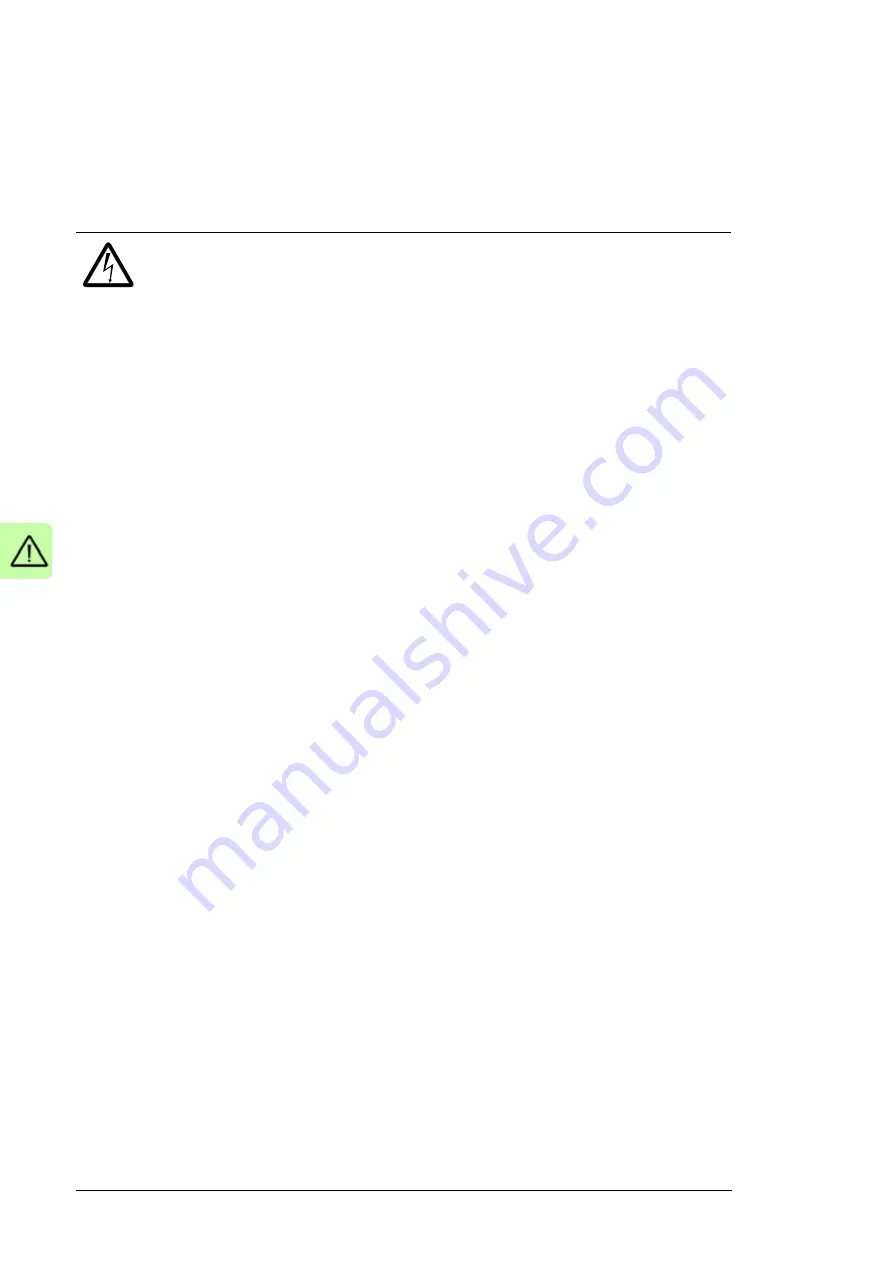
12 Safety instructions
Safety in installation and
maintenance
Electrical safety
These warnings are intended for all who work on the drive, motor cable or motor.
WARNING!
Ignoring the following instructions can cause physical injury or
death, or damage to the equipment:
•
Only qualified electricians are allowed to install and maintain the drive.
•
Never work on the drive, motor cable or motor when main power is applied. After
disconnecting the input power, always wait for 5 min to let the intermediate circuit
capacitors discharge before you start working on the drive, motor or motor cable.
Always ensure by measuring with a multimeter (impedance at least 1 Mohm) that:
1. voltage between drive input phases U1, V1 and W1 and the frame is close to 0 V.
2. voltage between terminals UDC+ and UDC- and the frame is close to 0 V (units
with additional DC busbars).
•
Do not work on the control cables when power is applied to the drive or to the
external control circuits. Externally supplied control circuits may cause dangerous
voltages inside the drive even when the main power on the drive is switched off.
•
Do not make any insulation or voltage withstand tests on the drive or drive modules.
•
When reconnecting the motor cable, always check that the phase order is correct.
Note:
•
The motor cable terminals on the drive are at a dangerously high voltage when the
input power is on, regardless of whether the motor is running or not.
•
The DC terminals (UDC+, UDC-) carry a dangerous DC voltage (over 500 V) when
internally connected to the intermediate DC circuit.
•
Depending on the external wiring, dangerous voltages (115 V, 220 V or 230 V) may
be present on the terminals of relay outputs (XRO1 and XRO2) or Safe torque off
(XSTO).
•
The Safe torque off function does not remove the voltage from the main and
auxiliary circuits.
Summary of Contents for ACQ810-04
Page 4: ......
Page 10: ...10 ...
Page 22: ...22 Introduction to the manual ...
Page 42: ...42 Planning the cabinet installation ...
Page 75: ...Installation 75 Assembly drawing frame G1 ...
Page 76: ...76 Installation Assembly drawing frame G2 ...
Page 83: ...Installation 83 3 6a 6b 5 4 8 4 8 6a 6b 7a 7b 7b ...
Page 84: ...84 Installation Assembly drawing of installing the drive module to the cabinet frame G1 ...
Page 85: ...Installation 85 Assembly drawing of installing the drive module to the cabinet frame G2 ...
Page 100: ...100 Installation ...
Page 104: ...104 Installation checklist ...
Page 106: ...106 Start up ...
Page 108: ...108 Fault tracing ...
Page 128: ...128 Technical data ...
Page 130: ...130 Dimension drawings Frame G1 Drive module dimensions ...
Page 131: ...Dimension drawings 131 Frame G1 Drive module dimensions with optional cabling panels H381 ...
Page 132: ...132 Dimension drawings ...
Page 133: ...Dimension drawings 133 Frame G1 Cabling panels H381 installed into a Rittal TS 8 cabinet ...
Page 134: ...134 Dimension drawings Frame G2 Drive module dimensions ...
Page 135: ...Dimension drawings 135 Frame G2 Drive module dimensions with optional cabling panels H381 ...
Page 136: ...136 Dimension drawings ...
Page 137: ...Dimension drawings 137 Frame G2 Cabling panels H381 installed into a Rittal TS 8 cabinet ...
Page 138: ...138 Dimension drawings Bottom plate ...
Page 142: ...142 du dt filters ...
Page 144: ...3AUA0000120538 Rev A EN 2012 06 27 Contact us www abb com drives www abb com drivespartners ...