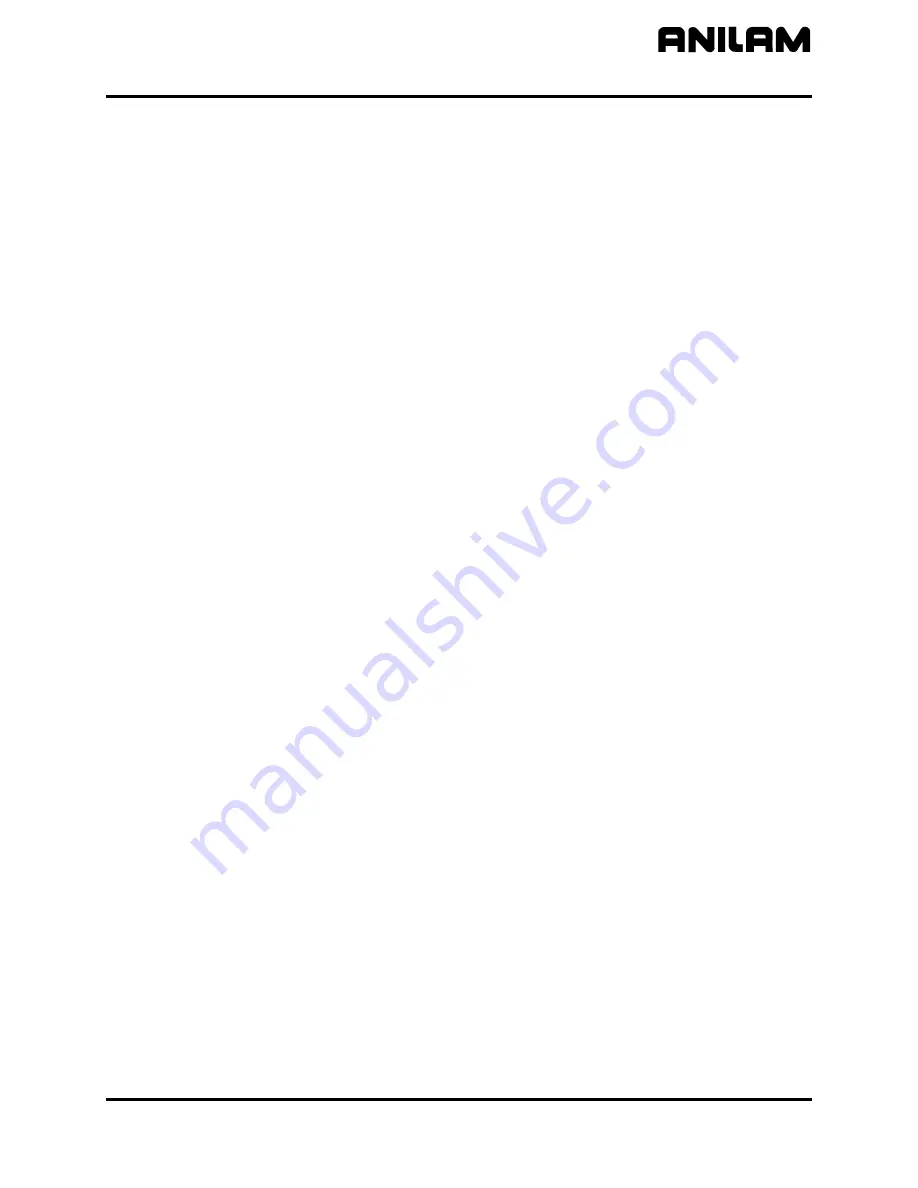
CNC Setup Utility Manual
P/N 70000490C - Tuning the Current, Velocity, and Position Controller
All rights reserved. Subject to change without notice.
5-11
10-December-04
Frequency Tune – Manual Test
This test finds the critical frequency at which an axis starts oscillating
when its velocity proportional gain is increased. Depending on this
frequency,
MC_2
x
18
(Fir filter),
MC_2
x
35
(notch filter center frequency)
and
MC_2
x
36
(notch filter damping) are set.
When the test is started, 4 parameter entries are displayed on the screen:
MC_2
x
18:
x
Velocity Filter (FIR filter)
MC_2
x
22:
x
Vel. Control Prop. Gain (mAs/rev)
MC_2
x
35:
x
Torque Notch Filter Freq. (.1 Hz)
MC_2
x
36:
x
Torque Notch Filter Damp. (.1 dB)
The initial values for all the parameters are taken from the values stored
in the setup. In order to find the oscillation frequency, the entries for
MC_2
x
18
,
MC_2
x
35
, and
MC_2
x
36
should be set to zero to eliminate
any kind of filtering. Every time the
Start
key is pressed, the following are
displayed:
A PSD plot is generated
Energy content of the 180 to 700 Hz. frequency band
Oscillation frequency
MC_2
x
22
should be increased little by little (by pressing
I
) and a step
response should be commanded (by pressing
Start
) after each parameter
change to check the energy percentage and the oscillation frequency
results. When the energy percentage gets close to 100% (axis will start to
make a loud noise), the test should be stopped.
If the oscillation frequency is less than 600Hz.:
MC_2
x
18
should be set to 1
MC_2
x
35
should be set to the oscillation frequency multiplied by 10
MC_2
x
36
should be set to 60.
If the oscillation frequency is between 600 and 700 Hz.:
Only
MC_2
x
18
should be set to 1
If the oscillation frequency is more than 700Hz.:
MC_2
x
18
should be set to 2.
To save the frequency values
After entering the values, press
Save
(
F10
). If the test is cancelled, the
parameters keep their original values.