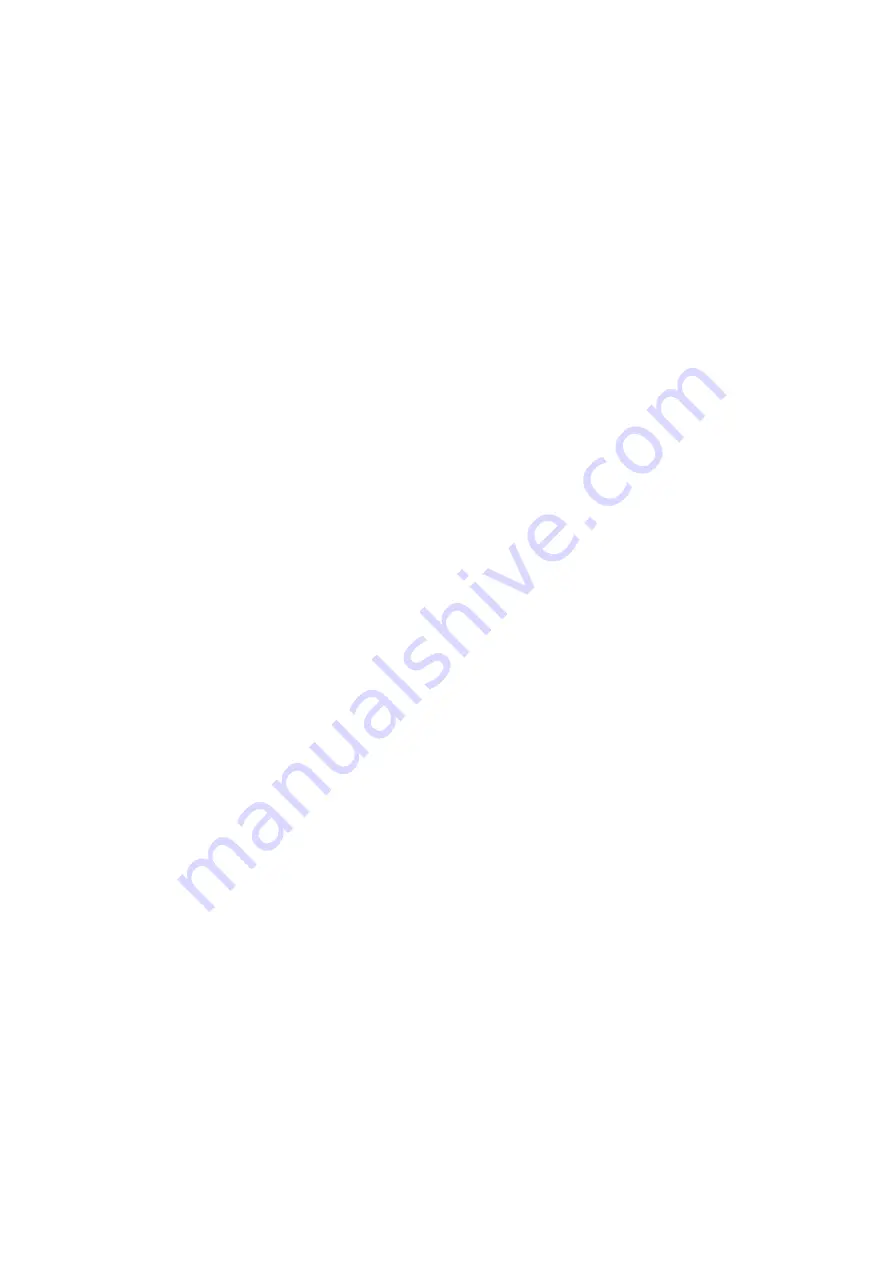
2022.3-0000010 OM
69
Cylinder heads 18 (figure 3.1.1) (one head for three cylinders) are interchangeable.
There are inlet and outlet passages in inner cavities of cylinder heads which are covered
with valves 3 (figure 3.1.2). To provide heat output, cylinder heads have inner cavities
where cooling liquid circulates. Valve seats are inserted into cylinder heads. Nozzles 14 (3
for each cylinder head), racks 13, rocking arms axles 8 with rocking arms 7, covers for cyl-
inder heads 17 (figure 3.1.1) and cover caps 16 which cover the valve mechanism are
mounted onto cylinder heads. There are three heating plugs (figure 3.1.2) installed at each
cylinder head on the left.
Gasket 19 is mounted between cylinder heads 18 (figure 3.1.1) and cylinder block
20 for the connection thickening.
The main parts of the crank-and-rod mechanism are crankshaft 25 with main and
connecting-rod bearings, flywheel 22, pistons 14 with piston rings and pins 12, connecting
rods 13. Drive gear of valve timing gear (crankshaft gear) and drive gear of oil pump, drive
pulley of oil pump, alternator, air conditioner compressor are mounted with force on the
crankshaft front end. To reduce the level of the crankshaft torque vibrations, torque vibra-
tion damper 3 is mounted on the pulley hub. Piston 14 is made of aluminum alloy. A com-
bustion chamber is installed in the piston-head. In the upper part of the piston there are
three furrows – compression rings are mounted into the first two furrows, and an oil-
scraper ring with an expander is mounted into the third furrow. Piston pin 12 is hollow, ax-
ial movement of the pin in the piston pin boss is limited by locking rings. Connecting rod 13
is steel of I section. A bushing is pressed into the connecting rod upper head. In the upper
head of the connecting rod and the bushing there is a hole to provide piston pin lubrication.
Flywheel 22 is fixed to the crankshaft flange by means of bolts. A steel toothed rim is
pressed onto the flywheel.
Valve timing gear consists of gears, cam shaft 1 (figure 3.1.2), inlet and outlet
valves and parts for their mounting and drive of pushers 2, wading rods 5, rocking arms 7,
adjusting screws with nuts, disks 9, dowels 10, springs 11 and 12, racks 13 and rocking
arms axles 8. A cam shaft is four-support, gets rotation from the crankshaft through timing
gears located under cover 6 (figure 3.1.1). Valve timing gear jaw members are made with
a slight taper due to which pushers perform circular movements during the operation proc-
ess.
The engine lubricating system is combined: some parts are lubricated under pres-
sure, some – by spattering. Bearings of the cam and crankshafts, the idle gear bushing,
rocking arms bushings, crankshaft rod bearings of the pneumatic compressor, the turbo-
charger shaft bearing are lubricated under pressure from oil pump. Sleeves, pistons, pis-
ton pins, wading rods, pushers, the cam shaft jaw members and the fuel pump parts are
lubricated by spattering. The lubricating system consists of oil pump of gear type 3 (figure
3.1.3), oil filter with paper filter cartridge 4, centrifugal oil filter 7, fluid-oil heat exchanger 6.
There is overflow valve 5 in the oil pump adjusted for pressure from 0.7 to 0.75
MPa. If the pressure increases above the specified value, oil bleeds off from the decreas-
ing space to the increasing space. The adjustment is carried out at the stand by means of
adjusting washers. The oil pump through oil receiver 2 takes oil from oil crankcase 1 and
through passages in the cylinder block supplies it to the full-flow oil filter with a paper filter
cartridge, and the part of oil – to the centrifugal oil filter for cleaning and succeeding dis-
charge to the oil crankcase.
Non-adjustable safety valve 18 is built into filter 4 housing. It is intended for main-
taining oil pressure in the main oil passage from 0.28 to 0.45 MPa. In case oil pressure ex-
ceeds 0.45 MPa, the safety valve opens and excess oil drains to the engine crankcase
through the safety valve. Oil cleaned in oil filter 4 is supplied to the fluid-oil heat-exchanger
which is built in the engine cylinder block. An oil filter cartridge has overflow valve 20. In
case of paper filter cartridge excessive clogging or while starting the engine with cold oil
when filter cartridge resistance increases over 0.13 to 0.17 MPa, the overflow valve opens
and oil is supplied to the oil passage without entering filter paper. The overflow valve is
non-adjustable.
Cooled oil is supplied from the fluid-oil heat-exchanger through passages in the cyl-
inder block to the main oil passage from which it is supplied through passages in the cylin-
https://tractormanualz.com/