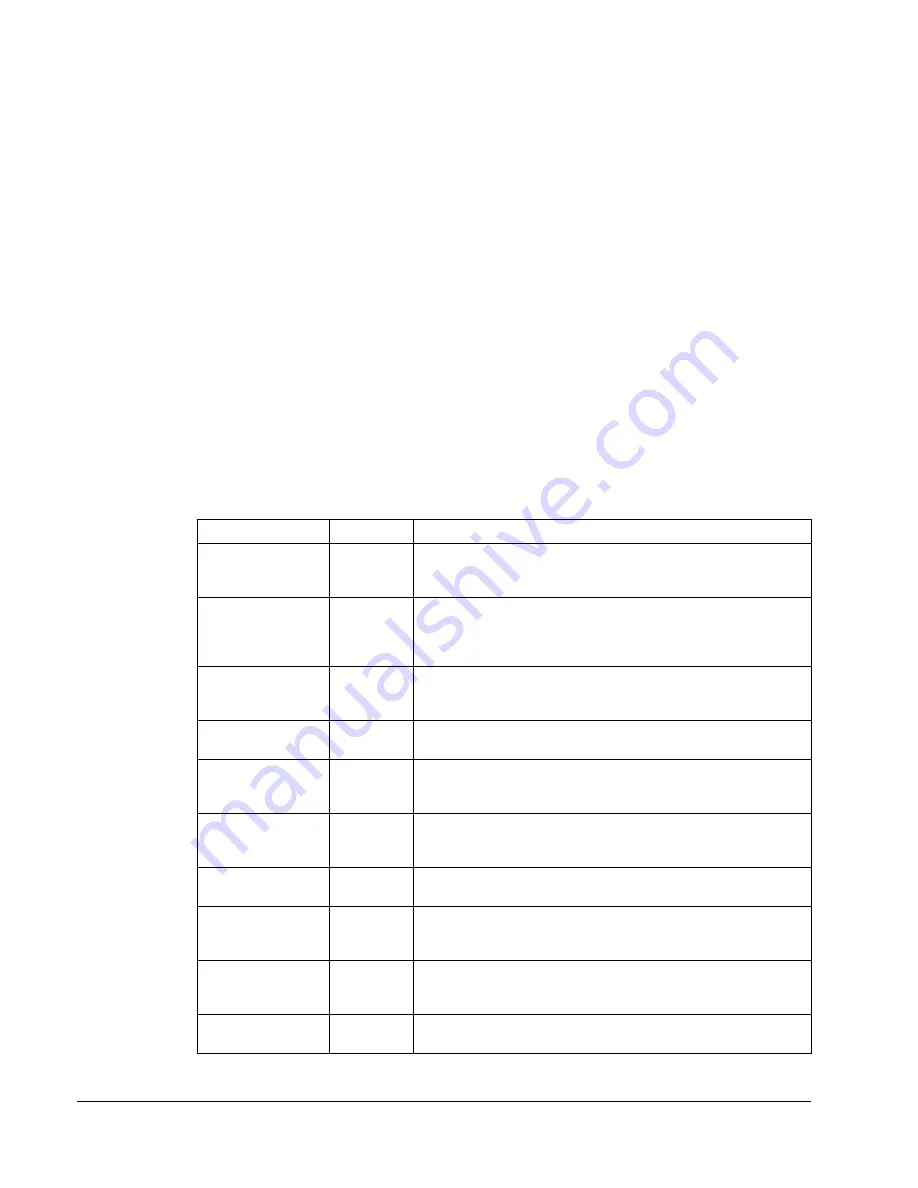
2-174
ACH550 E-Clipse Bypass User’s Manual
Embedded fieldbus
Modbus protocol technical data – system
System overview
The Modbus® protocol was introduced by Modicon, Inc. for use in control
environments featuring Modicon programmable controllers. Due to its ease of use
and implementation, this common PLC language was quickly adopted as a de-facto
standard for integration of a wide variety of master controllers and slave devices.
Modbus is a serial, asynchronous protocol. Transactions are half-duplex, featuring a
single Master controlling one or more Slaves. While RS232 can be used for point-
to-point communication between a single Master and a single Slave, a more
common implementation features a multi-drop EIA 485 network with a single Master
controlling multiple Slaves. The ABB E-Clipse bypass features EIA 485 for its
Modbus physical interface.
RTU
The Modbus specification defines two distinct transmission modes: ASCII and RTU.
The ABB E-Clipse Bypass supports RTU only.
Feature summary
The following Modbus function codes are supported by the system.
Function
Code (Hex)
Description
Read Coil Status
0x01
Read discrete output status. For the system, the individual bits of
the control word are mapped to Coils 1…16. Relay outputs are
mapped sequentially beginning with Coil 33 (e.g. RO1=Coil 33).
Read Discrete Input
Status
0x02
Read discrete inputs status. For the system, the individual bits of
the status word are mapped to Inputs 1…16 or 1…32, depending
on the active profile. Terminal inputs are mapped sequentially
beginning with Input 33 (e.g. DI1=Input 33).
Read Multiple
Holding Registers
0x03
Read multiple holding registers. For the system, the entire
parameter set is mapped as holding registers, as well as
command, status and reference values.
Read Multiple Input
Registers
0x04
Read multiple input registers. For the system, the 2 analog input
channels are mapped as input registers 1 & 2.
Force Single Coil
0x05
Write a single discrete output. For the system, the individual bits
of the control word are mapped to Coils 1…16. Relay outputs are
mapped sequentially beginning with Coil 33 (e.g. RO1=Coil 33).
Write Single
Holding Register
0x06
Write single holding register. For the system, the entire
parameter set is mapped as holding registers, as well as
command, status and reference values.
Diagnostics
0x08
Perform Modbus diagnostics. Subcodes for Query (0x00),
Restart (0x01) & Listen Only (0x04) are supported.
Force Multiple Coils 0x0F
Write multiple discrete outputs. For the system, the individual bits
of the control word are mapped to Coils 1…16. Relay outputs are
mapped sequentially beginning with Coil 33 (e.g. RO1=Coil 33).
Write Multiple
Holding Registers
0x10
Write multiple holding registers. For the system, the entire
parameter set is mapped as holding registers, as well as
command, status and reference values.
Read/Write Multiple
Holding Registers
0x17
This function combines functions 0x03 and 0x10 into a single
command.
Summary of Contents for ACH550-BCR
Page 4: ...iv Manual contents ...
Page 6: ......
Page 12: ...1 8 ACH550 UH User s Manual Table of contents ...
Page 36: ...1 32 ACH550 UH User s Manual Installation ...
Page 70: ...1 66 ACH550 UH User s Manual Application macros ...
Page 335: ...ACH550 UH User s Manual 1 331 Technical data ...
Page 348: ......
Page 382: ...2 36 ACH550 E Clipse Bypass User s Manual Start up ...
Page 398: ...2 52 ACH550 E Clipse Bypass User s Manual Bypass functions overview ...
Page 406: ...2 60 ACH550 E Clipse Bypass User s Manual Application macros ...
Page 544: ...2 198 ACH550 E Clipse Bypass User s Manual Embedded fieldbus ...
Page 584: ...2 238 ACH550 E Clipse Bypass User s Manual Diagnostics ...
Page 608: ......
Page 612: ...3 6 ACH550 UH User s Manual Table of contents ...
Page 622: ...3 16 ACH550 PCR PDR User s Manual Installation ...
Page 641: ......