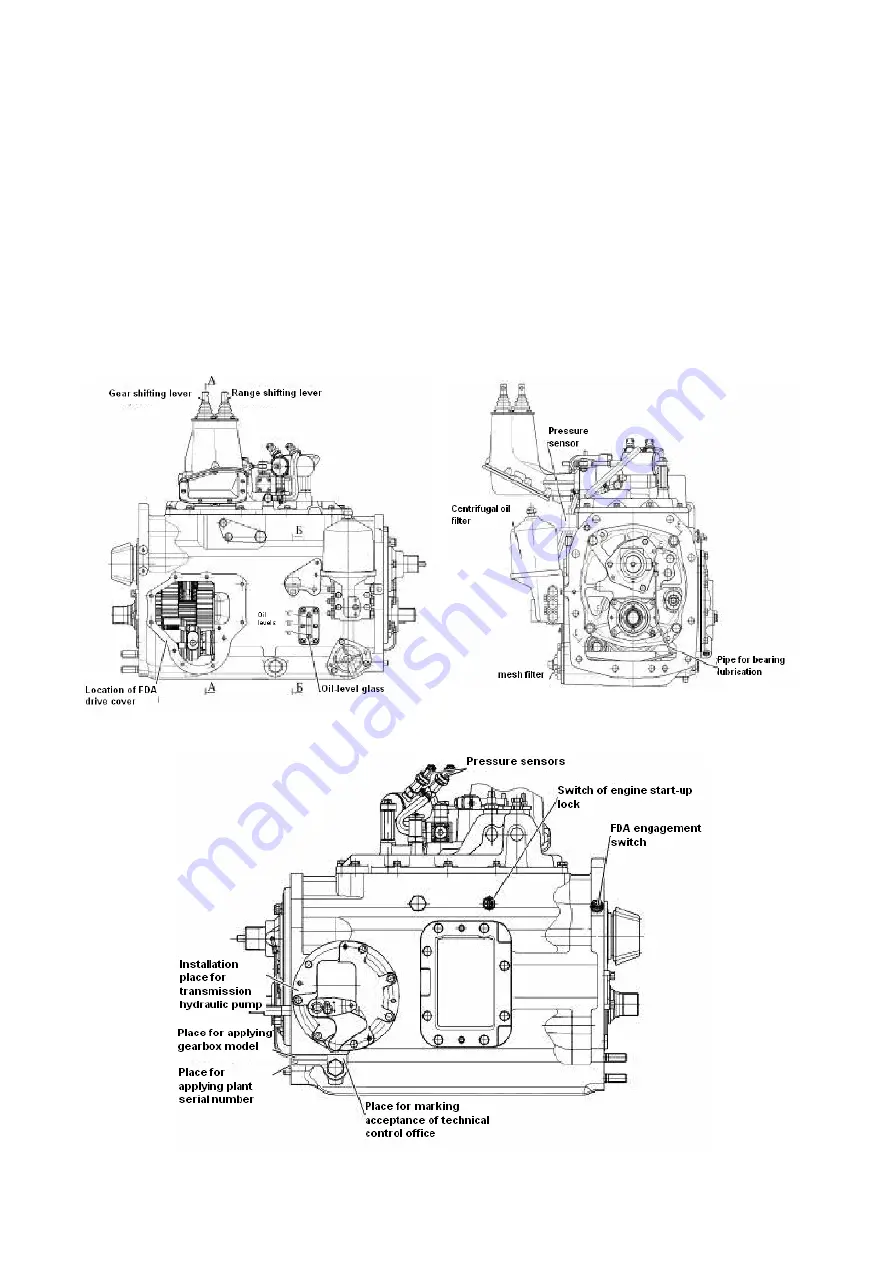
2022.3-0000010 OM
83
3.3 Gearbox
3.3.1 General information
The gearbox is mechanical, fixed-ratio with constant-mesh gears, range-type (four
ranges for forward travel and two ranges for the reverse), six speeds within each range are
shifted by means of synchronizers. The gearbox provides 24 speeds for forward travel and
12 speeds for the reverse, and also FDA drive. The gearbox layout is introduced in figure
3.3.1.
ATTENTION: OIL LEVEL IN THE TRANSMISSION SHALL ALWAYS STAY AT THE
MARK “ ” ±5 MM WHEN CHECKED OVER THE OIL-LEVEL GLASS. TO ENSURE
NORMAL OPERATION OF THE GEARBOX AND THE COUPLING CLUTCH IT IS NEC-
ESSARY TO WATCH THE VALUE OF OIL OPERATING PRESSURE IN THE TRANS-
MISSION!
Figure 3.3.1 – Gearbox layout (cuts
and
are shown in figure 3.3.2)
https://tractormanualz.com/