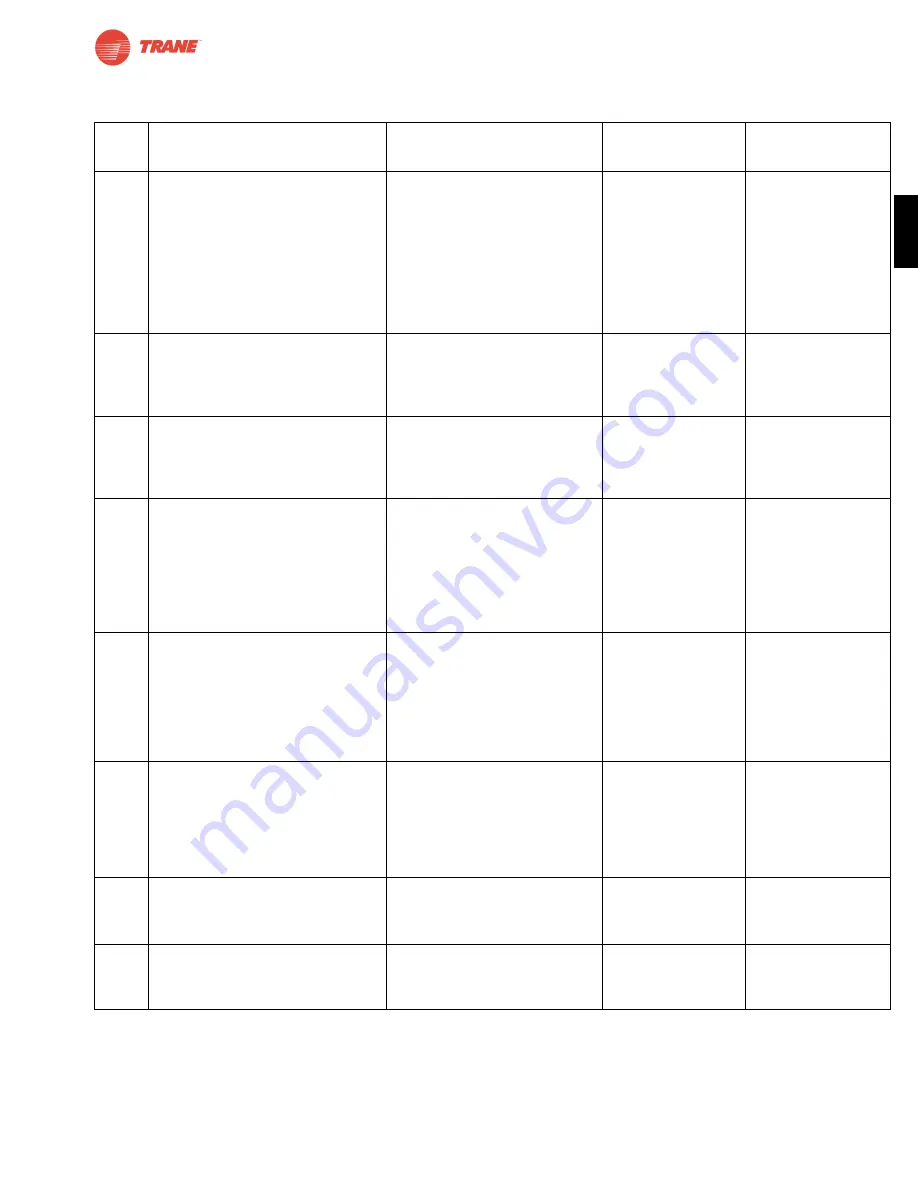
41
I20683 - Subject to change.
TNF
Startup and Checkout
Instructions For TNF24-SR + P-100…
Procedure
Control signal is applied to actuator.
Check power wiring. Correct any
problems. See Note 1.
Turn reversing switch to the correct
position. Make sure the switch is
turned all the way left or right.
Make sure the control signal positive
(+) is connected to Wire No 3 and
control signal negative (-) is connect-
ed to wire No. 1. Most control prob-
lems are caused by reversing these
two wires. Verify that the reversing
switch is all the way CCW or CW.
Check input signal with a digital volt
meter (DVM). Make sure the input is
within the range of the actuator. For
TNF24-SR this is 2 to 10 VDC or
4 to 20 mA. Note: The input signal
must be above the 2 VDC or 4 mA to
have the actuator move.
Loosen the nuts on the V-bolt and
move the damper by hand from fully
closed to fully open.
Check damper torque requirement.
Actuator works properly. Test
controller by following controller
manufacturer's instructions.
Expected Response
Actuator will move to its “Control
Signal” position.
Power supply rating should be
≥
the total power requirement of
the actuator(s). Minimum volt-
age of 19.2 VAC or 21.6 VDC.
Actuator will move to its “Control
Signal” position.
Drives to “Control Signal”
position.
Input voltage or current should
be ±1% of what controller's
adjustment or programming
indicate.
Damper will go from fully closed
to fully open.
Torque requirement is
≤
actuator’s minimum torque.
Gives Expected
Response
Go To Step…
Actuator operates
properly.
Step 8
Power wiring correct-
ed, actuator begins
to drive.
Step 1
Actuator operates
properly.
Step 8
Actuator operates
properly.
Step 8
Controller output
(actuator input) is
correct. Input
Polarity Correct.
Step 6
Damper moves
properly.
Step 7
Defective Actuator.
Replace Actuator.
Does Not Give
Expected Response
Go To Step…
No response at all.
Step 2
Operation is
reversed.
Step 3
Does not drive
toward "Control
Signal Position" .
Step 4
Power wiring
corrected, actuator
still does not drive.
Step 4
Does not drive
toward “Control
Signal Position”.
Step 4
Step 5
Reprogram, adjust
repair or replace
controller as needed.
Step 1
Find cause of damper
jam and repair. Move
damper back to the
fully closed position
and tighten the nuts.
Step 1
Recalculate actuator
requirement and
correct installation.
Step
1.
2.
3.
4.
5.
6.
7.
8.
Note 1
Check that the transformer(s) are sized properly.
• If a common transformer is used, make sure that polarity is observed on the secondary. This means connect all No. 1
wires to one leg of the transformer and all No. 2 wires to the other leg of the transformer.
• If multiple transformers are used with one control signal, make sure all No. 1 wires are tied together and tied to control
signal negative (-).
• Controllers and actuators must have separate 24 VAC/VDC power sources.
TNF24-SR + P-100… Electrical Check-out Procedure
Summary of Contents for TRANE TAF Series
Page 7: ...Notes Work Pad 7 I20683 Subject to change...
Page 27: ...27 I20683 Subject to change TAF Notes Work Pad...
Page 57: ...57 I20683 Subject to change TLF Notes Work Pad...
Page 73: ...73 I20683 Subject to change TTF Notes Work Pad...
Page 98: ...98 I20683 Subject to change Notes Work Pad...
Page 165: ...165 I20683 Subject to change Wiring Guide Notes Work Pad...
Page 166: ...Notes Work Pad 166 I20683 Subject to change...