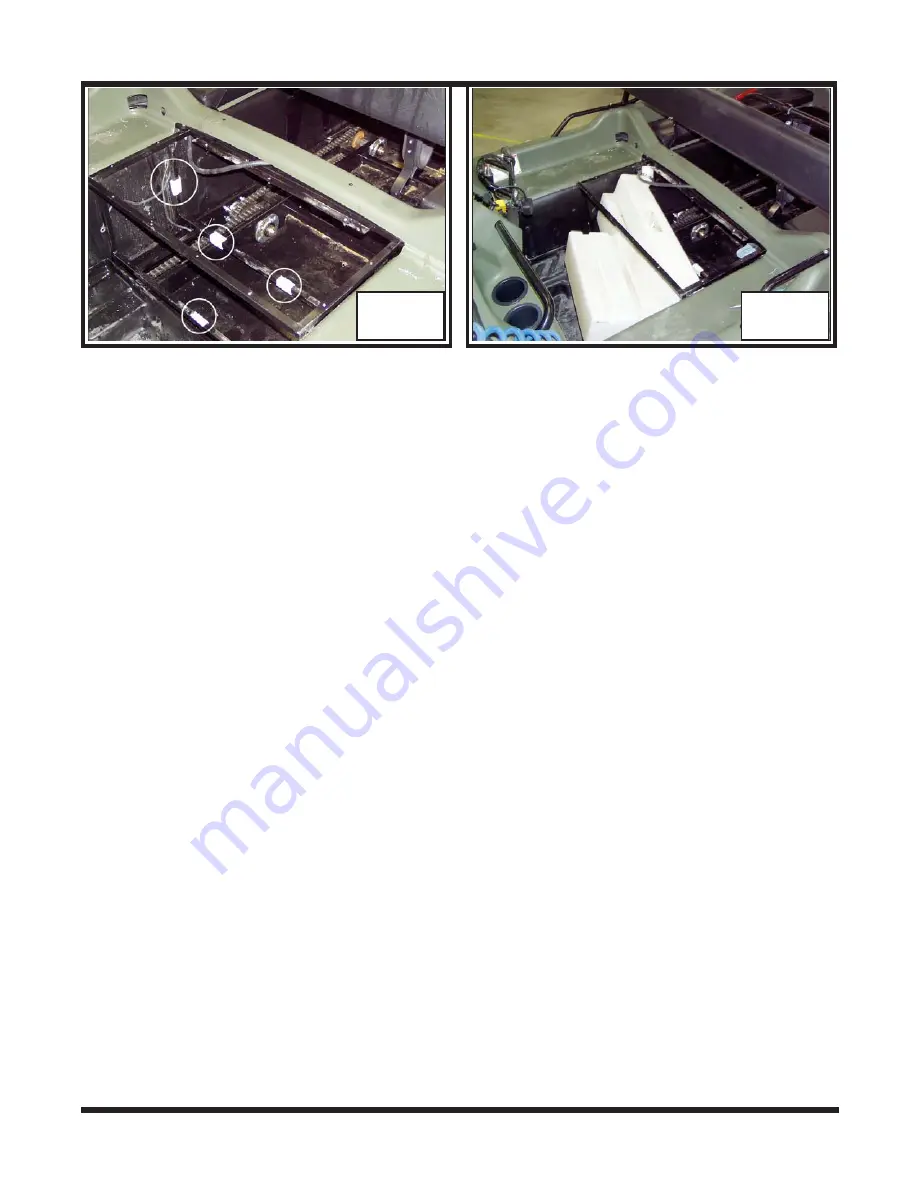
Fuel System Argo Service Manual
Ontario Drive & Gear Limited www.odg.com
PH.(519)- 662-2840 FAX (519)- 662-2421
FS-5A
2.
Slip the new or cleaned tank into the vehicle from the drivers compartment, recon-
necting the filler hose to the tank at the same time and secure it with the gear clamp.
Be sure to reconnect the fuel vent hose at the filler neck and ensure that it is facing
up and not kinked or pinched in any way.
3.
With the tank in place, reinstall the tool box and secure with rivets.
4.
Replace the fuel filter with a new one.
6.
Place the front seat back into the vehicle.
•
loose or broken clamps
•
loose connection in pick-up pipe
IMPOR
IMPOR
IMPOR
IMPOR
IMPORT
T
T
T
TANT
ANT
ANT
ANT
ANT
5.
Reinstall the battery
FS-3
FS-4