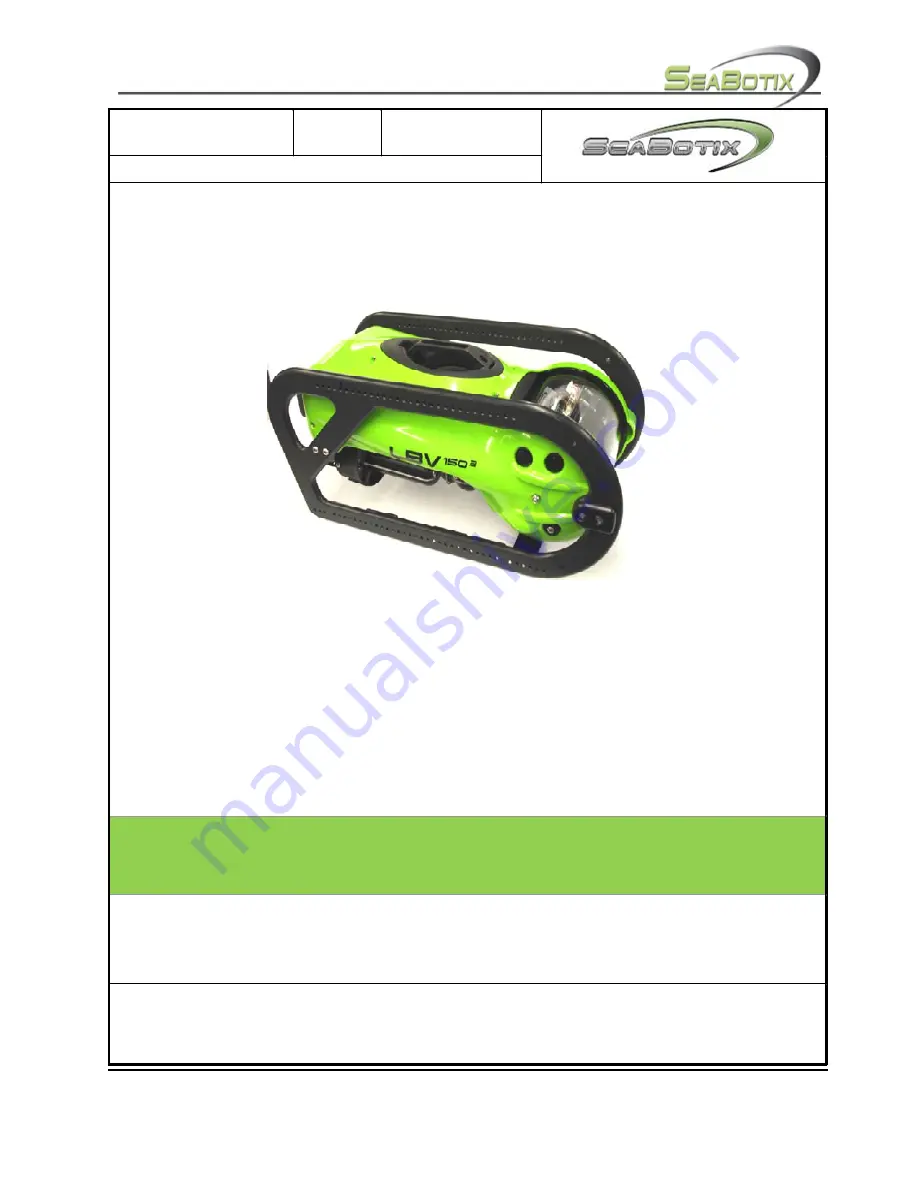
Title:
LBV150
Revision:
B
Revision Date:
27 Jan 10
Document Number:
DOCS-
001
©2009 SeaBotix Inc., all rights reserved
User’s
Manual
Proprietary
Notice:
Words
and
logos
marked
with
®
or
™
are
registered
trademarks
or
trademarks
of
their
respective
owners.
No
license
under
any
copyright,
trademark,
patent
or
other
intellectual
property
right
of
SeaBotix
or
any
third
party
are
granted
by
implication
in
connection
therewith.
This
Document
is
being
furnished
in
confidence
by
SeaBotix
Inc.
This
Document
and
the
information
disclosed
herein
are
proprietary
data
of
SeaBotix
Inc.
Neither
this
Document
nor
the
information
contained
within
shall
be
used,
reproduced,
or
disclosed
to
third
parties
without
the
express
written
authorization
of
SeaBotix
Inc.
Use
of
this
Document
for
other
than
the
intended
purpose
is
strictly
prohibited.
Head Office
: SeaBotix Inc., 2877 Historic Decatur Road STE 100, San Diego, CA 92106 USA +1 (619) 450-4000
Australia Office
: SeaBotix Australia Pty Ltd.8A Sparks Road, Henderson, WA 6166, Aus61 (0)8 9437-5400