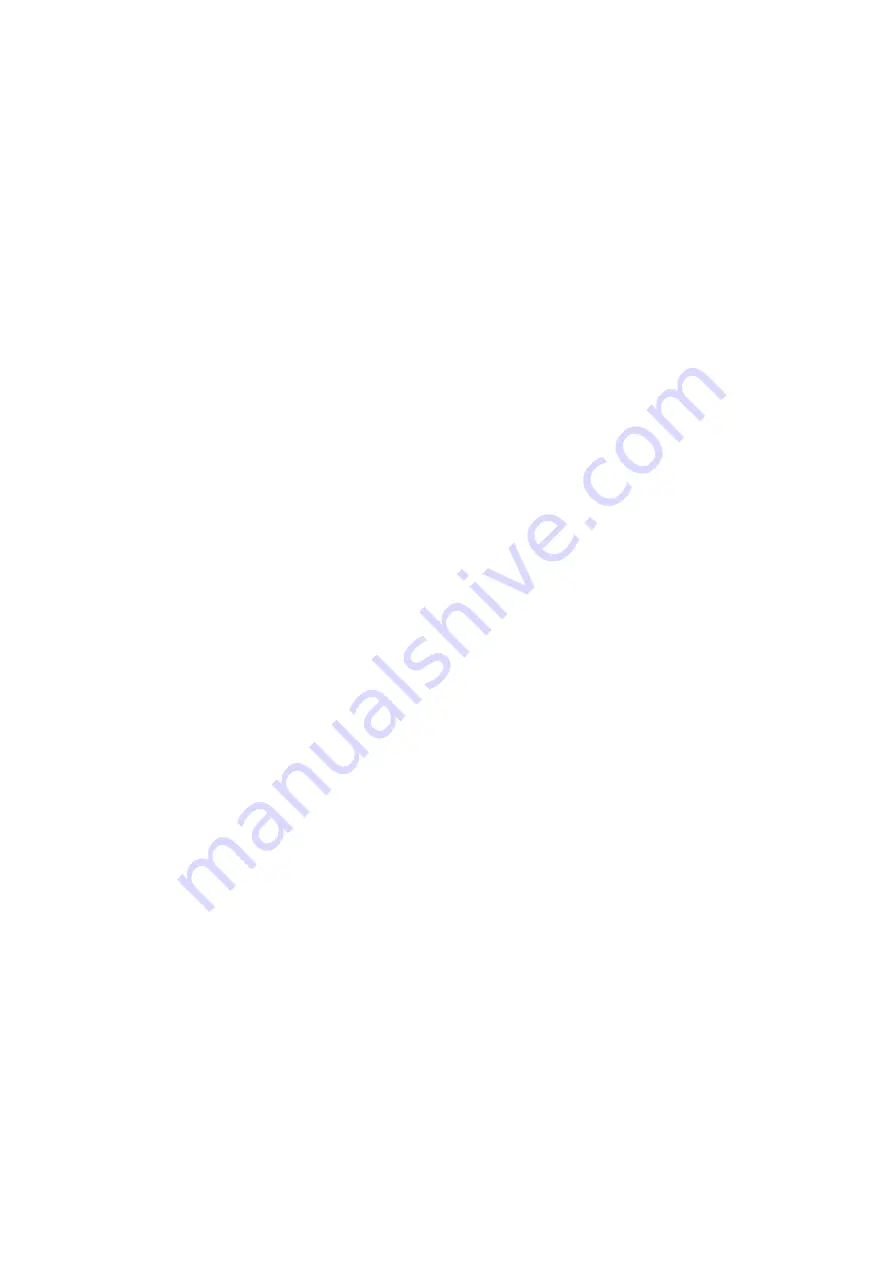
181
Front counterweight (33) is immovably fixed, on the web of the crankshaft front section by three pins (34).
The web and crankpin have a space closed at the front with steel plug (9) and at the rear by the crankpin
plane. The space is connected with the shaft front end by a drilled passage. The upper part of the web is provided
with a threaded hole receiving jet (12) for squirting oil to lubricate the cylinders and pistons. The jet is safetied with
lock (13).
The crankshaft crankpin is externally nitrated to increase wear resistance. The orank-pin has a radial hole
to supply oil from the crankshaft rear to its front section and two radial holes to feed oil to the master connecting rod
bushing which are at an angle of 60° from the axis of symmetry in the direction of crankshaft rotation. Two copper
pipes are inserted into these holes and flared to preclude dropping out. The pipe ends project inside the crankpin
and serve as oil filter operating aa a centrifuge during rotation of the crankshaft.
Crankshaft rear section (16) has a web and a main journal. The upper part of the web has a split lug
embracing the crankpin and a hole for coupling bolt (14). The coupling bolt tightening the lug by nut (17)» rigidly
interconnects the front and rear sections of the crankshaft.
The web lower part has two holes with bushings (22) pressed in them. The bushings receive pins (26)
whereby pendulum counterweight (29) with four bushings (27) pressed in it is suspended from the web. The pins
are kept against axial displacement by collars and strip (24) secured by two bolts (23).
Rear roller bearing (21) secured with nut (20) is press-fitted to the main journal of the crankshaft.
The surfaces of the front and rear roller bearing inner races contacting the crankcase journals are brass
plated to preclude cold hardening.
The rear main journal has a through hole with internal splines whereby the crankshaft is connected through
a coupling with the accessory drive shaft. The journal hole has press-fitted plug (15) copper plated on the outside
diameter surface; the accessory drive shaft splined coupling is aligned inside the plug. The plug is kept against dis-
placement with a pin. The web has a passage interconnecting the spaces of the main journal and crankpin.
The crankshaft is balanced by selecting weight of two plugs (35) threaded in the front counterweight. The
plugs are made of steel or aluminium, depending on balancing requirements.
The rear counterweight is a segment with a through slot at the middle for passing the crankshaft web and
two holes for the bushings. The slot inner surface is copper plated to preclude cold hardening.
2.4. CONMECTING ROD ASSEMBLY
Connecting rod assembly (Ref. Fig. 6) of the M-14P engine comprises one master connecting rod (1) and
eight articulated connecting rods (5) which are hinged to the master rod by steel pins (7).
The master connecting rod is arranged in cylinder No. 4.
The connecting rods are forged of nickel-chrome steel and heat-treated. The connecting rod surfaces are
polished.
The master and articulated connecting rods comprise small and big ends interconnected by an I-section
stem. Pressed in the master connecting rod big end is steel bushing (9) potted with lead bronze and locked by two
set screws (8). A thin layer of lead-tin plating is applied to the inner friction surface of the bushing after machining.
Bushings (2), (6) and (4) made of bronze band are press-fitted in the small end of the master connecting rod and in
the ends of all articulated connecting rods, respectively. The bushings are compacted by broaching and their edges
are flared.
Two through holes for feeding oil, squirted during operation, to bushing friction surfaces are made in the
lower parts of the small ends of all the connecting rods.
The cross section of the master connecting rod decreases from the small end to the big one, while the
articulated rods have equal cross section throughout the length.
The master connecting rod big end has two side plates with eight brass plated holes each, to receive pins
of the articulated connecting rods. The pins carry eight articulated connecting rods. Oil is fed to them under
pressure from the crankpin through the drillings in the rear side plate and pins.
The articulated connecting rod pins are made of steel and cemented for surface hardness. Each pin has a
through cylindrical hole with a spool-shaped aluminium alloy plug pressed in. The space between the plug and inner
surface of the pin serves to pass oil to the articulated connecting rod bushings.
The pin outer surface is stepped.
The front part diameter exceeds that of the other portion of the pin. The steps of the pin outer surface
ensure equal-interference fit in both side plates of the master connecting rod. The pin middle part surface is a
working portion for the articulated connecting rod bushing; the outer portions are support necks for the pin in the
master connecting rod.
Two diametrically opposed flats are made on the pin working surface. Oil is fed to them through the holes
drilled in the pin wall from the pin inner space to its friction surface. For uniform distribution of oil over the pin
surface, one hole is located closer to the front end and the other hole closer to the rear end. The rear cylindrical part
of the pin has an inclined through hole connecting the pin inner space with the oil supply hole in the master
connecting rod side plate.
Содержание M-14P
Страница 6: ...19 Engine M 14P Front View Figure 1...
Страница 7: ...20 Engine M 14P Rear View Figure 2...
Страница 27: ...40 Arrangement of Airborne Tools in Case Figure 1...
Страница 39: ......
Страница 44: ...57 Engine M 14P Test Run Chart Figure 201...
Страница 67: ...80...
Страница 163: ...176 Crankshaft Thrust Ball Bearing Front Cover Figure 1 Intermediate Crankcase Figure 2...
Страница 166: ...179 Intermediate Grankcase Front Portion Figure 3 Intermediate Crankcase Rear Portion Figure 4...
Страница 173: ...186 Front view Cylinder Figure 1 Rear view...
Страница 174: ...187 1 Inlet Valve 2 Outer Spring 3 Inner Spring 4 Split Retainer 5 Valve Plate Inlet Valve Figure 2...
Страница 178: ...191 Intake Pipe of Cylinders Nos 4 5 and 6 Figure 4 Piston Piston Rings and Piston Pin with Plugs Figure 5...
Страница 180: ...193 Timing Mechanism Schematic Diagram Figure 6 Cam Plate Figure 7...
Страница 189: ...Blower Longitudinal Section View Figure 1...
Страница 191: ...Rear view Mixture Collector Figure 2 Diffuser Figure 3...
Страница 194: ...1 Plate 2 Spring 3 Plate 4 Gear 5 Accessory Drive Shaft Blower Coupling Figure 4...
Страница 204: ...Oil Sump Figure 4...
Страница 216: ...Engine M 14P Gear Train Figure 1...
Страница 247: ...Carburetor AK 14P Operation Diagram Figure 1...
Страница 249: ......
Страница 267: ...OPERATIONS AND TECHNICAL REQUIREMENTS CORRECTIVE ACTIONS CH ECKED BY Carburetor AK 14P Right Side View Figure 201...
Страница 273: ...Carburetor Altitude Control Needle Position Versus Barometric Pressure Barometric Graph Figure 203...
Страница 274: ......
Страница 282: ......
Страница 283: ......
Страница 288: ...T t en 0 CO 0 T K D fi h0 Ol f 01 3 0 F4...
Страница 293: ......
Страница 309: ...SPARK PLUG SD 49SMM MAINTENANCE PRACTICES 1 LIST OF TASK CARDS Title Task Card Uo Removal 201 Installation 202...
Страница 344: ...Generator Electrical Connection Diagram Commutator Side View Figure 3 1 Main Pole 2 Interpole...
Страница 355: ......
Страница 358: ......