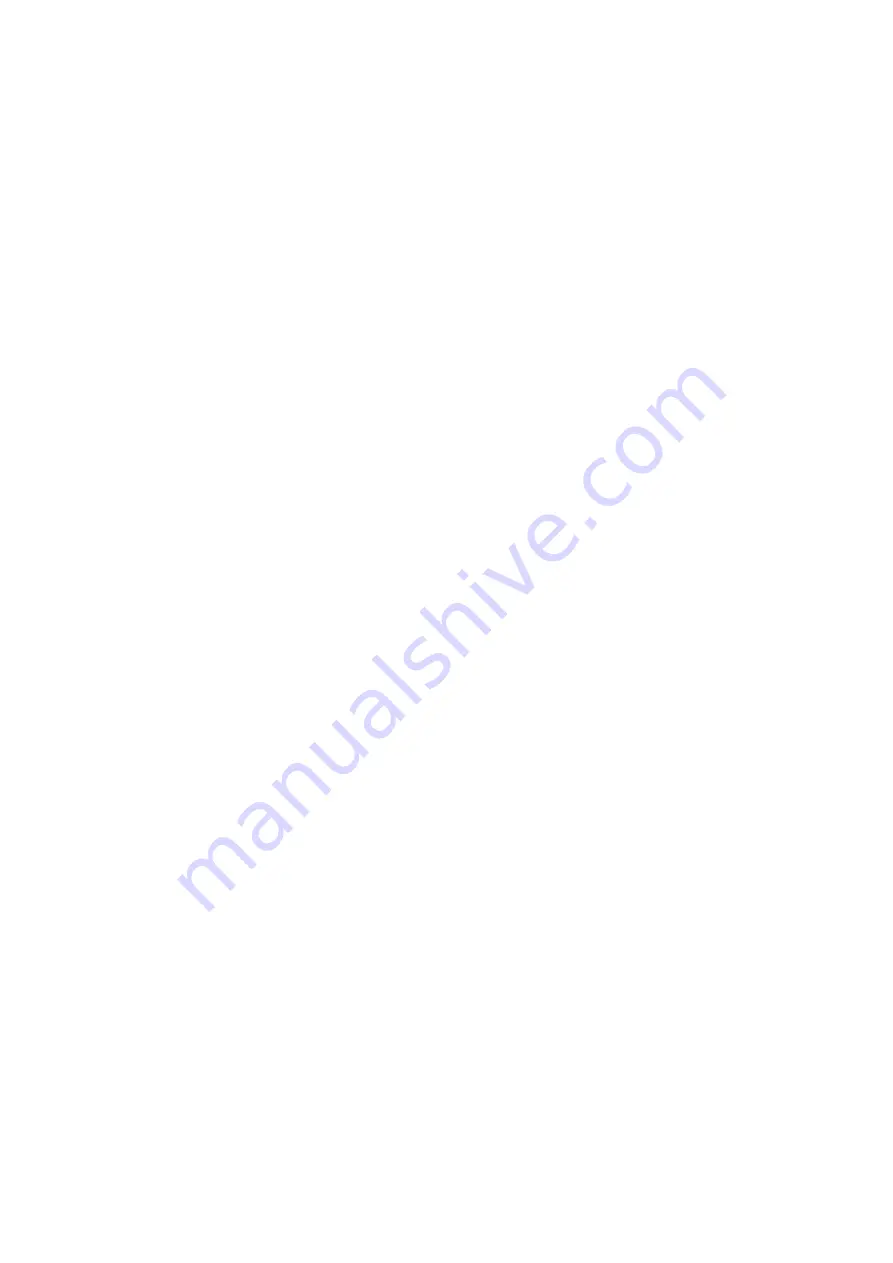
184
CYLINDER ASSEMBLY - DESCRIPTION AND OPERATION
1. GENERAL
The engine cylinder assembly comprises cylinders with valve mechanisms, pistons, timing
mechanism parts, intake pipes and deflectors.
The engine cylinder with its bottom forms a chamber where fuel-air mixture is combusted and thermal
energy is converted into mechanical work.
To ensure well-timed opening and closing of inlet and exhaust valves according to the timing chart,
the timing mechanism is used.
Normal operation of the engine is achieved at uniform cooling of its cylinders. The engine is cooled
by on-coming air stream created by the airscrew.
2. CONSTRUCTION
2.1. CYLINDER WITH VALVE MECHANISM
Engine cylinder (Ref. Pig. 1) comprises two main parts: a steel machined sleeve and an aluminium
alloy head screwed on it when hot. The head lower collar has press-fitted steel shroud ring.
The cylinder sleeve is made of an alloyed steel forging, heat-treated, its internal surface is nitrated,
ground and honed. The sleeve has cooling outside ribs and a flange with holes for securing the cylinder to the
intermediate crankcase. The cylindrical part below the flange (skirt) ensures alignment of the sleeve relative
to the crankcase port.
The sleeve top is provided with a thrust thread having a sealing band for coupling with the cylinder
head.
The cylinder head is cast of aluminium alloy integrally with two valve cases. The outer surface of the
head is provided with vertical and horizontal ribs cast integrally with the head. The cylinder head inner space
is machined, has a thrust thread for mating with the sleeve and defines together with the piston the dome
combustion chamber.
Seats for inlet and exhaust valves are pressed at the inner aide of the cylinder head. The upper
bands of the seat are flared in the head.
The inlet valve seat land is machined at an an^le of 30°, the exhaust valve land at an angle of 45°
relative to the seat lower end face plane.
The valve case bottoms located on the outer top side of the sleeve have drilled, holes where bronze
guide bushings of the valves are press-fitted. The bushings are arranged at an angle of 75° symmetrically to
the axis of the cylinder. Holes for valve rocker axles with outer recesses for sealing washers are machined in
the thickened portion of the valve case side walls. Connections for attachment of rod covers are driven into
the front bottom part of the valve cases; air deflector attachment studs are driven in the rear part.
The case front'portions have lugs whose holes receive flared axles suspending stops of tensioning
wing nuts. A cover attachment screw is driven into a boss provided at the rear part of the cases. A ring cable
run in the grooves of the valve case cover is fitted to the screw neck. The other side of the cable is fitted to
the tensioning wing nut and on being tightened with a special wrench, tightly presses the cover to the valve
case.
The valve cover is sealed with a rubber ring.
Located at the rear of the head are: at the LH side - an inlet branch pipe with a steel copper-plated
connection screwed into it, at the RH side - an exhaust branch pipe with a bronze ring screwed on it. The
intake pipe (Ref. Fig. 4) is attached to the LH branch pipe and the exhaust manifold branch pipe is connected
to the RH branch pipe.
Three bronze bushings with internal thread are driven into the front and rear parts of the cylinder
head threaded holes. Two bushings located symmetrically to the cylinder axis serve for receiving the front
and rear spark plugs. The third bushing driven in a boss located at the front under the inlet valve case serves
for driving in the starting system valve. Located under the front spark plug hole is the louver mounting bracket
attachment stud.
Each cylinder has one inlet valve (1) (Ref. Pig. 2) and one exhaust valve (1) (Ref. Pig. 3) made of
heat-resistant steel forgings.
The valves admit mixture to the cylinders and release gases from them during inlet and exhaust
strokes and seal the cylinders during compression and expansion strokes.
The inlet valve (Ref. Pig. 2) is made of steel Ch12M; its mushroom-type head on the side opposite to
Содержание M-14P
Страница 6: ...19 Engine M 14P Front View Figure 1...
Страница 7: ...20 Engine M 14P Rear View Figure 2...
Страница 27: ...40 Arrangement of Airborne Tools in Case Figure 1...
Страница 39: ......
Страница 44: ...57 Engine M 14P Test Run Chart Figure 201...
Страница 67: ...80...
Страница 163: ...176 Crankshaft Thrust Ball Bearing Front Cover Figure 1 Intermediate Crankcase Figure 2...
Страница 166: ...179 Intermediate Grankcase Front Portion Figure 3 Intermediate Crankcase Rear Portion Figure 4...
Страница 173: ...186 Front view Cylinder Figure 1 Rear view...
Страница 174: ...187 1 Inlet Valve 2 Outer Spring 3 Inner Spring 4 Split Retainer 5 Valve Plate Inlet Valve Figure 2...
Страница 178: ...191 Intake Pipe of Cylinders Nos 4 5 and 6 Figure 4 Piston Piston Rings and Piston Pin with Plugs Figure 5...
Страница 180: ...193 Timing Mechanism Schematic Diagram Figure 6 Cam Plate Figure 7...
Страница 189: ...Blower Longitudinal Section View Figure 1...
Страница 191: ...Rear view Mixture Collector Figure 2 Diffuser Figure 3...
Страница 194: ...1 Plate 2 Spring 3 Plate 4 Gear 5 Accessory Drive Shaft Blower Coupling Figure 4...
Страница 204: ...Oil Sump Figure 4...
Страница 216: ...Engine M 14P Gear Train Figure 1...
Страница 247: ...Carburetor AK 14P Operation Diagram Figure 1...
Страница 249: ......
Страница 267: ...OPERATIONS AND TECHNICAL REQUIREMENTS CORRECTIVE ACTIONS CH ECKED BY Carburetor AK 14P Right Side View Figure 201...
Страница 273: ...Carburetor Altitude Control Needle Position Versus Barometric Pressure Barometric Graph Figure 203...
Страница 274: ......
Страница 282: ......
Страница 283: ......
Страница 288: ...T t en 0 CO 0 T K D fi h0 Ol f 01 3 0 F4...
Страница 293: ......
Страница 309: ...SPARK PLUG SD 49SMM MAINTENANCE PRACTICES 1 LIST OF TASK CARDS Title Task Card Uo Removal 201 Installation 202...
Страница 344: ...Generator Electrical Connection Diagram Commutator Side View Figure 3 1 Main Pole 2 Interpole...
Страница 355: ......
Страница 358: ......