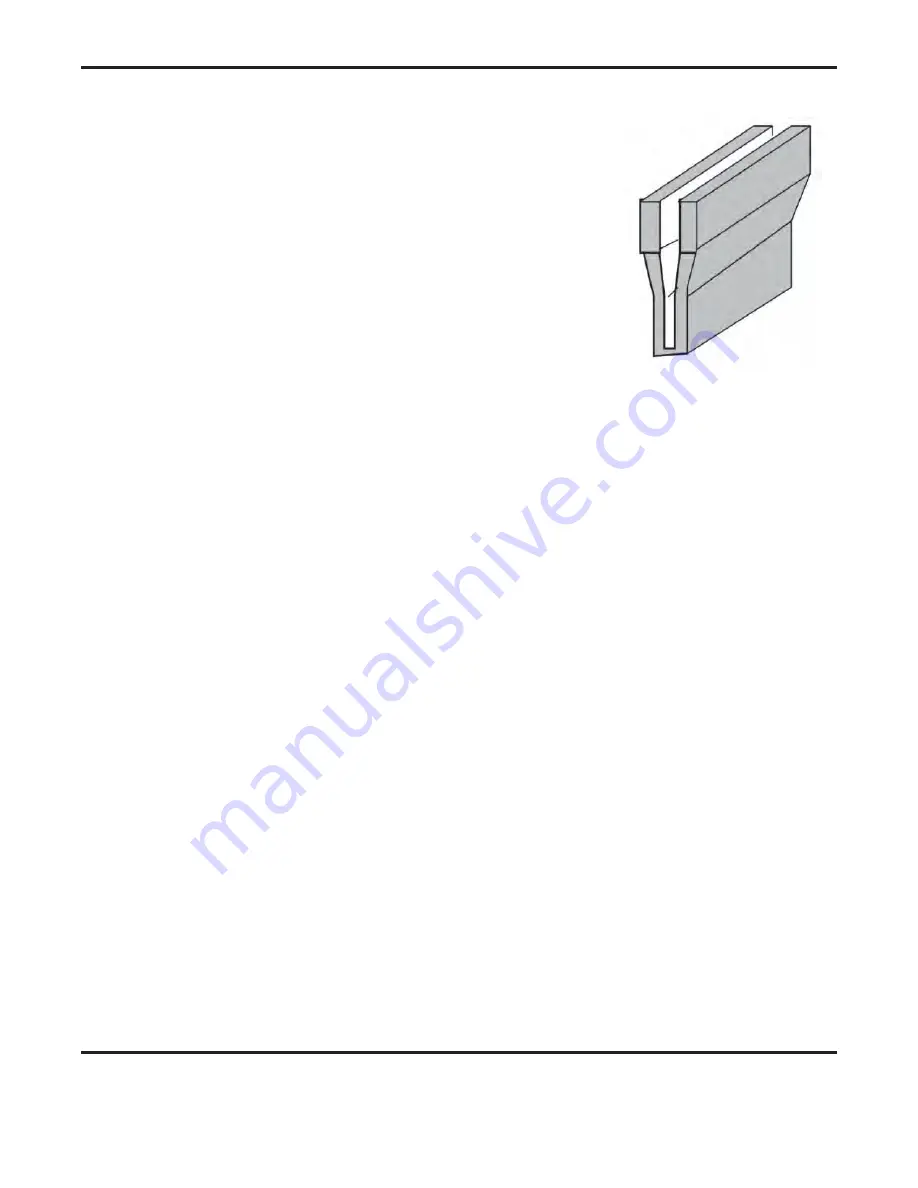
APPENDIX E: GUIDELINES FOR REFLOW SOLDERING
UNIFLOW
®
4 PULSED HEAT CONTROL
E-8
990-908
Thermode Manufacturing And Temperature Characteristics
Modern wire erosion techniques such as EDM and advanced materials
have allowed the manufacture of precisely designed thermodes to suit
most applications. Three-dimensional thermodes pass the current around
the face and thus have zero voltage potential across the traces. These
technological advances in machining processes produce designs with
constant temperature across the length, and special alloys achieve flatness
and co-planarity under heating. Solder will not wet to the materials used
and they are resilient to oxidization.
Tooling And Part Positioning
Heat resilient high temperature plastic such as peek (trade name Ketron) or tuffnel should be used under
the reflow area to prevent heat sinking from the bond area. Tooling nests should be totally flat as the
quality of the process depends upon achieving an equal distribution of heat when the pressure from the
thermode is applied. The best finishing technique is to grind the surface in preference to milling. If
possible, parts should be located on tooling pins adjacent to the reflow area. It is common practice for
the tooling holes in the flex to be reinforced with copper trace for strength and accuracy. If no tooling
holes are possible, the parts can be positioned and tooled from a square edge. As the flex is not rigid
vacuum holes in the part nest may be required to hold it flat. For fine pitch flex, an alignment x-y stage
and camera system may be useful. It is important to take into account any tolerances or batch-to-batch
variations in size when designing the part fixturing.
Preparation
It is more common for both parts to be previously solder plated. If this is not the case, it is still possible
to achieve wetting between a single sided flex design and a base pad plated with gold or tin. The base
plating of the two parts is often enough solder to achieve a reliable joint with a single sided flex.
Most flex designs, however, will require additional solder normally applied by the screen printing
process and previously reflowed (quantities are described earlier). For finer pitch applications the solder
is normally hot air leveled prior to the reflow process. Hot air leveling allows even distribution of the
solder along the pad and good thermal transfer resulting from a flatter surface. This process also makes
alignment under the pressure of the heated bar easier to maintain. Parts must be free of dirt and dust and
generally clean and oxide free. Flux is normally used to ensure any oxide barrier is removed to allow
proper wetting to occur.
Summary of Contents for UNIFLOW 4 REMOTE
Page 1: ...990 908 REV K PULSED HEAT CONTROL UNIFLOW 4 UNIFLOW 4 REMOTE OPERATION MANUAL ...
Page 18: ...UNIFLOW 4 PULSED HEAT CONTROL xviii 990 908 ...
Page 19: ...UNIFLOW 4 PULSED HEAT CONTROL 990 908 xix ...
Page 20: ...UNIFLOW 4 PULSED HEAT CONTROL xx 990 908 ...
Page 21: ...UNIFLOW 4 PULSED HEAT CONTROL 990 908 xxi ...
Page 26: ......
Page 36: ......
Page 50: ......
Page 96: ......
Page 106: ......