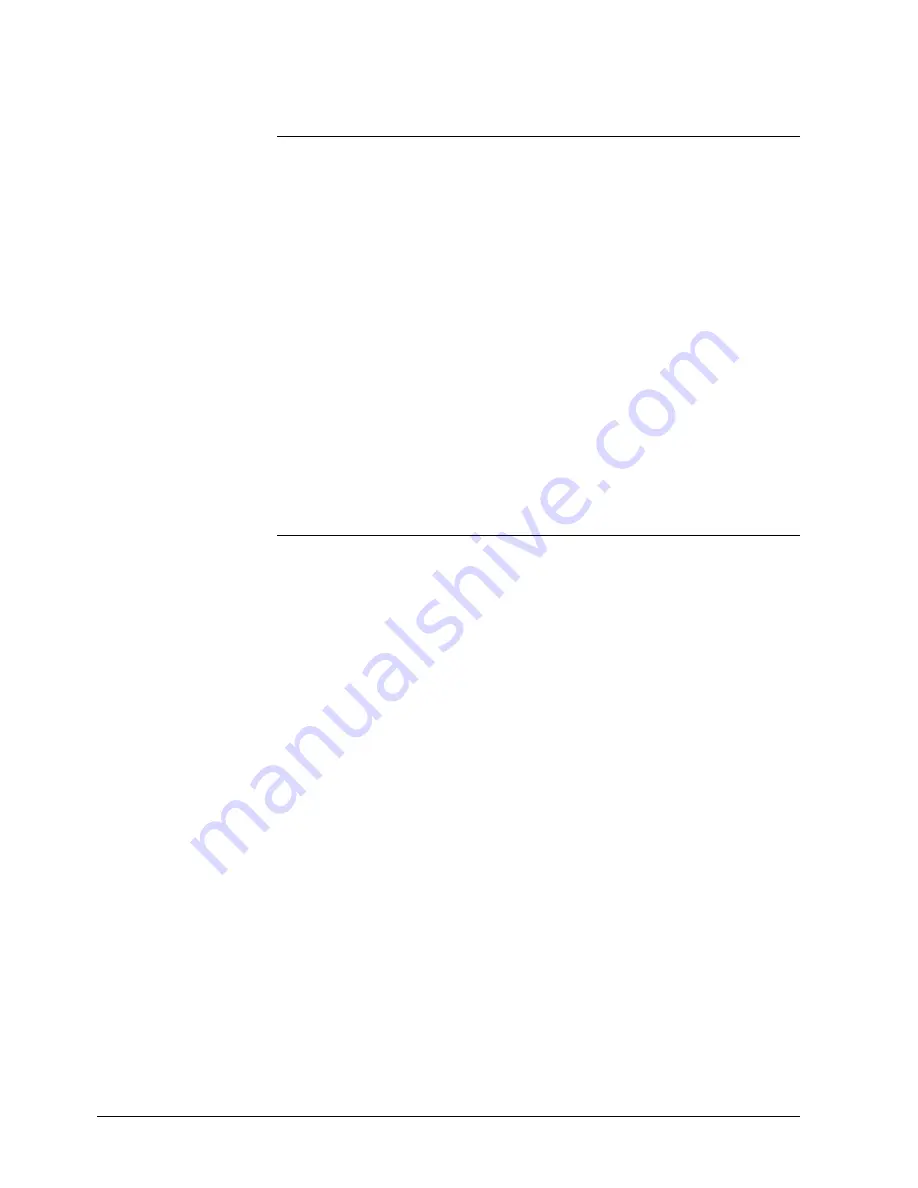
188/218
Siemens Building Technologies
Basic Documentation RVA63.242, RVA53.242
CE1P2373E
Landis & Staefa Division
General control processes
26.03.2001
6.3 Modulating burner control
6.3.1 Setting rules for Xp, Tn and Tv
Setting values
Xp
(proportional band),
Tn
(integral action time) and
Tv
(derivative
action time) are used to match the controller to the plant’s characteristics. This enables
the plant to quickly adjust heat generation to load changes when the demand for heat
increases, for example, so that the boiler temperature will only slightly deviate from the
setpoint and for short periods of time only.
Most plants change their behavior depending on the load.
If the setting values are not adequately adjusted, the control system’s response is
either too slow or too quick. If the control system operates correctly in the upper load
range and not satisfactorily in the lower load range (or via versa), mean values should
be used, which may lead to a slightly less satisfactory control behavior in the load
range that previously showed a good performance.
It should be made certain that when commissioning the modulating burner for the first
time, the present parameters of Xp, Tn and Tv will be used. To optimize and check the
control parameters, it is recommended to follow the procedure detailed below under
“Checking the control function”.
6.3.2 Checking the control function
To check the control behavior with the preset control parameters, the following
procedure is recommended:
after the controller has reached and held the setpoint for a certain time, change the
setpoint by 5 to 10 %, either up or down. When making this test, it is of advantage to
have the plant operating in the lower load range where, usually, it is more difficult to
control.
In principle, control must be stable, but it may be fast- or slow-acting.
If fast control is required, the boiler temperature must reached the new setpoint fairly
quickly.
If fast control of a setpoint change (disturbance) is not a mandatory requirement, the
control action can be rather slow. Non-oscillating control reduces wear on the actuator
and on other electromechanical controls used in the plant.
If the control does not produce the required result, the control parameters should be
adjusted as follows:
6.3.3 Control action too slow
If the control system’s response is too slow, setting parameters Xp, Tv and Tn must be
decreased in a stepwise fashion. A new readjustment should be made only after the
control action resulting from the previous readjustment is completed.
Introduction