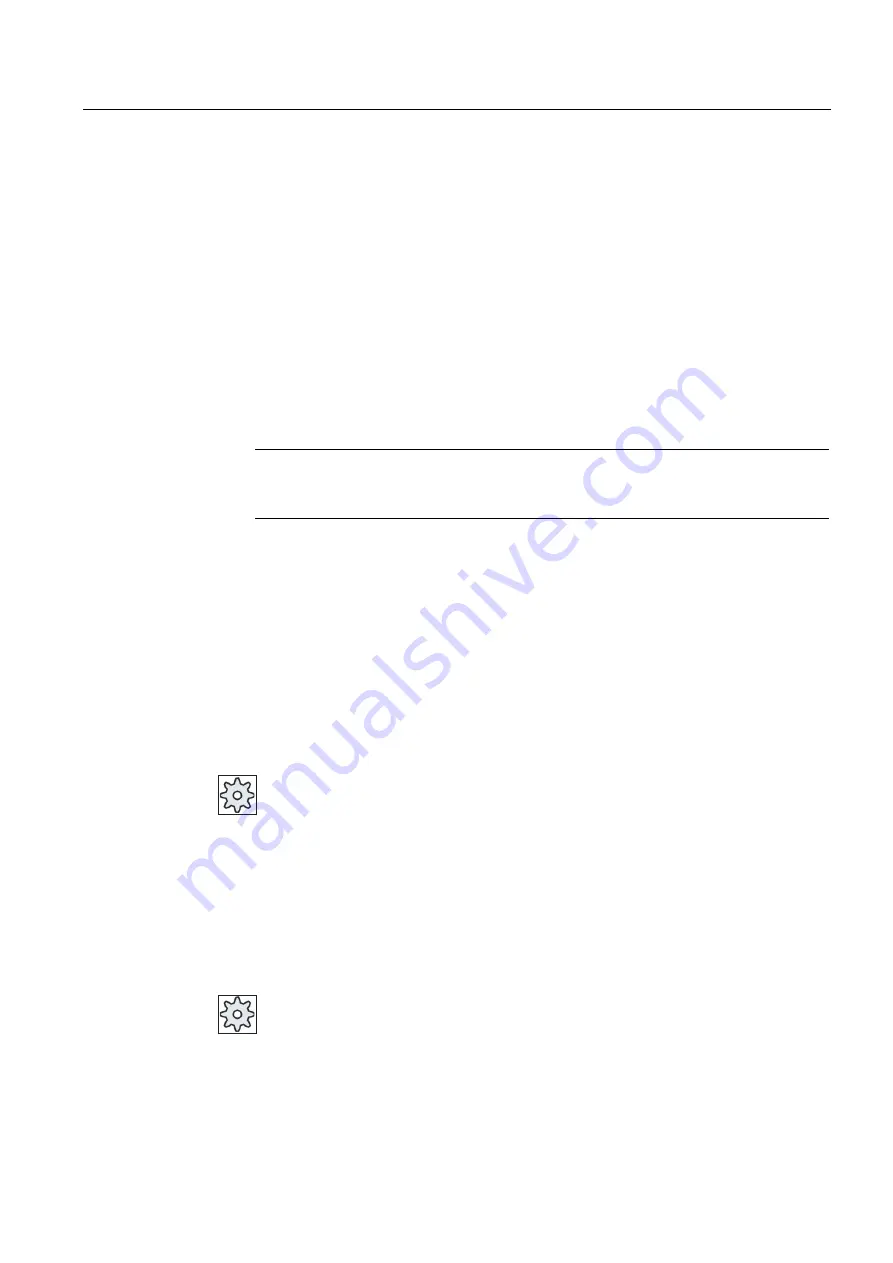
Execution in manual mode
3.5 Swiveling
Milling
Operating Manual, 03/2010, 6FC5398-7CP20-1BA0
127
●
Swivel plane
You can start the swivel plane as "new" or "additive" to a swivel plane that is already
active.
●
Swivel mode
Swiveling can be axis by axis or direct.
–
Axis-by-axis swiveling is based on the coordinate system of the workpiece (X, Y, Z).
The coordinate axis sequence can be selected freely. Rotations are applied in the
selected sequence. The rotation of the two rotary axes (A, B or C) is calculated from
this.
–
For direct swiveling, the required positions of the rotary axes are specified. A suitable
new coordinate system is calculated based on those values. The tool axis is aligned in
the Z direction. You can derive the resulting direction of the X and Y axis by traversing
the axes.
Note
The positive direction of each rotation for the different swivel methods is shown in the
help displays.
●
Direction
"Direction" corresponds to the parameter _DIR of CYCLE800.
For swivel systems with 2 rotary axes, a particular plane can be reached in two different
ways. You can choose between these two different positions in the "Direction" parameter.
The +/- corresponds to the larger or smaller value of a rotary axis. This may affect the
working area.
When the swivel data set is set up, the entries in the "Direction" parameter determine for
which rotary axis you can select each of the two settings.
If one of the two positions cannot be reached for mechanical reasons, the alternative
position is automatically selected irrespective of the setting of the "Direction" parameter.
Machine manufacturer
Please refer to the machine manufacturer's specifications.
●
Correcting tool
"Tool" corresponds to the Parameter _ST=1x (correct tool tip) of CYCLE800.
To avoid collisions, you can use the 5-axis transformation (software option) to retain the
position of the tool tip during swiveling.
When machine manufacturer commissions the function "Swivel Manual", "Track Tool"
must be enabled.
Machine manufacturer
Please refer to the machine manufacturer's specifications.
Содержание SINUMERIK 840D
Страница 6: ...Preface Milling 6 Operating Manual 03 2010 6FC5398 7CP20 1BA0 ...
Страница 50: ...Introduction 1 4 User interface Milling 50 Operating Manual 03 2010 6FC5398 7CP20 1BA0 ...
Страница 134: ...Execution in manual mode 3 7 Default settings for manual mode Milling 134 Operating Manual 03 2010 6FC5398 7CP20 1BA0 ...
Страница 172: ...Machining the workpiece 4 13 Setting for automatic mode Milling 172 Operating Manual 03 2010 6FC5398 7CP20 1BA0 ...
Страница 194: ...Simulating machining 5 9 Displaying simulation alarms Milling 194 Operating Manual 03 2010 6FC5398 7CP20 1BA0 ...
Страница 207: ...Creating G code program 6 8 Selection of the cycles via softkey Milling Operating Manual 03 2010 6FC5398 7CP20 1BA0 207 ...
Страница 208: ...Creating G code program 6 8 Selection of the cycles via softkey Milling 208 Operating Manual 03 2010 6FC5398 7CP20 1BA0 ...
Страница 209: ...Creating G code program 6 8 Selection of the cycles via softkey Milling Operating Manual 03 2010 6FC5398 7CP20 1BA0 209 ...
Страница 216: ...Creating G code program 6 10 Measuring cycle support Milling 216 Operating Manual 03 2010 6FC5398 7CP20 1BA0 ...
Страница 264: ...Creating a ShopMill program 7 17 Example standard machining Milling 264 Operating Manual 03 2010 6FC5398 7CP20 1BA0 ...
Страница 440: ...Multi channel view 9 3 Setting the multi channel view Milling 440 Operating Manual 03 2010 6FC5398 7CP20 1BA0 ...
Страница 460: ...Teaching in a program 11 7 Deleting a block Milling 460 Operating Manual 03 2010 6FC5398 7CP20 1BA0 ...
Страница 600: ...Appendix A 2 Overview Milling 600 Operating Manual 03 2010 6FC5398 7CP20 1BA0 ...
Страница 610: ...Index Milling 610 Operating Manual 03 2010 6FC5398 7CP20 1BA0 ...