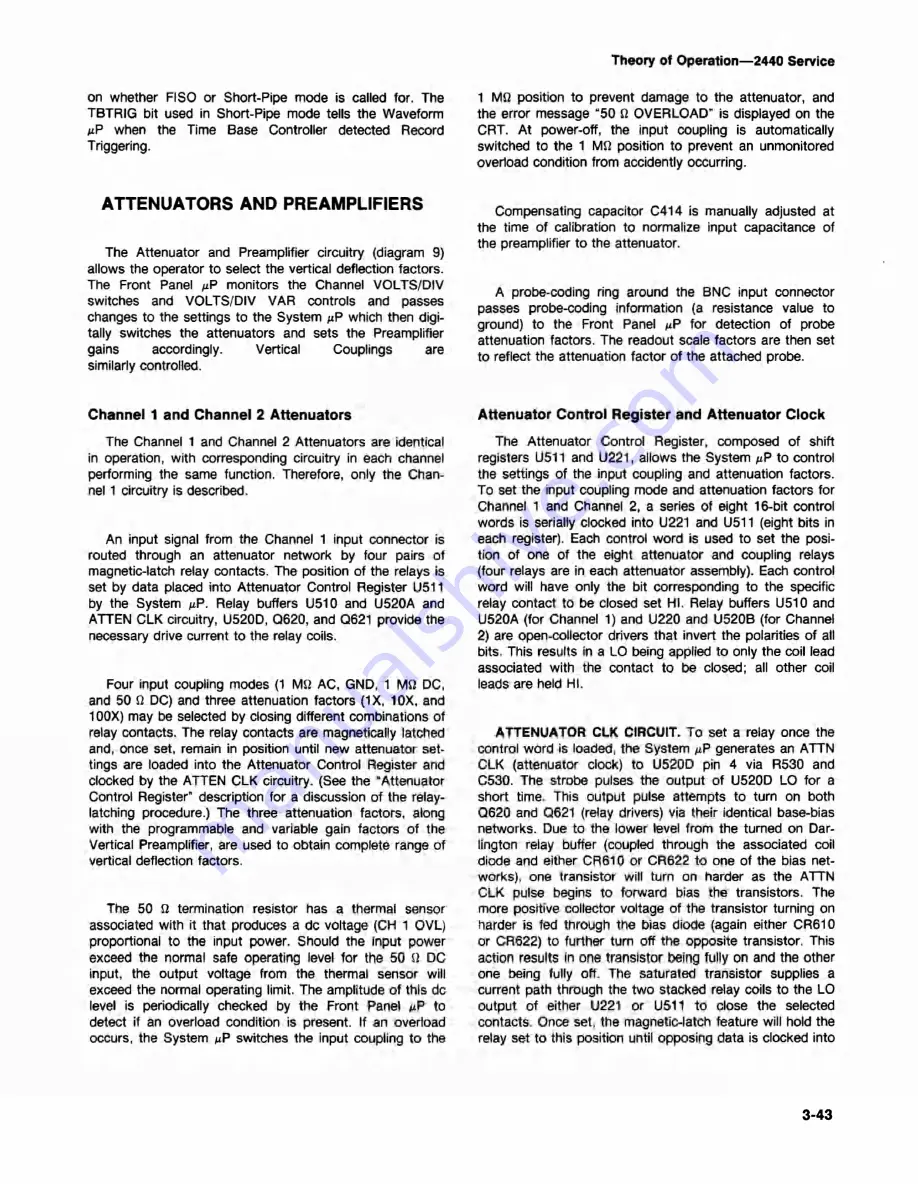
Theory of Operation— 2440 Service
on whether FI SO or Short-Pipe mode is called for. The
TBTRIG bit used in Short-Pipe mode tells the Waveform
fiP
when the Time Base Controller detected Record
Triggering.
ATTENUATORS AND PREAMPLIFIERS
The Attenuator and Preamplifier circuitry (diagram 9)
allows the operator to select the vertical deflection factors.
The Front Panel
/uP
monitors the Channel VOLTS/DIV
switches and VOLTS/DIV VAR controls and passes
changes to the settings to the System
fiP
which then digi
tally switches the attenuators and sets the Preamplifier
gains
accordingly.
Vertical
Couplings
are
similarly controlled.
C h a n n e l 1 a n d C h a n n e l 2 A tte n u a to rs
The Channel 1 and Channel 2 Attenuators are identical
in operation, with corresponding circuitry in each channel
performing the same function. Therefore, only the Chan
nel 1 circuitry is described.
An input signal from the Channel 1 input connector is
routed through an attenuator network by four pairs of
magnetic-latch relay contacts. The position of the relays is
set by data placed into Attenuator Control Register U 511
by the System
u P .
Relay buffers U510 and U520A and
ATTEN CLK circuitry, U520D, 0 6 2 0 , and Q621 provide the
necessary drive current to the relay coils.
Four input coupling modes (1 M$2 AC, GND, 1 Mfi DC,
and 50
Q
DC) and three attenuation factors (1X, 10X, and
100X) may be selected by closing different combinations of
relay contacts. The relay contacts are magnetically latched
and, once set, remain in position until new attenuator set
tings are loaded into the Attenuator Control Register and
clocked by the ATTEN CLK circuitry. (See the “Attenuator
Control Register” description for a discussion of the relay
latching procedure.) The three attenuation factors, along
with the programmable and variable gain factors of the
Vertical Preamplifier, are used to obtain complete range of
vertical deflection factors.
The 50 1) termination resistor has a thermal sensor
associated with it that produces a dc voltage (CH 1 OVL)
proportional to the input power. Should the input power
exceed the normal safe operating level for the 50
(2
DC
input, the output voltage from the thermal sensor will
exceed the normal operating limit. The amplitude of this dc
level is periodically checked by the Front Panel
to
detect if an overload condition is present. If an overload
occurs, the System /uP switches the input coupling to the
1 Mfi position to prevent damage to the attenuator, and
the error message “50
Q
OVERLOAD" is displayed on the
CRT. At power-off, the input coupling is automatically
switched to the 1
position to prevent an unmonitored
overload condition from accidently occurring.
Compensating capacitor C414 is manually adjusted at
the time of calibration to normalize input capacitance of
the preamplifier to the attenuator.
A probe-coding ring around the BNC input connector
passes probe-coding information (a resistance value to
ground) to the Front Panel ^P for detection of probe
attenuation factors. The readout scale factors are then set
to reflect the attenuation factor of the attached probe.
A tte n u a to r C o n tro l R e g is te r a n d A tte n u a to r C lo c k
The Attenuator Control Register, composed of shift
registers U511 and U221, allows the System
i*P
to control
the settings of the input coupling and attenuation factors.
To set the input coupling mode and attenuation factors for
Channel 1 and Channel 2, a series of eight 16-bit control
words is serially clocked into U221 and U 511 (eight bits in
each register). Each control word is used to set the posi
tion of one of the eight attenuator and coupling relays
(four relays are in each attenuator assembly). Each control
word will have only the bit corresponding to the specific
relay contact to be closed set HI. Relay buffers U510 and
U520A (for Channel 1) and U220 and U520B (for Channel
2) are open-collector drivers that invert the polarities of all
bits. This results in a LO being applied to only the coil lead
associated with the contact to be closed; all other coil
leads are held HI.
ATTENUATOR CLK CIRCUIT. To set a relay once the
control word is loaded, the System
n P
generates an ATTN
CLK (attenuator clock) to U520D pin 4 via R530 and
C530. The strobe pulses the output of U520D LO for a
short time. This output pulse attempts to turn on both
Q620 and Q621 (relay drivers) via their identical base-bias
networks. Due to the lower level from the turned on Dar
lington relay buffer (coupled through the associated coil
diode and either CR610 or CR622 to one of the bias net
works), one transistor will turn on harder as the ATTN
CLK pulse begins to forward bias the transistors. The
more positive collector voltage of the transistor turning on
harder is fed through the bias diode (again either CR610
or CR622) to further turn off the opposite transistor. This
action results in one transistor being fully on and the other
one being fully off. The saturated transistor supplies a
current path through the two stacked relay coils to the LO
output of either U221 or U511 to close the selected
contacts. Once set, the magnetic-latch feature will hold the
relay set to this position until opposing data is clocked into
3 -4 3
Содержание 2440
Страница 4: ......
Страница 12: ......
Страница 37: ...Specification 2440 Service Dimensions are in inches mm 4918 39 1 25 Figure 1 1 Dimensional drawing ...
Страница 38: ......
Страница 91: ...Theory of Operation 2440 Service 3 49 Figure 3 5 Simplified CCD architecture ...
Страница 120: ...Theory of Operation 2440 Service Figure 3 10 DC Restorer 3 78 ...
Страница 123: ...Theory of Operation 2440 Service SOURCE ACCEPTOR 4 9 1 7 1 2 3 81 Figure 3 11 GPIB data flow diagram ...
Страница 130: ...Theory of Operation 2440 Service 3 88 ...
Страница 136: ...Theory of Operation 2440 Service Figure 3 15 PWM Regulator and Inverter 3 94 ...
Страница 138: ...Theory of Operation 2440 Service Figure 3 16 PWM switching waveforms 3 96 ...
Страница 208: ......
Страница 322: ......
Страница 419: ......
Страница 423: ...2440 Service Figure 9 4b 2440 Block diagram part 2 6330 27 BLOCK DIAGRAM PART 2 ...
Страница 427: ......
Страница 428: ...2440 Service WAVEFORMS FOR DIAGRAM 1 6 2 8 5 3 2 ...
Страница 429: ......
Страница 432: ...2440 Service WAVEFORMS FOR DIAGRAM 2 BUS ISOLATED 6 6 0 3 4 9 ...
Страница 433: ...WAVEFORMS FOR DIAGRAM 2 ...
Страница 439: ......
Страница 445: ......
Страница 446: ...2440 Service WAVEFORMS FOR DIAGRAM 7 I I f f f NtITOT CHI r K I It MVIHi TRIGGER ON FALLING EDGE OF U832 PIN 8 MORE ...
Страница 450: ...2440 Service WAVEFORMS FOR DIAGRAM 8 6603 27 ...
Страница 455: ...W A V EFO R M S FOR D IAG RAM 11 WAVEFORMS FOR DIAGRAM 11 6603 29 ...
Страница 458: ...WAVEFORMS FOR DIAGRAM 12 ...
Страница 463: ...WAVEFORMS FOR DIAGRAM 14 ...
Страница 468: ...2440 Service W A VE FO R M S FOR DIAG RAM 17 TEST SCOPE TRIGGERED ON 126 6330 46 WAVEFORMS FOR DIAGRAM 17 ...
Страница 471: ... C N i u i t e x r 4 j u J l i 1 i 6 28 5 44 WAVEFORMS FOR DIAGRAM 18 ...
Страница 476: ...WAVEFORMS FOR DIAGRAM 20 ...
Страница 490: ...YES ...
Страница 492: ......
Страница 494: ......
Страница 499: ...YES ...
Страница 501: ......
Страница 502: ...2440 Service FIG 1 C A B IN E T ...
Страница 503: ......
Страница 510: ...2440 Service SISSVHO Z Old ...
Страница 511: ......
Страница 512: ...A12 2440 Service F IG 3 C IR C U IT BOARDS ...
Страница 513: ......
Страница 517: ...10 16 R E V J U L 1993 Replaceable Mechanical Parts ...
Страница 518: ...2440 Service ...
Страница 519: ...FIG 4 L V H V PWR SUPPLY ...
Страница 520: ...FIG 5 ACCESSORIES 2440 Service ...
Страница 521: ......
Страница 523: ......
Страница 529: ......
Страница 530: ......
Страница 531: ......