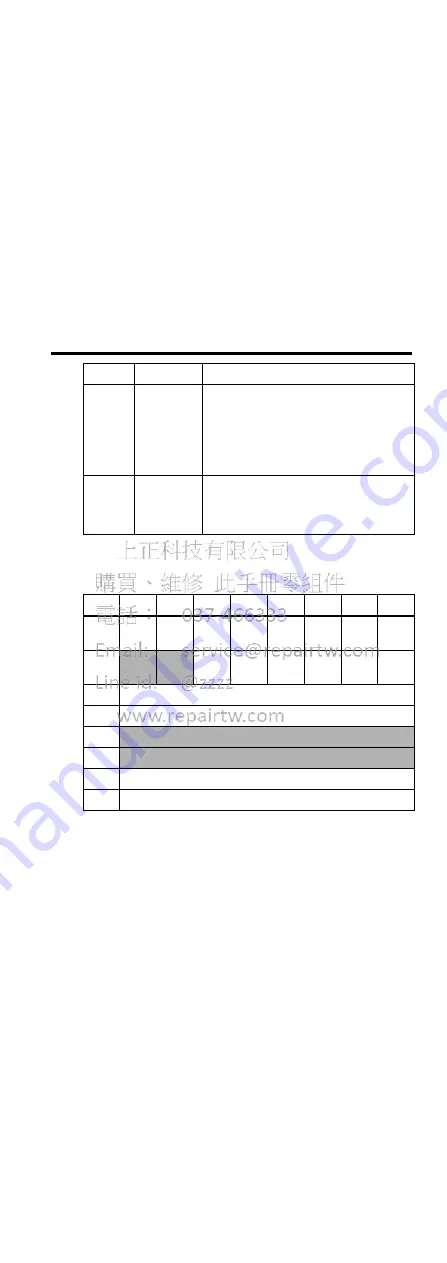
6. Operating with DeviceNet Communications
69
* Terminal MA can be used only from DeviceNet communications. There is
no corresponding external output terminal.
• Output (Inverter
→
Master) Instance 151 (97 Hex)
Byte 1,
bit 7
Terminal
P2
Operates the Inverter’s multi-function
output terminal P2. This function is en-
abled only when Inverter constant n059
is set to 18.
0: Terminal P2 OFF
1: Terminal P2 ON
Bytes
2 and 3
Speed
Reference
Sets the Inverter’s speed reference.
The units depend on the setting in Invert-
er constant n035. The units are not af-
fected by the speed scale (SS) setting.
Byte
Bit 7
Bit 6
Bit 5
Bit 4
Bit 3
Bit 2
Bit 1
Bit 0
0
Fault-
ed
Warn-
ing
Ready
At Ref-
erence
Reset
Rev
Run-
ning
ZSP
Run-
ning
1
---
---
Termi-
nal P2
Termi-
nal P1
Termi-
nal
MA*
Local/
Re-
mote
UV
OPE
2
Speed Actual (Low Byte)
3
Speed Actual (High Byte)
4
---
5
---
6
Output Current (Low Byte)
7
Output Current (High Byte)
Data
Name
Contents