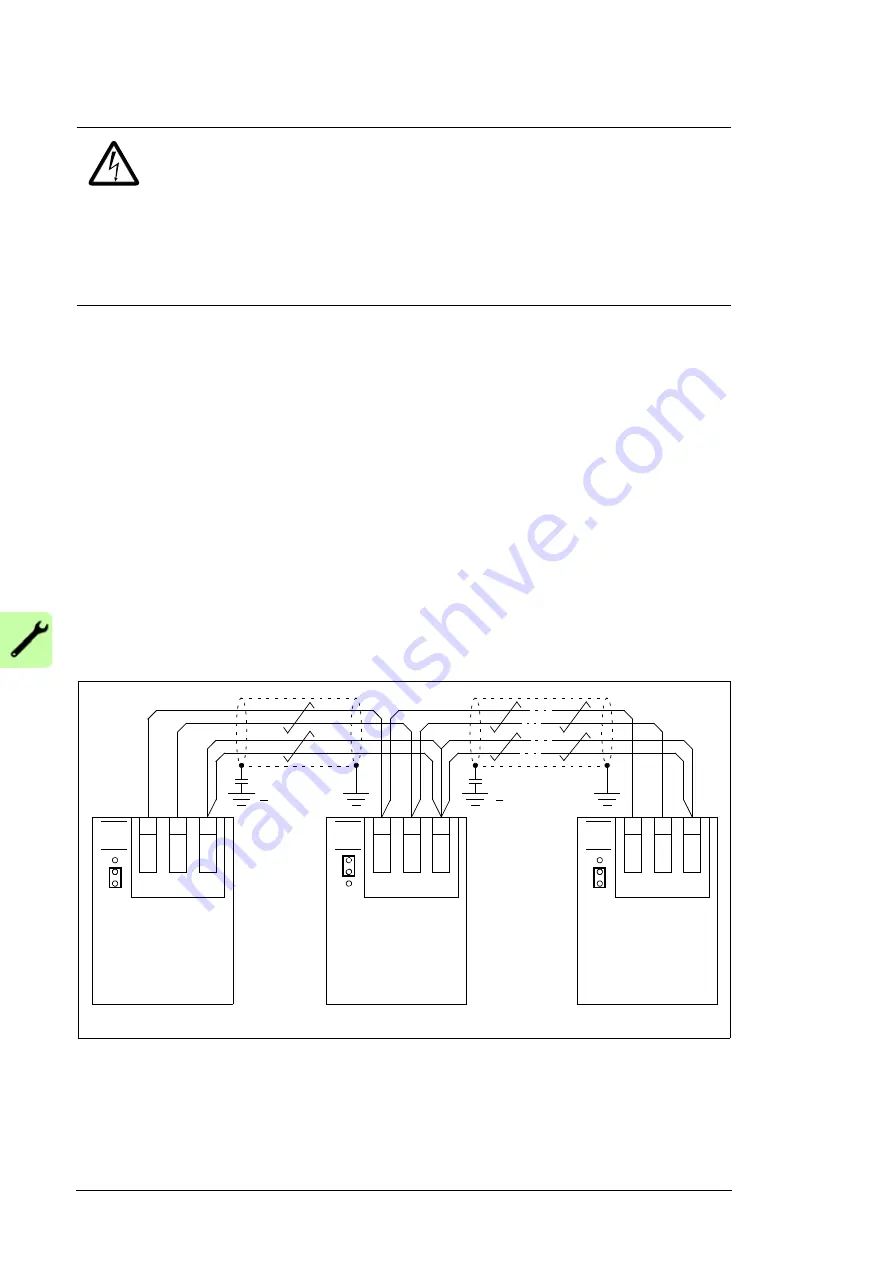
98 Installation
WARNING!
As the inputs pictured above are not insulated according to
IEC 60664, the connection of the motor temperature sensor requires double or
reinforced insulation between motor live parts and the sensor. If the assembly
does not fulfil the requirement,
• the I/O board terminals must be protected against contact and must not be
connected to other equipment, or
• the temperature sensor must be isolated from the I/O terminals.
Start interlock (XDI:A)
Terminal XDI:A must be jumpered to XD24:3 to enable the drive start.
Drive-to-drive link (XD2D)
The drive-to-drive link is a daisy-chained RS-485 transmission line that allows basic
master/follower communication with one master drive and multiple followers.
Termination activation jumper T (see section
above) next to this terminal block
must be set to the ON position on the drives at the ends of the drive-to-drive link. On
intermediate drives, the jumper must be set to the OFF position.
Shielded twisted-pair cable (~100 ohm, for example PROFIBUS-compatible cable) must
be used for the wiring. For best immunity, high quality cable is recommended. The cable
should be kept as short as possible; the maximum length of the link is 100 meters (328 ft).
Unnecessary loops and running the cable near power cables (such as motor cables) must
be avoided. The cable shields must be grounded to the control cable clamp plate on the
drive as shown on page
.
The following diagram shows the wiring of the drive-to-drive link.
Safe torque off (XSTO)
For the drive to start, both connections (OUT1 to IN1, and OUT2 to IN2) must be closed.
By default, the terminal block has jumpers to close the circuit. Remove the jumpers before
connecting an external Safe torque off circuitry to the drive. See page
XD2D
...
1
T
J3
Termination
ON
JCU
Drive 1
B
2
A
3
BG
N
D
XD2D
1
J3
Termination
OFF
JCU
Drive 2
B
2
A
3
BG
N
D
T
XD2D
1
T
J3
Termination
ON
JCU
Drive n
B
2
A
3
BG
N
D
3.3 nF
> 630 V AC
3.3 nF
> 630 V AC
Summary of Contents for ACQ810-04
Page 4: ......
Page 10: ...10 ...
Page 22: ...22 Introduction to the manual ...
Page 42: ...42 Planning the cabinet installation ...
Page 75: ...Installation 75 Assembly drawing frame G1 ...
Page 76: ...76 Installation Assembly drawing frame G2 ...
Page 83: ...Installation 83 3 6a 6b 5 4 8 4 8 6a 6b 7a 7b 7b ...
Page 84: ...84 Installation Assembly drawing of installing the drive module to the cabinet frame G1 ...
Page 85: ...Installation 85 Assembly drawing of installing the drive module to the cabinet frame G2 ...
Page 100: ...100 Installation ...
Page 104: ...104 Installation checklist ...
Page 106: ...106 Start up ...
Page 108: ...108 Fault tracing ...
Page 128: ...128 Technical data ...
Page 130: ...130 Dimension drawings Frame G1 Drive module dimensions ...
Page 131: ...Dimension drawings 131 Frame G1 Drive module dimensions with optional cabling panels H381 ...
Page 132: ...132 Dimension drawings ...
Page 133: ...Dimension drawings 133 Frame G1 Cabling panels H381 installed into a Rittal TS 8 cabinet ...
Page 134: ...134 Dimension drawings Frame G2 Drive module dimensions ...
Page 135: ...Dimension drawings 135 Frame G2 Drive module dimensions with optional cabling panels H381 ...
Page 136: ...136 Dimension drawings ...
Page 137: ...Dimension drawings 137 Frame G2 Cabling panels H381 installed into a Rittal TS 8 cabinet ...
Page 138: ...138 Dimension drawings Bottom plate ...
Page 142: ...142 du dt filters ...
Page 144: ...3AUA0000120538 Rev A EN 2012 06 27 Contact us www abb com drives www abb com drivespartners ...