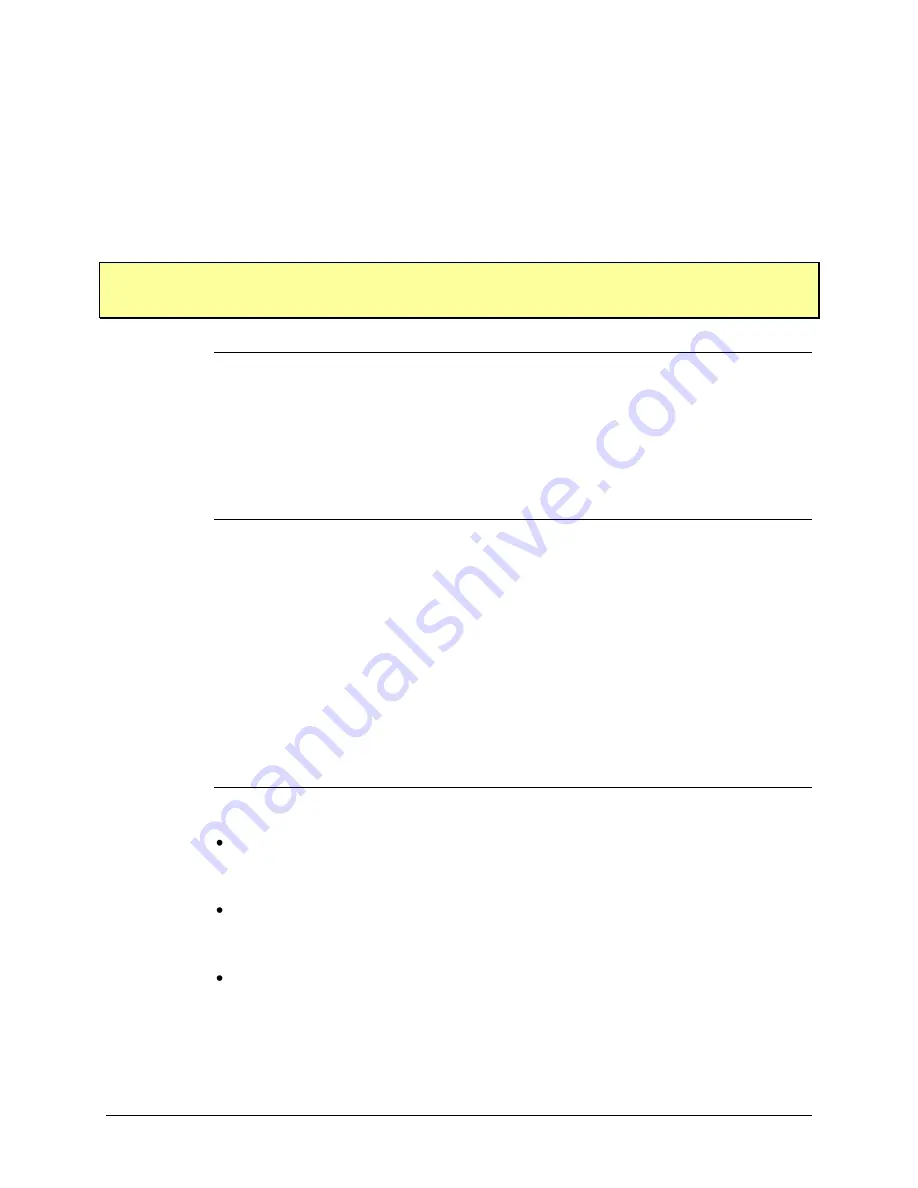
www.vtiinstruments.com
EX1629 Introduction
23
from the theoretical strain is then considered to be due to lead wire desensitization, and a
compensation factor is determined. However, some strain purists argue that shunt calibration is
actually meant to be a verification step and should not be used for this purpose. What is needed,
then, is an automated way to determine the lead wire desensitization error without using shunt
calibration. This can be accomplished using the vtex1629_set_lead_wire_resistance and
vtex1629_set_half_bridge_lead_wire_desensitization functions. An additional API is available to
help
measure
the
lead
wire
resistance,
beginning
with
firmware
version
1.0:
vtex1629_measure_lead_wire_resistance.
NOTE
This functionality was added to the EX1629 after September 2006 in firmware version 1.0. To
ensure compatibity, use the instrument’s embedded web page interface or use the EX1629’s
Shunt Calibration
Shunt calibration can be performed with either the internal 55 kΩ resistor or an external resistor
inserted into the front panel shunt connector. For highest accuracy, the value of this external
resistor should be precisely known. The
connection resistance
characteristic refers to the series
resistance of the switch mechanisms used to route the external resistor into the requested bridge
circuit. This resistance must be considered in conjunction with the raw resistor value when
determining the theoretical simulated strain of the shunt calibration process. The connection
resistance is the same for local or remote connection.
Quarter-Bridge Strain Measurement
The strain dynamic range is slightly different for tension vs. compression. While the dynamic
range of the voltage measurement circuitry is a balanced ±160 mV, the transfer function of strain-
to-voltage is nonlinear for quarter-bridge configuration, and that results in the small disparity.
Quarter-bridge measurement accuracy is noted as being exclusive of lead wire desensitization
errors. This refers to the gain error that is generated by lead wire resistance in series with the
actual strain gage. Depending on the length and gauge of the wire employed, the resultant
resistance can cause errors that are much larger than the underlying instrument accuracy. Precision
measurements consequently demand that lead wire compensation is conducted to eliminate this
error. This compensation can be calculated theoretically if the resistance of the connection wire is
characterized or can be inferred through the shunt calibration process. Reference the
paragraph above for information on how to compensate for the lead wire resistance
that is internal to the EX1629.
Quarter-Bridge Strain Measurement/Full-Bridge Strain Measurement
The key concepts regarding the conditions on the strain measurement accuracy tables are:
The stability effects of the excitation source are already captured in the listed accuracies. It is
thus not necessary to combine the two to create a total system accuracy. The listed strain
accuracies are already for the entire EX1629 measurement system.
The accuracies do assume that the excitation voltage is measured and used in the EU
conversion before the initiation of strain measurements. This eliminates its set point accuracy
from being an error source.
The restriction of 30 days, ±5 °C is used throughout the conditions. Essentially the intention is
to describe a strain test setup that is initiated with a self-calibration, excitation voltage
measurement, and unstrained voltage measurement. From that point, continuous strain
measurements are considered to be taken over ambient conditions of 30 days, ±5 ºC.
Содержание EX1629
Страница 310: ...VTI Instruments Corp 310 EX1629 Command Set...
Страница 342: ...VTI Instruments Corp 342 EX1629 Onboard Memory...