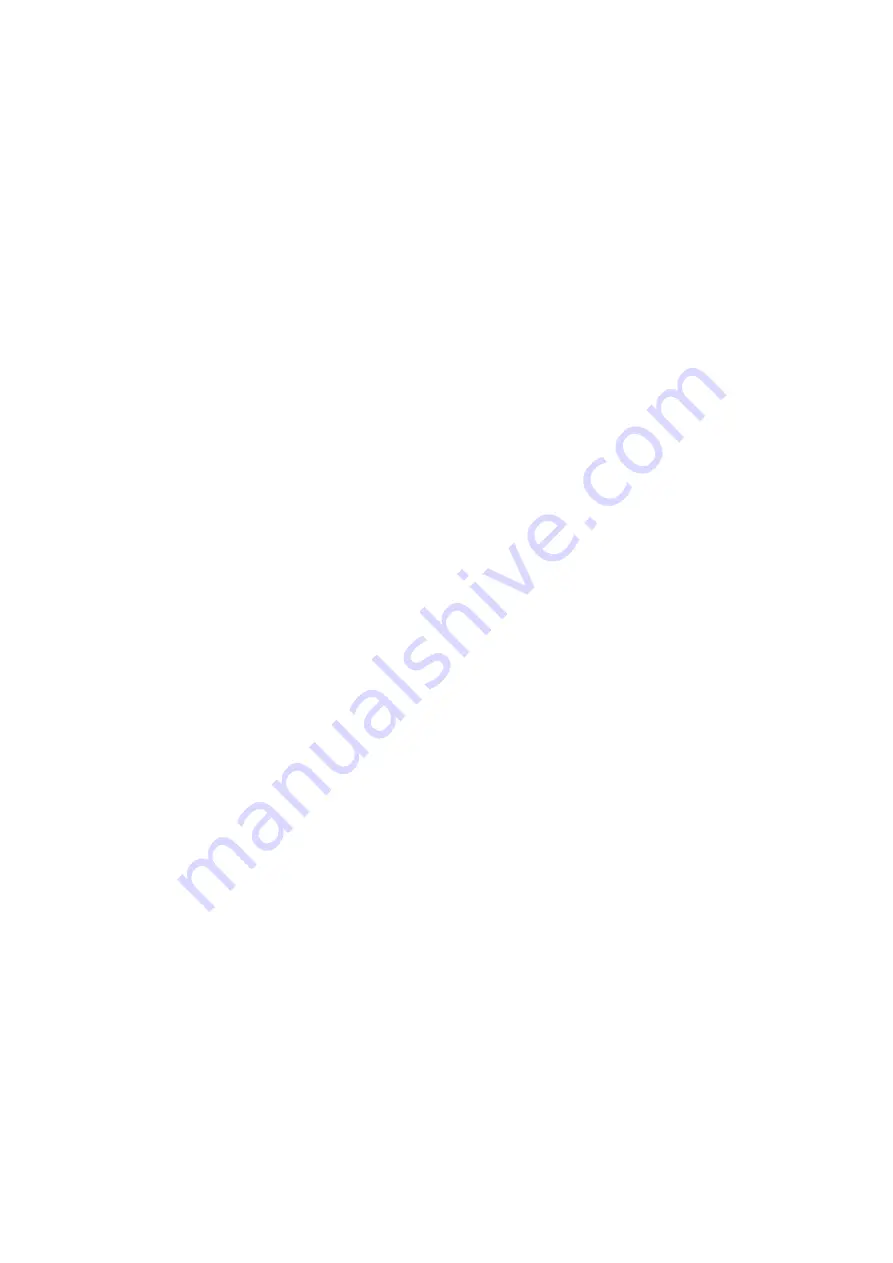
168
Gearbox housing (10) (Ref. Pig. 2) is adapted to accommodate the gearbox parts and is cast of
magnesium alloy ML-5. It is a truncated cone attached to the engine intermediate crankcase with its rear
flange by means of studs driven into the intermediate crankcase front part.
The gearbox housing takes up load created by the airscrew and transmits it to the crankcase
attachment units and engine frame.
The front part of the housing has a hub with an outer flange with fourteen bosses receiving thirteen
threaded studs and three milled flats for the thrust bearing front cover puller. Nine studs are used to secure
cover (6) of radial ball bearing (8) of airscrew shaft (1) and four studs attach the inner ring of the engine
cowling louvers.
The lower boss has a through inclined hole transforming into an open passage for draining oil from
the cover space of the airscrew shaft radial ball bearing.
Bushing (7) for mounting the airacrew shaft ball bearing is press-fit in the front bore of the hub.
Mounted on the front flange of the housing is ball bearing cover (6) whose aligning collar doubles as a front
stop for the ball bearing.
Steel cover (6) has a flange with nine holes for installing on the housing studs and an annular recess
on the flange side. Disposed between the ball bearing and the cover aligning collar is steel oil baffle (4). A
paronite gasket is arranged between the cover and the housing. Sealing rubber collar (3) is installed in the
central bore of cover (6).
Steel bushing (11) is pressed in a hole turned in the housing hub concentrically with the radial ball
bearing seat. The inner surface of the bushing carries oil sealing rings (32). The bushing is fixed by set screw
(27) driven into the gearbox housing hub. The screw is safetied with a plate lock.
Driven into the gearbox housing hub threaded hole is a jet for lubricating the radial ball bearing of the
airscrew shaft.
Made in the middle inner part of the housing are bores and a flange with bosses for mounting and
securing hub (12) of the gearbox sun gear. Screwed into each boss is a steel threaded bushing with left-hand
thread. Hub (12) is secured to the housing flange by bolts (13) driven in the threaded bushings.
The housing lower part has a flange with a central hole and four threaded holes receiving threaded
bushings for mounting the bellows. The bellows is used to drain oil from the gearbox housing through a
circular central hole of the flange to the oil sump.
A boss with a flange and four studs for attachment of the airscrew speed governor is made on the
outside upper RH part of the gearbox housing. A through hole is made in the flange to pass the shank of the
speed governor drive shaft; an inclined lateral hole is intended to drain'oil from the speed governor.
Provided in the upper LH part of the gearbox housing is a boss with a machined flange having a
through hole and two studs for attachment of auxiliary blanking cover (24) of the gearbox breather.
The housing has two bosses with holes serving as passages to supply oil from the engine main
gallery to the speed governor and from the governor to the airscrew.
These passages interconnect two holes on the speed governor mounting flange and two respective
holes in the oil sealing ring bushing.
The passage supplying oil from the engine main gallery to the speed governor features a boss with a
threaded hole receiving steel adapter bushing (22), fixed against turning with a retainer. Oil mesh filter (23) is
driven into the adapter bushing. The filter comprises two parts: a casing and a mesh brazed to it. A fiber
gasket is placed between the filter casing and the adapter bushing end face. The filter is safetied with a
spring lock.The passage for supplying oil to the airscrew speed governor is connected to an additional
passage drilled in parallel with the gearbox housing center line and further through the oil transfer bushing to
the middle part of the crankcase for lubricating the valve mechanisms of the cylinder head cases.
Содержание M-14P
Страница 6: ...19 Engine M 14P Front View Figure 1...
Страница 7: ...20 Engine M 14P Rear View Figure 2...
Страница 27: ...40 Arrangement of Airborne Tools in Case Figure 1...
Страница 39: ......
Страница 44: ...57 Engine M 14P Test Run Chart Figure 201...
Страница 67: ...80...
Страница 163: ...176 Crankshaft Thrust Ball Bearing Front Cover Figure 1 Intermediate Crankcase Figure 2...
Страница 166: ...179 Intermediate Grankcase Front Portion Figure 3 Intermediate Crankcase Rear Portion Figure 4...
Страница 173: ...186 Front view Cylinder Figure 1 Rear view...
Страница 174: ...187 1 Inlet Valve 2 Outer Spring 3 Inner Spring 4 Split Retainer 5 Valve Plate Inlet Valve Figure 2...
Страница 178: ...191 Intake Pipe of Cylinders Nos 4 5 and 6 Figure 4 Piston Piston Rings and Piston Pin with Plugs Figure 5...
Страница 180: ...193 Timing Mechanism Schematic Diagram Figure 6 Cam Plate Figure 7...
Страница 189: ...Blower Longitudinal Section View Figure 1...
Страница 191: ...Rear view Mixture Collector Figure 2 Diffuser Figure 3...
Страница 194: ...1 Plate 2 Spring 3 Plate 4 Gear 5 Accessory Drive Shaft Blower Coupling Figure 4...
Страница 204: ...Oil Sump Figure 4...
Страница 216: ...Engine M 14P Gear Train Figure 1...
Страница 247: ...Carburetor AK 14P Operation Diagram Figure 1...
Страница 249: ......
Страница 267: ...OPERATIONS AND TECHNICAL REQUIREMENTS CORRECTIVE ACTIONS CH ECKED BY Carburetor AK 14P Right Side View Figure 201...
Страница 273: ...Carburetor Altitude Control Needle Position Versus Barometric Pressure Barometric Graph Figure 203...
Страница 274: ......
Страница 282: ......
Страница 283: ......
Страница 288: ...T t en 0 CO 0 T K D fi h0 Ol f 01 3 0 F4...
Страница 293: ......
Страница 309: ...SPARK PLUG SD 49SMM MAINTENANCE PRACTICES 1 LIST OF TASK CARDS Title Task Card Uo Removal 201 Installation 202...
Страница 344: ...Generator Electrical Connection Diagram Commutator Side View Figure 3 1 Main Pole 2 Interpole...
Страница 355: ......
Страница 358: ......