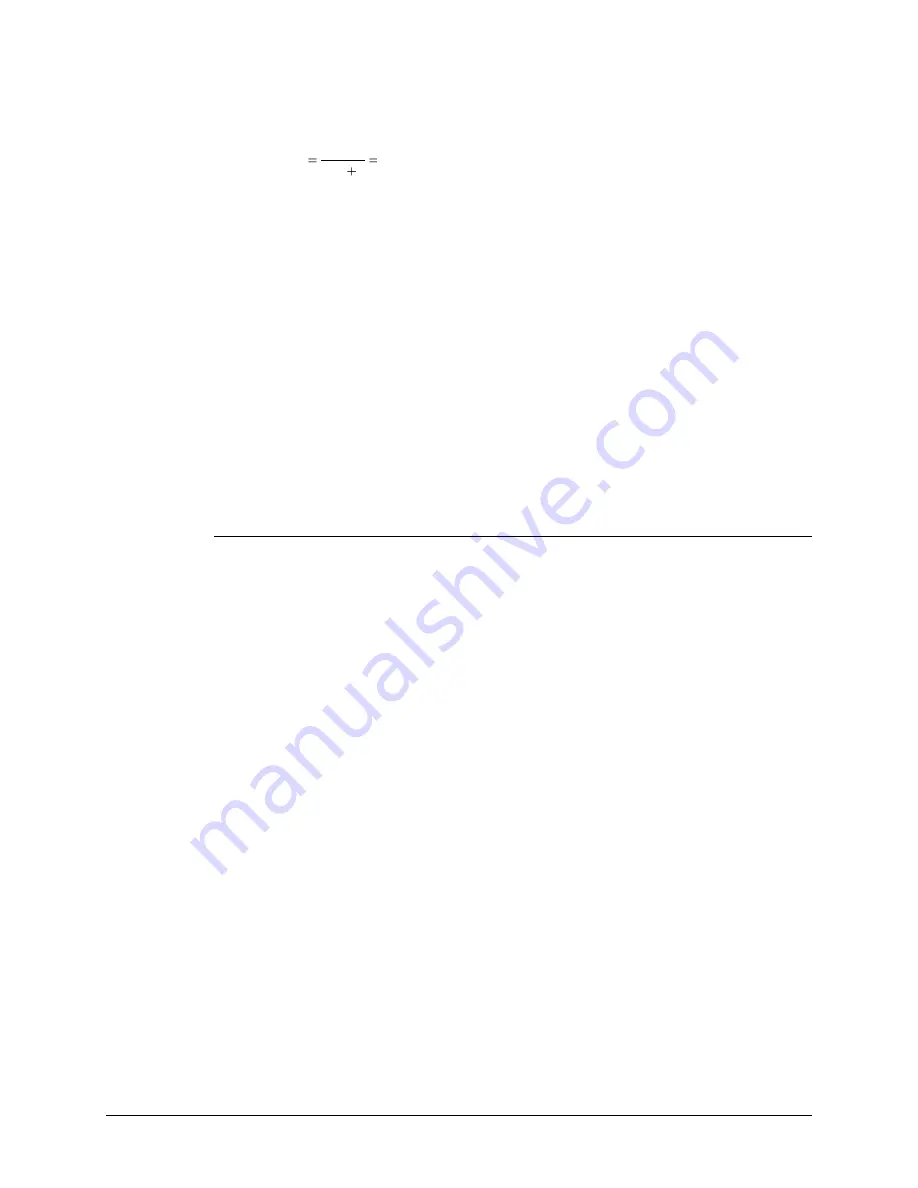
VTI Instruments Corp.
26
EX1629 Introduction
For example, lead wire resistance of 1 Ω on a 350 Ω gage causes a desensitization error of:
02849
.
0
1
350
1
error
Because it is a gain error, it is easily compensated if the desensitization can be measured or
calculated prior to the commencement of the strain testing. Depending on the abilities of the data
collection mechanism, the compensation can be done as a post-acquisition mathematical
operation, through manipulation of the gage factor in the calculation equation, or through internal
gain compensation based on an inputted lead wire value.
But, regardless of how the compensation is conducted, the first step in the process is to determine
the value of the desensitization for each measurement channel in the system. Depending on the
consistency of the test setup and the accuracy desired, there are two common ways of determining
the error. The most basic way is simply to measure the resistance value of the lead wire with a
DMM during the gage installation process. However, for a large channel count application with
little consistency in the distance between the sensors and the measuring instrument, this would
require the manual measurement and tracking of hundreds of wires, an obviously arduous task.
This compensation can be calculated theoretically if the resistance of the connection wire is
characterized or can be inferred through the shunt calibration process, or by calling the
vtex1629_set_lead_wire_resistance
and
vtex1629_set_half_bridge_lead_wire_desensitization
functions. Please reference the
subsection in Section 1 for information on how
to compensate for the lead wire resistance that is internal to the EX1629.
Allow for thermal stabilization of the bridge
Compared to other sensor measurements, bridge measurements inherently involve relatively high
amounts of power dissipation. Power is dissipated in the excitation source, the completion resistor,
as well as the gage itself. The power dissipation is not so much a problem as a change in power.
Specifically, when the excitation source value is changed, the amount of power being dissipated in
the various bridge elements changes. A power dissipation change then leads to a temperature
change through the thermal impedance of each element. Temperature change then ultimately
results in performance characteristic drift. Since bridge power is directly related to the excitation
current amount, this issue is worsened by increasing the excitation voltage or decreasing the
bridge resistance.
To achieve maximum performance, it is best to allow the system elements to thermally stabilize
once the bridge configuration has been programmed and the excitation source set and enabled.
This time will be largely driven by the characteristics of the strain gage chosen for the application,
and should be determined empirically. Only after this time should the excitation and unstrained
voltage measurements be conducted.
Содержание EX1629
Страница 310: ...VTI Instruments Corp 310 EX1629 Command Set...
Страница 342: ...VTI Instruments Corp 342 EX1629 Onboard Memory...