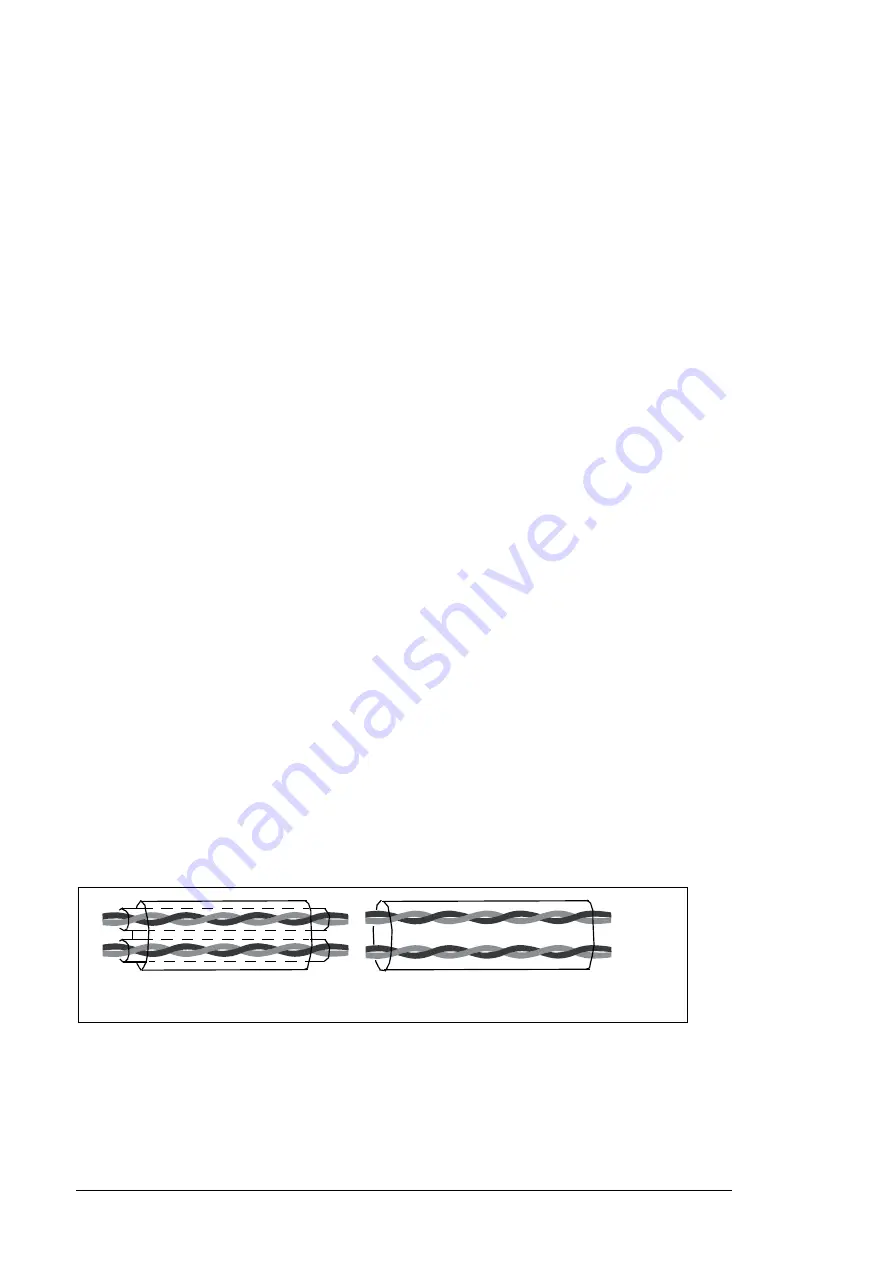
52 Planning the electrical installation
Additional US requirements
Use type MC continuous corrugated aluminum armor cable with symmetrical grounds or
shielded power cable for the motor cables if metallic conduit is not used. For the North
American market, 600 V AC cable is accepted for up to 500 V AC. For drives rated over
100 amperes, the power cables must be rated for 75
°
C (167
°
F).
Conduit
Couple separate parts of a conduit together: bridge the joints with a ground conductor
bonded to the conduit on each side of the joint. Bond the conduits also to the drive
enclosure and motor frame. Use separate conduits for input power, motor, brake resistor,
and control wiring. When conduit is employed, type MC continuous corrugated aluminium
armor cable or shielded cable is not required. A dedicated ground cable is always
required.
Note
: Do not run motor wiring from more than one drive in the same conduit.
Armored cable / shielded power cable
Six conductor (3 phases and 3 ground) type MC continuous corrugated aluminum armor
cable with symmetrical grounds is available from the following suppliers (trade names in
parentheses):
•
Anixter Wire & Cable (Philsheath)
•
BICC General Corp (Philsheath)
•
Rockbestos Co. (Gardex)
•
Oaknite (CLX).
Shielded power cables are available from Belden, LAPPKABEL (ÖLFLEX) and Pirelli.
Selecting the control cables
Shielding
All control cables must be shielded.
Use a double-shielded twisted pair cable for analog signals. This type of cable is
recommended for the pulse encoder signals also. Employ one individually shielded pair for
each signal. Do not use common return for different analog signals.
A double-shielded cable is the best alternative for low-voltage digital signals but single-
shielded twisted pair cable is also usable.
Signals in separate cables
Run analog and digital signals in separate, shielded cables.
Never mix 24 V DC and 115/230 V AC signals in the same cable.
Double-shielded twisted pair
cable
Single-shielded twisted pair
cable
Summary of Contents for ACQ810-04
Page 4: ......
Page 10: ...10 ...
Page 22: ...22 Introduction to the manual ...
Page 42: ...42 Planning the cabinet installation ...
Page 75: ...Installation 75 Assembly drawing frame G1 ...
Page 76: ...76 Installation Assembly drawing frame G2 ...
Page 83: ...Installation 83 3 6a 6b 5 4 8 4 8 6a 6b 7a 7b 7b ...
Page 84: ...84 Installation Assembly drawing of installing the drive module to the cabinet frame G1 ...
Page 85: ...Installation 85 Assembly drawing of installing the drive module to the cabinet frame G2 ...
Page 100: ...100 Installation ...
Page 104: ...104 Installation checklist ...
Page 106: ...106 Start up ...
Page 108: ...108 Fault tracing ...
Page 128: ...128 Technical data ...
Page 130: ...130 Dimension drawings Frame G1 Drive module dimensions ...
Page 131: ...Dimension drawings 131 Frame G1 Drive module dimensions with optional cabling panels H381 ...
Page 132: ...132 Dimension drawings ...
Page 133: ...Dimension drawings 133 Frame G1 Cabling panels H381 installed into a Rittal TS 8 cabinet ...
Page 134: ...134 Dimension drawings Frame G2 Drive module dimensions ...
Page 135: ...Dimension drawings 135 Frame G2 Drive module dimensions with optional cabling panels H381 ...
Page 136: ...136 Dimension drawings ...
Page 137: ...Dimension drawings 137 Frame G2 Cabling panels H381 installed into a Rittal TS 8 cabinet ...
Page 138: ...138 Dimension drawings Bottom plate ...
Page 142: ...142 du dt filters ...
Page 144: ...3AUA0000120538 Rev A EN 2012 06 27 Contact us www abb com drives www abb com drivespartners ...