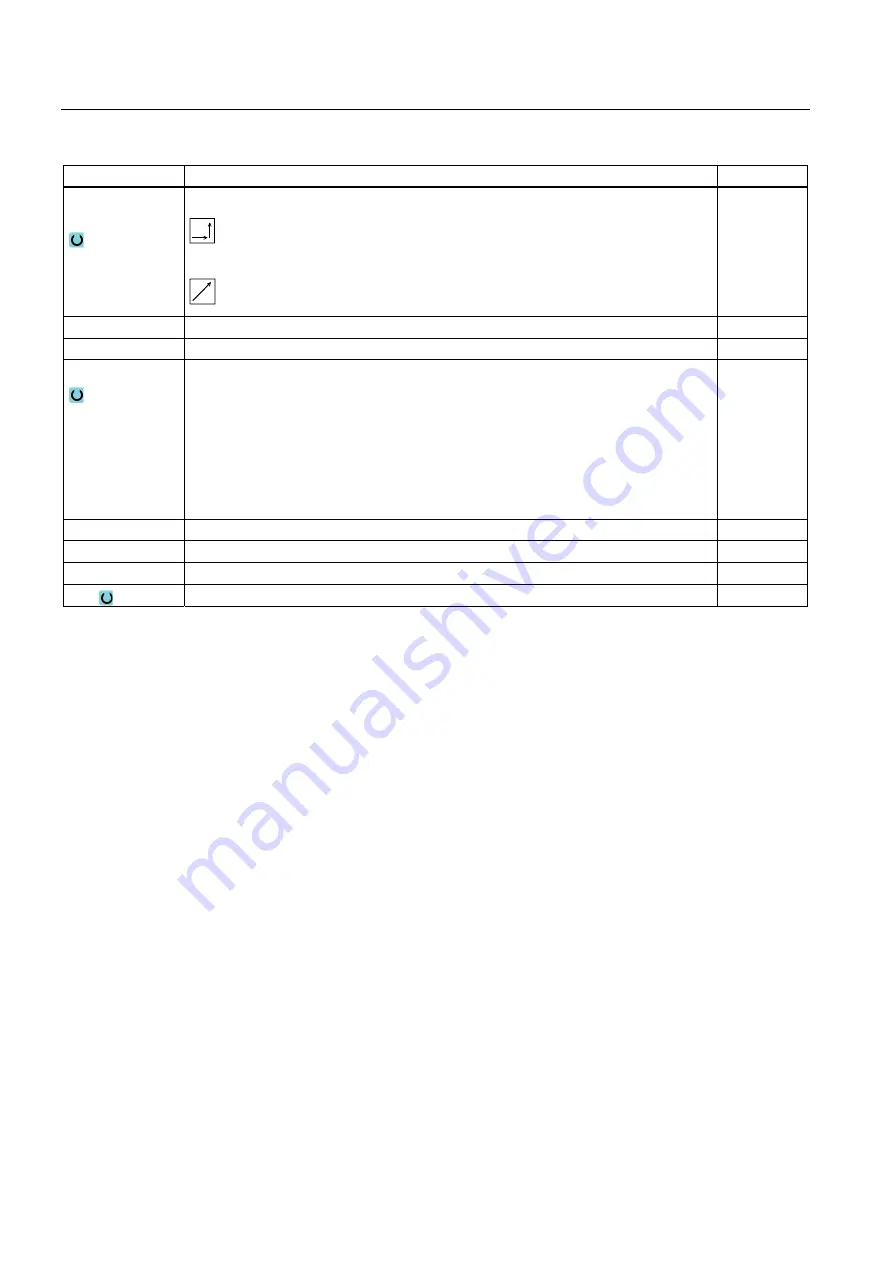
Programming technological functions (cycles)
8.3 Contour milling
Milling
342
Operating Manual, 03/2010, 6FC5398-7CP20-1BA0
Parameter
Description
Unit
Retraction
strategy
Axis by axis
Spatial (not with perpendicular approach mode)
R2
Retraction radius - (only for "quadrant or semi-circle" retraction)
mm
L2
Retraction distance - (only for "straight line" retraction)
mm
Lift mode
If more than one depth infeed is necessary, specify the retraction height to which the
tool retracts between the individual infeeds (at the transition from the end of the contour
to the start).
Lift mode before new infeed
Z0 + safety clearance
By the safety clearance
to RP
No retraction
FZ
Depth infeed rate - (only for G code)
FR
Retraction feedrate for intermediate positioning - (not with "No retraction" lift mode)
FS
Chamfer width for chamfering - (only for chamfering machining)
mm
ZFS
Insertion depth of tool tip (abs or inc) - (for machining only)
mm
8.3.8
Contour pocket/contour spigot (CYCLE63/64)
Contours for pockets or islands
Contours for pockets or islands must be closed, i.e. the starting point and end point of the
contour are identical. You can also mill pockets that contain one or more islands. The islands
can also be located partially outside the pocket or overlap each other. The first contour you
specify is interpreted as the pocket contour and all the others as islands.
Automatically calculating/Manually entering the starting point
Using "Automatic starting point" you have the option of calculating the optimum plunge point.
By selecting "Manual starting point", you define the plunge point in the parameter screen.
If the islands and the miller diameter, which must be plunged at various locations, are
obtained from the pocket contour, then the manual entry only defines the first plunge point;
the remaining plunge points are automatically calculated.
Contours for spigots
Contours for spigots must be closed, i.e. the starting point and end point of the contour are
identical. You can define multiple spigots, which can also overlap. The first contour specified
is interpreted as a blank contour and all others as spigots.
Содержание SINUMERIK 840D
Страница 6: ...Preface Milling 6 Operating Manual 03 2010 6FC5398 7CP20 1BA0 ...
Страница 50: ...Introduction 1 4 User interface Milling 50 Operating Manual 03 2010 6FC5398 7CP20 1BA0 ...
Страница 134: ...Execution in manual mode 3 7 Default settings for manual mode Milling 134 Operating Manual 03 2010 6FC5398 7CP20 1BA0 ...
Страница 172: ...Machining the workpiece 4 13 Setting for automatic mode Milling 172 Operating Manual 03 2010 6FC5398 7CP20 1BA0 ...
Страница 194: ...Simulating machining 5 9 Displaying simulation alarms Milling 194 Operating Manual 03 2010 6FC5398 7CP20 1BA0 ...
Страница 207: ...Creating G code program 6 8 Selection of the cycles via softkey Milling Operating Manual 03 2010 6FC5398 7CP20 1BA0 207 ...
Страница 208: ...Creating G code program 6 8 Selection of the cycles via softkey Milling 208 Operating Manual 03 2010 6FC5398 7CP20 1BA0 ...
Страница 209: ...Creating G code program 6 8 Selection of the cycles via softkey Milling Operating Manual 03 2010 6FC5398 7CP20 1BA0 209 ...
Страница 216: ...Creating G code program 6 10 Measuring cycle support Milling 216 Operating Manual 03 2010 6FC5398 7CP20 1BA0 ...
Страница 264: ...Creating a ShopMill program 7 17 Example standard machining Milling 264 Operating Manual 03 2010 6FC5398 7CP20 1BA0 ...
Страница 440: ...Multi channel view 9 3 Setting the multi channel view Milling 440 Operating Manual 03 2010 6FC5398 7CP20 1BA0 ...
Страница 460: ...Teaching in a program 11 7 Deleting a block Milling 460 Operating Manual 03 2010 6FC5398 7CP20 1BA0 ...
Страница 600: ...Appendix A 2 Overview Milling 600 Operating Manual 03 2010 6FC5398 7CP20 1BA0 ...
Страница 610: ...Index Milling 610 Operating Manual 03 2010 6FC5398 7CP20 1BA0 ...