any questions,
contact the controller manufacturer.
Transformer(s)
The non-spring return actuators require a 24 VAC class 2
transformer and draws a maximum of 5 VA per actuator. The
actuator enclosure cannot be opened in the field, there are no
parts or components to be replaced or repaired.
– EMC directive: 89/336/EEC
– Software class A: Mode of operation type 1
– Low voltage directive: 73/23/EEC
CAUTION: It is good practice to power electronic or digital
controllers from a separate power transformer than that used
for actuators or other end devices. The power supply design
in our actuators and other end devices use half wave
rectification. Some controllers use full wave rectification.
When these two different types of power supplies are
connected to the same power transformer and the DC
commons are connected together, a short circuit is created
across one of the diodes in the full wave power supply,
damaging the controller. Only use a single power transformer
to power the controller and actuator if you know the controller
power supply uses half wave rectification.
Multiple Actuators, One Transformer
Multiple actuators may be powered from one transformer
provided the following rules are followed:
1. The TOTAL current draw of the actuators (VA rating) is
less than or equal to the rating of the transformer.
2. Polarity on the secondary of the transformer is strictly
followed. This means that all No. 1 wires from all
actuators are connected to the common leg on the trans-
former and all No. 2 wires from all actuators are
connected to the hotleg.
Mixing wire No. 1 & 2 on one leg
of the transformer will result in erratic operation or failure
of the actuator and/or controls.
Multiple Actuators, Multiple Transformers
Multiple actuators positioned by the same control signal may
be powered from multiple transformers provided the following
rules are followed:
1. The transformers are properly sized.
2. All No. 1 wires from all actuators are tied together and tied
to the negative leg of the control signal. See wiring diagram.
Wire Length for Actuators
Keep power wire runs below the lengths listed in the Figure H.
If more than one actuator is powered from the same wire run,
divide the allowable wire length by the number of actuators to
determine the maximum run to any single actuator.
Example: 3 actuators, 16 Ga wire
350 ft ÷ 3 actuators = 117 ft. maximum wire run
Maximum Wire Length:
TGMB-24…
Wire Size
Max. Feet.
Wire Size
Max. Feet
12 Ga
1125 ft.
12 Ga
1150 ft.
14 Ga
800 ft.
12 Ga
925 ft.
16 Ga
500 ft.
16 Ga
550 ft.
18 Ga
325 ft.
18 Ga
375 ft.
20 Ga
175 ft.
20 Ga
200 ft.
22 Ga
90 ft.
22 Ga
100 ft.
TNMB-24…
Wire Size
Max. Feet.
Wire Size
Max. Feet
12 Ga
1250 ft.
16 Ga
1125 ft.
14 Ga
1130 ft.
18 Ga
750 ft.
16 Ga
900 ft.
20 Ga
400 ft.
18 Ga
575 ft.
22 Ga
200 ft.
20 Ga
300 ft.
22 Ga
150 ft.
Figure H
Wire Type and Wire Installation Tips
For most installations, 18 or 16 Ga. cable works well with the
non-spring return actuators. Use code-approved wire nuts,
terminal strips or solderless connectors where wires are joined.
It is good practice to run control wires unspliced from the
actuator to the controller. If splices are unavoidable, make sure
the splice can be reached for possible maintenance. Tape
and/or wire-tie the splice to reduce the possibility of the splice
being inadvertently pulled apart.
The non-spring return proportional actuators have a digital
circuit that is designed to ignore most unwanted input signals
(pickup). In some situations the pickup may be severe enough
to cause erratic running of the actuator. For example, a large
inductive load (high voltage AC wires, motors, etc.) running
near the power or control wiring may cause excessive pickup.
To solve this problem, make one or more of the following
changes:
1. Run the wire in metallic conduit.
2. Re-route the wiring away from the source of pickup.
3. Use shielded wire (Belden 8760 or equal).
Ground the
shield to an earth ground. Do not connect it to the
actuator common.
TLMB-24…
TAMB-24…
Summary of Contents for TRANE TAF Series
Page 7: ...Notes Work Pad 7 I20683 Subject to change...
Page 27: ...27 I20683 Subject to change TAF Notes Work Pad...
Page 57: ...57 I20683 Subject to change TLF Notes Work Pad...
Page 73: ...73 I20683 Subject to change TTF Notes Work Pad...
Page 98: ...98 I20683 Subject to change Notes Work Pad...
Page 165: ...165 I20683 Subject to change Wiring Guide Notes Work Pad...
Page 166: ...Notes Work Pad 166 I20683 Subject to change...