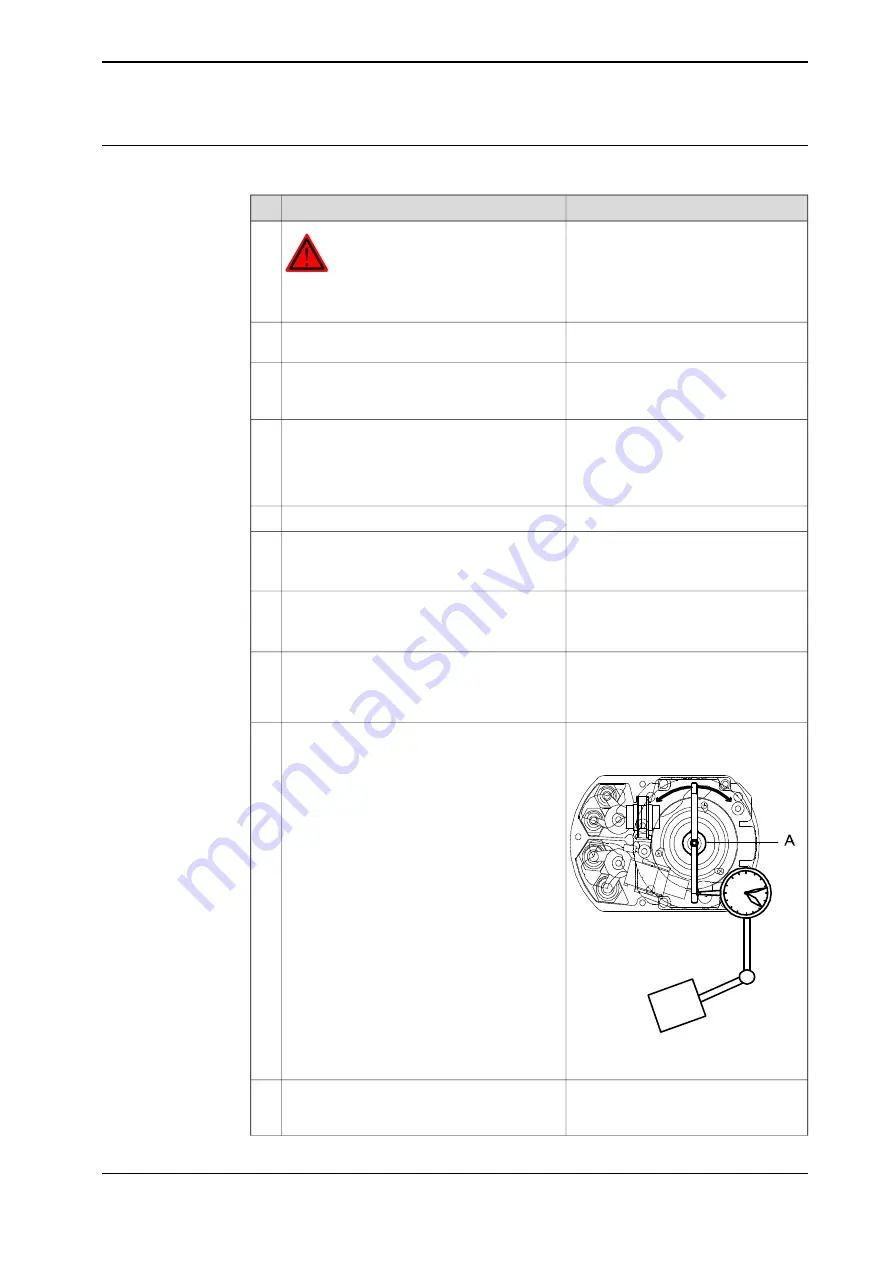
Refitting, motor axis 3
The procedure below details how to refit the motor, axis 3.
Note/Illustration
Action
DANGER
Turn off all electric power, hydraulic and
pneumatic pressure supplies to the robot!
1
Check that the assembly surfaces are clean
and the motor is unscratched.
2
Always mount a new one, see art. no.
in section
.
Fit a new
o-ring
to the motor.
3
Note the position of the motor! Use the
mark on the motor base, made before
removal. Also see the orientation holes
on the motor cover, shown in the figure
Location of motor, axis 3 on page 178
Fit the motor, by gently lifting it straight on.
4
Tightening torque: 2 Nm.
Tighten the four screws lightly.
5
Connect to connector R3.MP3:
•
+: pin 7
•
-: pin 8
In order to release the brakes, connect the 24
VDC power supply to the motor.
6
See the figure below.
Fit the
measuring tool
to the rear of the motor.
7
Art. no. is specified in
See the figure below.
Rotate the motor shaft several turns, using
the measuring tool.
There must always be some backlash, mean-
ing that the shaft should go easy to rotate!
8
The tip of the dial indicator must
measure on a 50 mm radius from the
center of the motor shaft.
xx0200000473
Place the tip of a dial indicator against the
scribed mark on the measuring tool.
9
A Measuring tool
Set the gear play to 0.02 mm, which corres-
ponds to a reading on the dial indicator of 0.13
mm.
10
Continues on next page
Product manual - IRB 2400
181
3HAC022031-001 Revision: P
© Copyright 2004-2018 ABB. All rights reserved.
4 Repair
4.7.3 Replacement of motor, axis 3
Continued
Summary of Contents for IRB 2400 Series
Page 1: ...ROBOTICS Product manual IRB 2400 ...
Page 8: ...This page is intentionally left blank ...
Page 18: ...This page is intentionally left blank ...
Page 204: ...This page is intentionally left blank ...
Page 220: ...This page is intentionally left blank ...
Page 232: ...This page is intentionally left blank ...
Page 234: ...This page is intentionally left blank ...
Page 240: ......
Page 241: ......