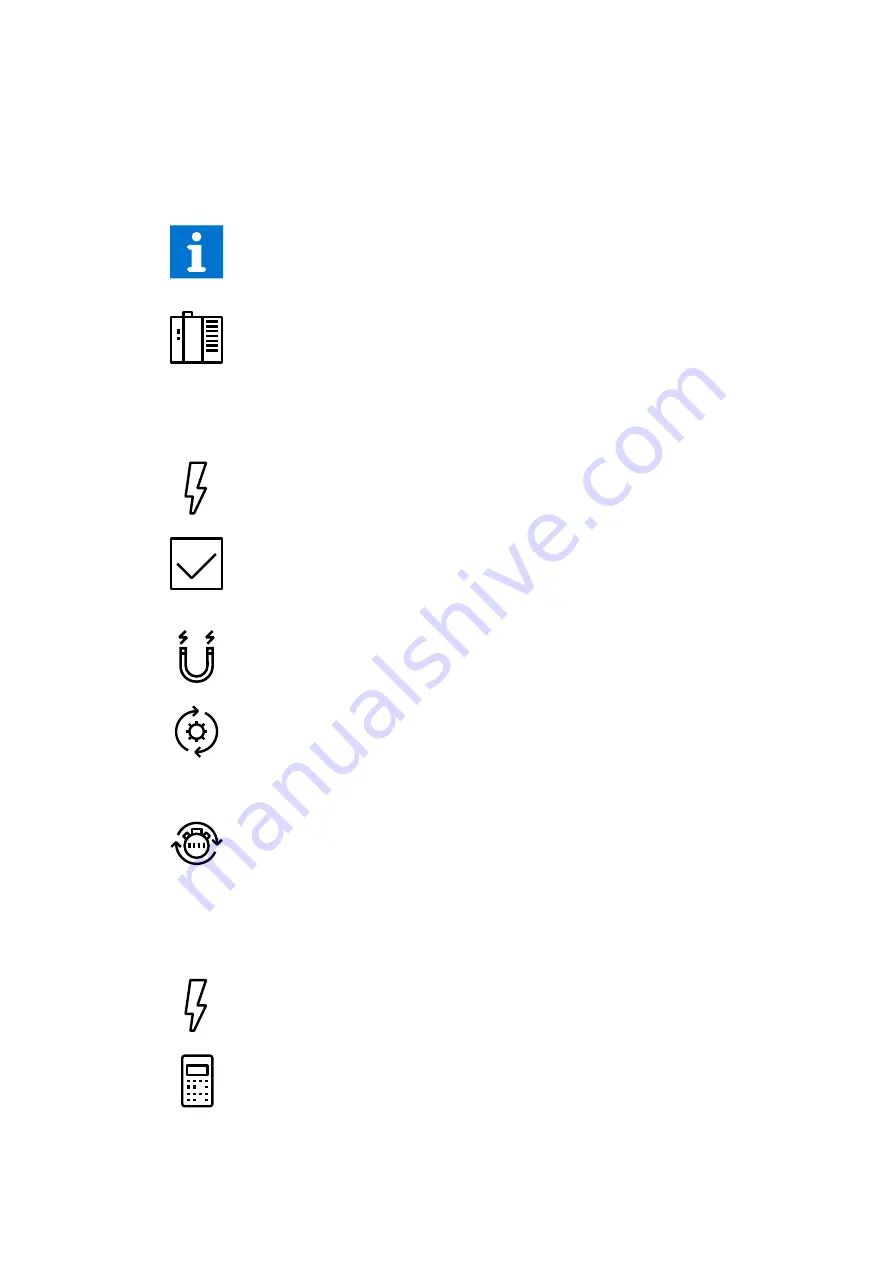
09 OPERATION
3BHS206977 E01 REV H
ACS1000I AIR-COOLED
USER MANUAL
115/174
9.5
Status messages
This section lists the messages of the main operating states the drive passes through, when it
is put into operation, when it is stopped, or when a fault condition has occurred. The messages
are sent to the higher-level control system and are displayed on the CDP control panel of
the drive.
For information on other status messages, such as fault status messages in
particular, see the status words in the “Appendix G – Signal and parameter table” of
the drive.
RdyForMCBOn
The status message signals that the drive is healthy and ready for the ON
command. The ON command initiates the charging of the DC-link capacitors and
the closing of the main circuit breaker of the drive. Depending on the control
place, the command can either be sent from the higher-level control system to the
drive or be initiated by pressing the Main circuit online pushbutton on the control
compartment door.
Charging
The status message
RdyForMCBOn
changes to
Charging
when the DC-link
capacitors of the drive are being charged.
Rdy to Strt
The status message
Rdy to Strt
tells the operator that the drive is energized and
ready for operation. As soon as the start command is initiated, the motor is
magnetized and the drive starts to modulate.
Magnetizing
The status message
Rdy to Strt
changes to
Magnetizing
when the firing pulses of
the inverter are released.
Running
When the drive is in
Running
state, it is running and operating according to the set
speed or torque reference value. When in remote control mode, the reference
value is set by the higher-level control system. When in local control mode, the
value is entered into the CDP control panel.
Stopping
I
ndicates that the drive has received a stop command and that a ramp or coast
stop has been initiated. The stopping mode depends on the parameter setting.
The status message changes to
Rdy to Strt
when the zero speed threshold
is reached.
When a start command is given while the drive is stopping, the drive resumes
operation and the status message changes to Running again.
Discharging
The status message
Rdy to Strt
changes to
Discharging
when the MCB has
opened and the DC-link capacitors are discharging.
Tripped
The status message indicates that a fault condition has occurred that requires a
shutdown of the drive. The status message always alternates with the specific
fault message. The type of shutdown depends on the fault class the fault
condition is assigned to in the drive software.
Summary of Contents for ACS1000i air-cooled
Page 1: ... MEDIUM VOLTAGE AC DRIVES ACS1000i air cooled User manual ...
Page 3: ...Contents ACS1000i air cooled User manual ...
Page 5: ... 01 About this manual 01 5 16 ...
Page 16: ......
Page 17: ... 02 Important safety information 02 17 28 ...
Page 28: ......
Page 29: ... 03 Power electronics and cabinet features03 29 56 ...
Page 57: ... 04 Control system 04 57 70 ...
Page 71: ... 05 Transportation storage and disposal05 71 78 ...
Page 78: ......
Page 79: ... 06 Mechanical installation 06 79 88 ...
Page 88: ......
Page 89: ... 07 Electrical installation07 89 104 ...
Page 105: ... 08 Commissioning 08 105 110 ...
Page 110: ......
Page 111: ... 09 Operation 09 111 124 ...
Page 125: ... 10 CDP control panel 10 125 148 ...
Page 149: ... 11 Preventive and corrective maintenance 11 149 172 ...
Page 173: ......