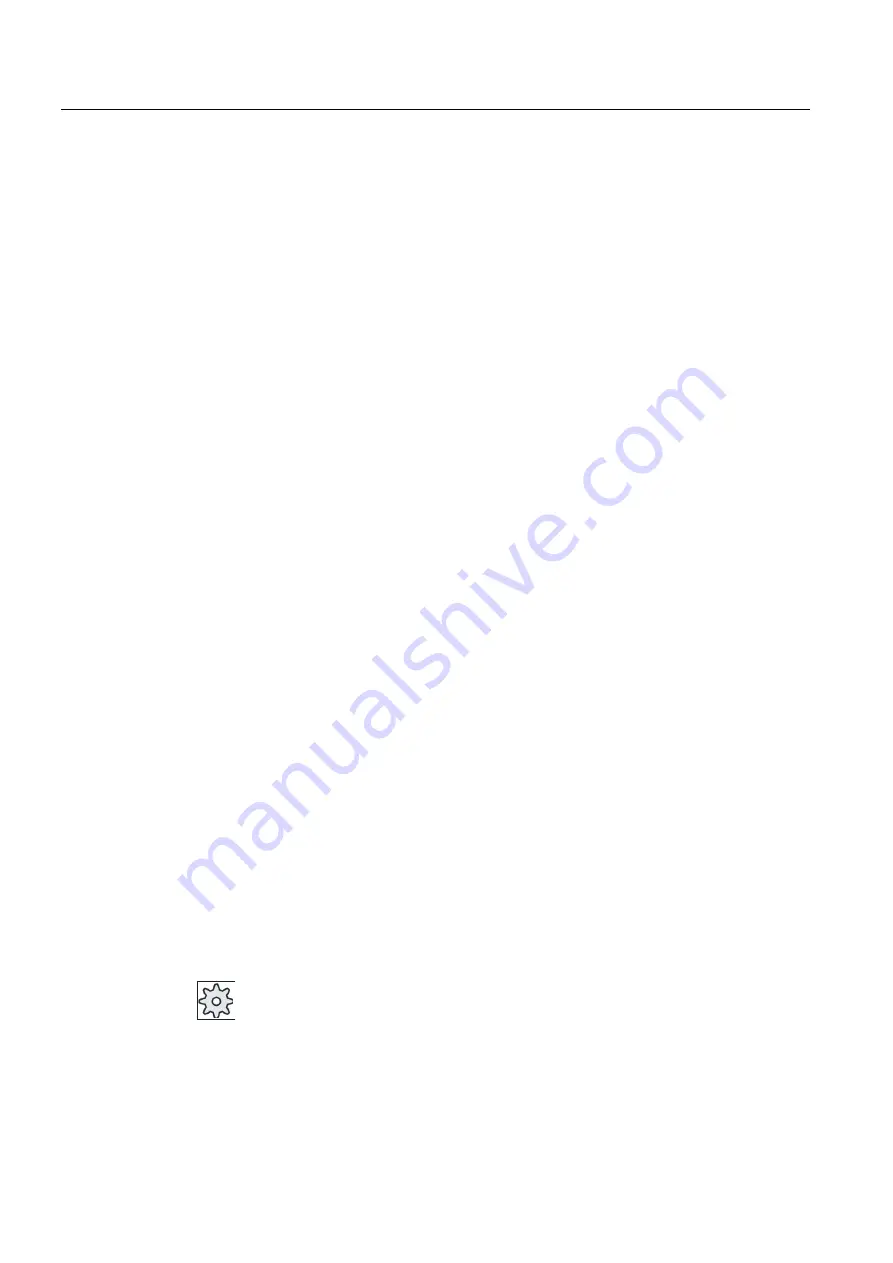
Programming technological functions (cycles)
8.1 Drilling
Milling
276
Operating Manual, 03/2010, 6FC5398-7CP20-1BA0
Approach/retraction - CYCLE84 - without compensating chuck
One cut:
1.
Travel with G0 to the safety clearance of the reference point.
2.
Spindle is synchronized and started with the programmed speed (dependent on %S).
3.
Tapping with spindle-feedrate synchronization to Z1.
4.
Spindle stop and dwell time at drilling depth.
5.
Spindle reverse after dwell time has elapsed.
6.
Retraction with active spindle retraction speed (dependent on %S) to safety clearance
7.
Spindle stop.
8.
Retraction to retraction plane with G0.
Approach/retraction during stock removal
1.
The tool drills at the programmed spindle speed S (dependent on %S) as far as the first
infeed depth (maximum infeed depth D).
2.
Spindle stop and dwell time DT.
3.
The tool retracts from the workpiece for the stock removal with spindle speed SR to the
safety clearance.
4.
Spindle stop and dwell time DT.
5.
The tool then drills with spindle speed S as far as the next infeed depth.
6.
Steps 2 to 5 are repeated until the programmed final drilling depth Z1 is reached.
7.
On expiry of dwell time DT, the tool is retracted with spindle speed SR to the safety
clearance. The spindle stops and retracts to the retraction plane.
Approach/retraction during chipbreaking
1.
The tool drills at the programmed spindle speed S (dependent on %S) as far as the first
infeed depth (maximum infeed depth D).
2.
Spindle stop and dwell time DT.
3.
The tool retracts by the retraction distance V2 for chipbreaking.
4.
The tool then drills to the next infeed depth at spindle speed S (dependent on %S).
5.
Steps 2 to 4 are repeated until the programmed final drilling depth Z1 is reached.
6.
On expiry of dwell time DT, the tool is retracted with spindle speed SR to the safety
clearance. The spindle stops and retracts to the retraction plane.
Machine manufacturer
Please refer to the machine manufacturer's specifications.
Содержание SINUMERIK 840D
Страница 6: ...Preface Milling 6 Operating Manual 03 2010 6FC5398 7CP20 1BA0 ...
Страница 50: ...Introduction 1 4 User interface Milling 50 Operating Manual 03 2010 6FC5398 7CP20 1BA0 ...
Страница 134: ...Execution in manual mode 3 7 Default settings for manual mode Milling 134 Operating Manual 03 2010 6FC5398 7CP20 1BA0 ...
Страница 172: ...Machining the workpiece 4 13 Setting for automatic mode Milling 172 Operating Manual 03 2010 6FC5398 7CP20 1BA0 ...
Страница 194: ...Simulating machining 5 9 Displaying simulation alarms Milling 194 Operating Manual 03 2010 6FC5398 7CP20 1BA0 ...
Страница 207: ...Creating G code program 6 8 Selection of the cycles via softkey Milling Operating Manual 03 2010 6FC5398 7CP20 1BA0 207 ...
Страница 208: ...Creating G code program 6 8 Selection of the cycles via softkey Milling 208 Operating Manual 03 2010 6FC5398 7CP20 1BA0 ...
Страница 209: ...Creating G code program 6 8 Selection of the cycles via softkey Milling Operating Manual 03 2010 6FC5398 7CP20 1BA0 209 ...
Страница 216: ...Creating G code program 6 10 Measuring cycle support Milling 216 Operating Manual 03 2010 6FC5398 7CP20 1BA0 ...
Страница 264: ...Creating a ShopMill program 7 17 Example standard machining Milling 264 Operating Manual 03 2010 6FC5398 7CP20 1BA0 ...
Страница 440: ...Multi channel view 9 3 Setting the multi channel view Milling 440 Operating Manual 03 2010 6FC5398 7CP20 1BA0 ...
Страница 460: ...Teaching in a program 11 7 Deleting a block Milling 460 Operating Manual 03 2010 6FC5398 7CP20 1BA0 ...
Страница 600: ...Appendix A 2 Overview Milling 600 Operating Manual 03 2010 6FC5398 7CP20 1BA0 ...
Страница 610: ...Index Milling 610 Operating Manual 03 2010 6FC5398 7CP20 1BA0 ...