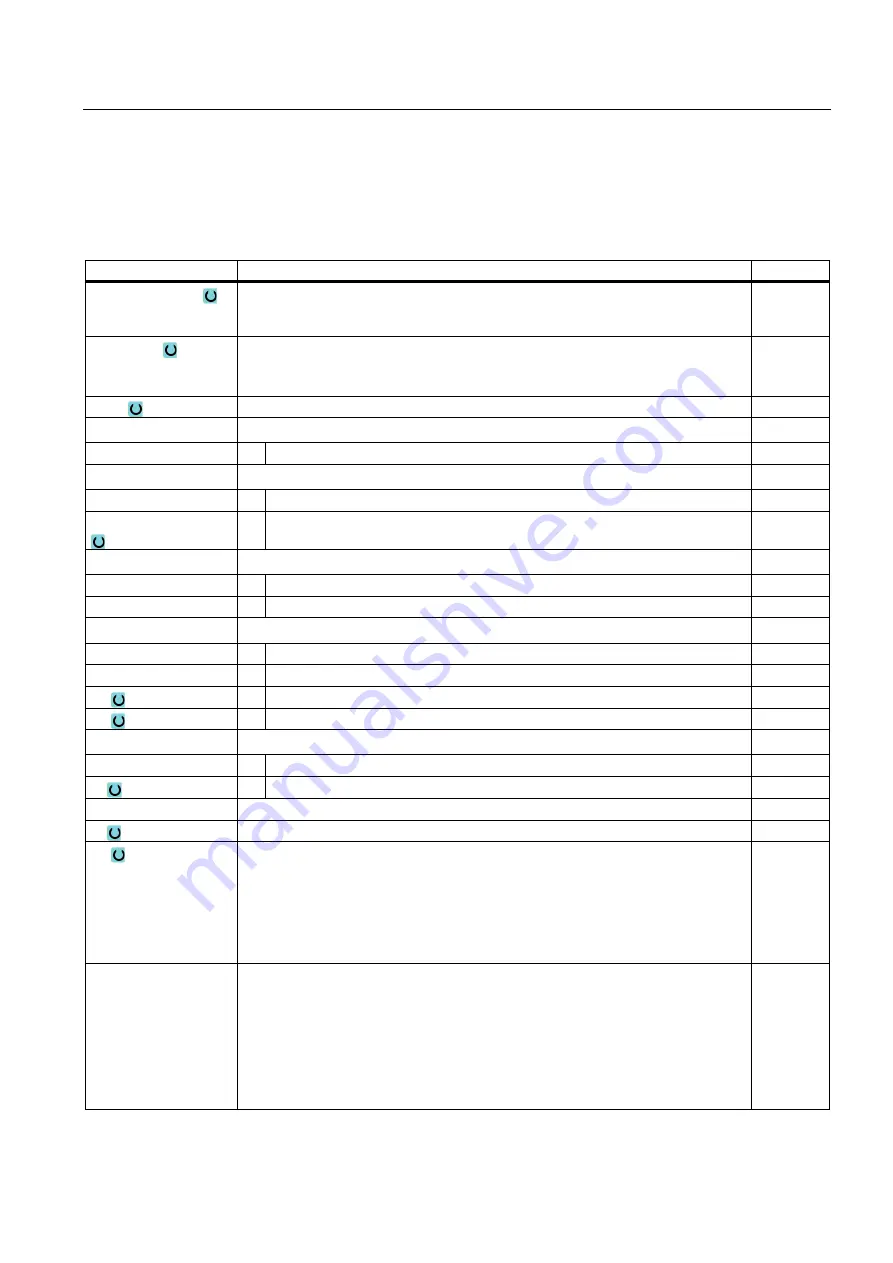
Creating a ShopMill program
7.5 Program header
Milling
Operating Manual, 03/2010, 6FC5398-7CP20-1BA0
227
7.5
Program header
In the program header, set the following parameters, which are effective for the complete
program.
Parameter
Description
Unit
Measurement unit
The dimension unit (mm or inch) set in the program header only refers to the
position data in the actual program. All other data, such as feedrate or tool offsets,
are entered in the dimension unit that you have set for the entire machine.
mm
inch
Work offset
The work offset in which the workpiece zero is saved.
You can also delete the pre-setting of the parameter if you do not want to specify a
work offset.
Blank
Define the form and dimensions of the workpiece
Cylinder
XA
Outer diameter ∅
mm
Polygon
N
Number of edges
SW / L
Width across flats
Edge length
Centered cuboid
W
Width of blank
mm
L
Length of blank
mm
Cuboid
X0
1. Corner point X
mm
Y0
1. Corner point Y
mm
X1
2. Corner point X (abs) or 2nd corner point X referred to X0 (inc)
mm
Y1
2. Corner point Y (abs) or 2nd corner point Y referred to Y0 (inc)
mm
Tube
XA
Outer diameter ∅
mm
XI
Inner diameter ∅ (abs) or wall thickness (inc)
mm
ZA
Initial dimension
mm
ZI
Final dimension (abs) or final dimension in relation to ZA (inc)
mm
PL
Machining plane
G17 (XY)
G18 (ZX)
G19 (YZ)
Note: The plane settings can already be defined. Ask the machine manufacturer in
order that the selection box is available.
Retraction plane RP
Safety clearance SC:
Planes above the workpiece.
During machining the tool travels in rapid traverse from the tool change point to the
return plane (RP) and then to the safety clearance (SC). The machining feedrate is
activated at this level. When the machining operation is finished, the tool travels at
the machining feedrate away from the workpiece to the safety clearance level. It
travels from the safety clearance to the retraction plane and then to the tool change
point in rapid traverse. The retraction plane is entered as an absolute value.
The safety clearance must be entered as an incremental value (without sign).
Содержание SINUMERIK 840D
Страница 6: ...Preface Milling 6 Operating Manual 03 2010 6FC5398 7CP20 1BA0 ...
Страница 50: ...Introduction 1 4 User interface Milling 50 Operating Manual 03 2010 6FC5398 7CP20 1BA0 ...
Страница 134: ...Execution in manual mode 3 7 Default settings for manual mode Milling 134 Operating Manual 03 2010 6FC5398 7CP20 1BA0 ...
Страница 172: ...Machining the workpiece 4 13 Setting for automatic mode Milling 172 Operating Manual 03 2010 6FC5398 7CP20 1BA0 ...
Страница 194: ...Simulating machining 5 9 Displaying simulation alarms Milling 194 Operating Manual 03 2010 6FC5398 7CP20 1BA0 ...
Страница 207: ...Creating G code program 6 8 Selection of the cycles via softkey Milling Operating Manual 03 2010 6FC5398 7CP20 1BA0 207 ...
Страница 208: ...Creating G code program 6 8 Selection of the cycles via softkey Milling 208 Operating Manual 03 2010 6FC5398 7CP20 1BA0 ...
Страница 209: ...Creating G code program 6 8 Selection of the cycles via softkey Milling Operating Manual 03 2010 6FC5398 7CP20 1BA0 209 ...
Страница 216: ...Creating G code program 6 10 Measuring cycle support Milling 216 Operating Manual 03 2010 6FC5398 7CP20 1BA0 ...
Страница 264: ...Creating a ShopMill program 7 17 Example standard machining Milling 264 Operating Manual 03 2010 6FC5398 7CP20 1BA0 ...
Страница 440: ...Multi channel view 9 3 Setting the multi channel view Milling 440 Operating Manual 03 2010 6FC5398 7CP20 1BA0 ...
Страница 460: ...Teaching in a program 11 7 Deleting a block Milling 460 Operating Manual 03 2010 6FC5398 7CP20 1BA0 ...
Страница 600: ...Appendix A 2 Overview Milling 600 Operating Manual 03 2010 6FC5398 7CP20 1BA0 ...
Страница 610: ...Index Milling 610 Operating Manual 03 2010 6FC5398 7CP20 1BA0 ...