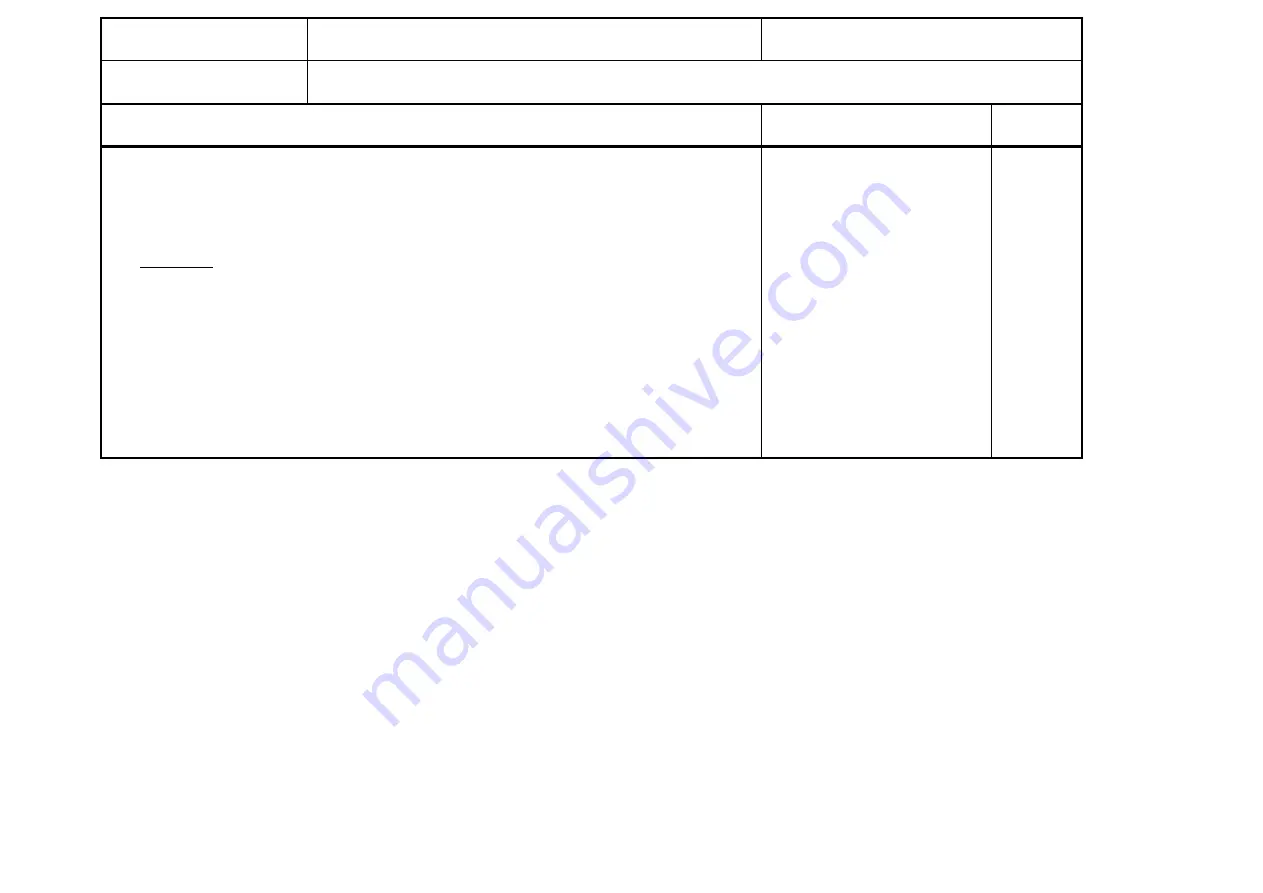
53
TO M-14P MS
TASK CARD No. 201
M.S. ITEM
PROCEDURE: Engine Starting
OPERATIONS AND TECHNICAL REQUIREMENTS
CORRECTIVE ACTIONS
CHECKED
BY
1. Shift the speed governor lever to the LOW PITCH position.
NOTE: At a carburetor inlet air temperature of below 10 °C, open the air heating
shutter at the carburetor inlet.
2. Set the carburetor throttle control lever to the position corresponding to a speed of 28 to
38 % (800 to 1100 r/min).
3. Cut in all the engine instruments.
CAUTION:
DO NOT FILL MORE GASOLINE THAN SPECIFIED, OTHERWISE IT CAN
WASH DOWN OIL FROM THE CYLINDER WALLS AND CAUSE SCORING OF PISTONS,
WHILE ACCUMULATION OF GASOLINE IN LOWER CYLINDERS AND SUCTION PIPES
MAY CAUSE HYDRAULIC SHOCK.
4. Make sure the ignition is switched on, prime the engine mixture collector by the hand
priming pump with 8 to 12 shots in summer and 15 to 20 shots in winter, simultaneously
turning the airscrew manually in its normal direction.
5. Allow gasoline vapors evaporate, for 1 to 2 min in summer and 3 to 5 min in winter.
6. Operate the hand pump to build up gasoline pressure of 0.2 to 0.5 kgf/cm before the
carburetor inlet.
Содержание M-14P
Страница 6: ...19 Engine M 14P Front View Figure 1...
Страница 7: ...20 Engine M 14P Rear View Figure 2...
Страница 27: ...40 Arrangement of Airborne Tools in Case Figure 1...
Страница 39: ......
Страница 44: ...57 Engine M 14P Test Run Chart Figure 201...
Страница 67: ...80...
Страница 163: ...176 Crankshaft Thrust Ball Bearing Front Cover Figure 1 Intermediate Crankcase Figure 2...
Страница 166: ...179 Intermediate Grankcase Front Portion Figure 3 Intermediate Crankcase Rear Portion Figure 4...
Страница 173: ...186 Front view Cylinder Figure 1 Rear view...
Страница 174: ...187 1 Inlet Valve 2 Outer Spring 3 Inner Spring 4 Split Retainer 5 Valve Plate Inlet Valve Figure 2...
Страница 178: ...191 Intake Pipe of Cylinders Nos 4 5 and 6 Figure 4 Piston Piston Rings and Piston Pin with Plugs Figure 5...
Страница 180: ...193 Timing Mechanism Schematic Diagram Figure 6 Cam Plate Figure 7...
Страница 189: ...Blower Longitudinal Section View Figure 1...
Страница 191: ...Rear view Mixture Collector Figure 2 Diffuser Figure 3...
Страница 194: ...1 Plate 2 Spring 3 Plate 4 Gear 5 Accessory Drive Shaft Blower Coupling Figure 4...
Страница 204: ...Oil Sump Figure 4...
Страница 216: ...Engine M 14P Gear Train Figure 1...
Страница 247: ...Carburetor AK 14P Operation Diagram Figure 1...
Страница 249: ......
Страница 267: ...OPERATIONS AND TECHNICAL REQUIREMENTS CORRECTIVE ACTIONS CH ECKED BY Carburetor AK 14P Right Side View Figure 201...
Страница 273: ...Carburetor Altitude Control Needle Position Versus Barometric Pressure Barometric Graph Figure 203...
Страница 274: ......
Страница 282: ......
Страница 283: ......
Страница 288: ...T t en 0 CO 0 T K D fi h0 Ol f 01 3 0 F4...
Страница 293: ......
Страница 309: ...SPARK PLUG SD 49SMM MAINTENANCE PRACTICES 1 LIST OF TASK CARDS Title Task Card Uo Removal 201 Installation 202...
Страница 344: ...Generator Electrical Connection Diagram Commutator Side View Figure 3 1 Main Pole 2 Interpole...
Страница 355: ......
Страница 358: ......