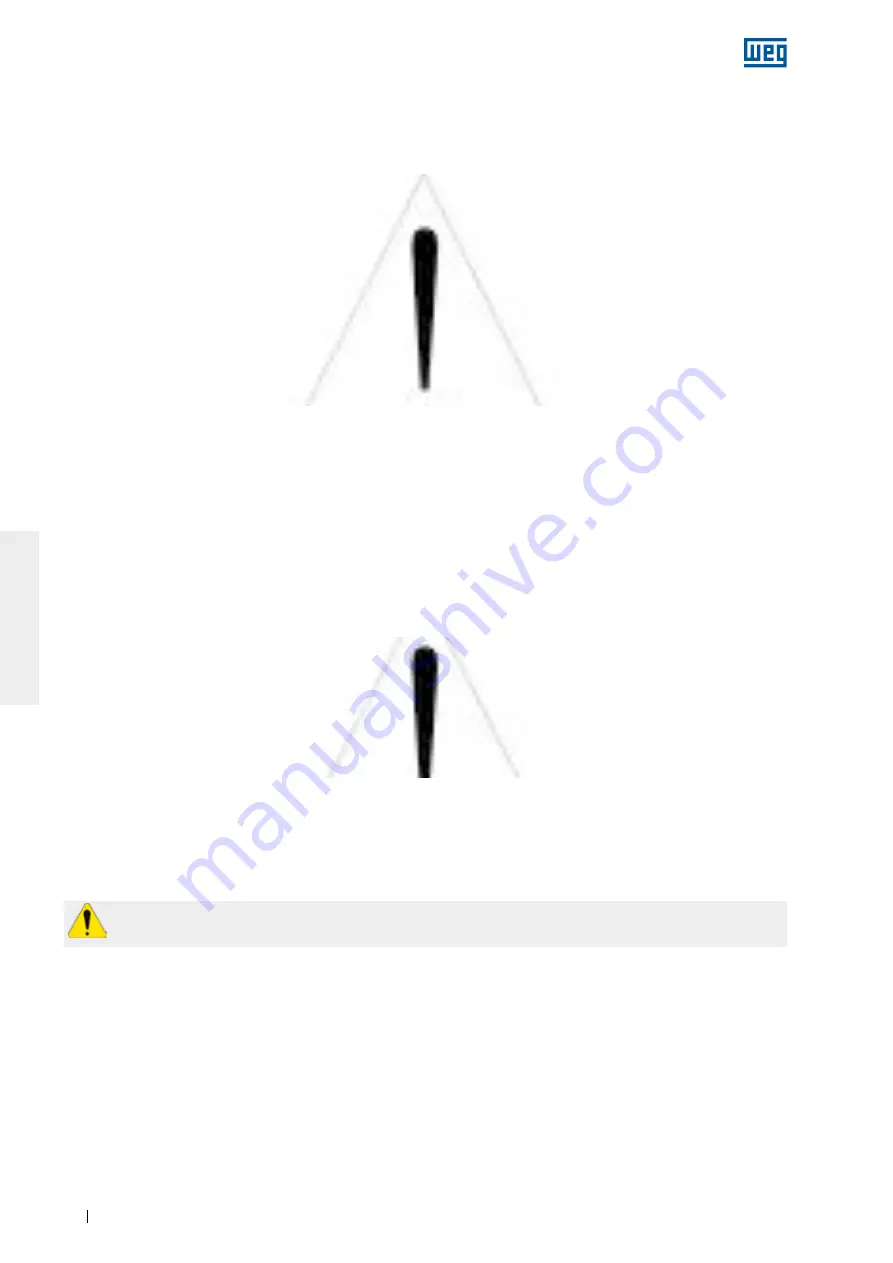
www.weg.net
Manual of Electric Motors
82
E
N
G
LI
S
H
For flange mounting the thread engagement length of the mounting bolt should be at least 1.5 times the bolt
diameter. In severe applications, longer thread engagement length may be required.
In severe applications or if large motors are flange mounted, a foot or pad mounting may be required in addition
to the flange mounting (Figure 6.7). The motor must never be supported on its cooling fins.
6.2.3. Pad mounted motors
Typically, this method of mounting is used in axial fans. The motor is fixed by tapped holes in the frame. The
dimensions of these tapped holes can be checked in the respective product catalogue. The selection of the
motor mounting rods/bolts must consider the dimensions of the fan case, the installation base and the thread
depth in the motor frame.
The mounting rods and the fan case wall must be sufficiently stiff to prevent the transmission of excessive
vibration to the machine set (motor & fan). Figure 6.8 shows the pad mounting system.
Figure 6.7
- Mounting method of flange mounted motors with frame base support
Figure 6.8
- Mounting of the motor inside the cooling duct
Note
:
When liquid (for example oil) is likely to come into contact with the shaft seal, please contact your local WEG representative.
The balance quality grade meets the applicable standards for each product line.
The maximum balancing deviation must be recorded in the installation report.
The transmission elements, such as pulleys, couplings, etc., must balanced with “half key” before they
are mounted on the motor shaft.
6.3. BALANCING
Unbalanced machines generate vibration which can result in damage to the motor. WEG motors are
dynamically balanced with “half key” and without load (uncoupled). Special balancing quality level must be
stated in the Purchase Order.
6.4. COUPLINGS
Couplings are used to transmit the torque from the motor shaft to the shaft of the driven machine. The following
aspects must be considered when couplings are installed:
g
Use proper tools for coupling assembly & disassembly to avoid damages to the motor and bearings;
g
Whenever possible, use flexible couplings, since they can absorb eventual residual misalignments during the
machine operation;
g
The maximum loads and speed limits informed in the coupling and motor manufacturer catalogues cannot
be exceeded;
g
Level and align the motor as specified in sections 6.5 and 6.6, respectively.
Page 153
Содержание BN 5-12 Series
Страница 13: ...TAB 1 DEVICE DATA SHEETS ...
Страница 18: ...TAB 2 APPROVED SUBMITTAL ...
Страница 23: ...All data subject to change without notice 1 800 ASK 4WEG www weg net 14 ...
Страница 26: ...Your advantages our pumps ...
Страница 45: ...ADV 2 13E And what can we get flowing for you Your nearest contact Or visit www seepex com ...
Страница 117: ...TAB 3 INSTALLATION OPERATIONS AND MAINTENANCE ...
Страница 133: ...Page 37 ...
Страница 233: ...www weg net Manual of Electric Motors 64 ENGLISH Figure 2 1 IEC motor nameplate Page 135 ...
Страница 234: ...www weg net Manual of Electric Motors 65 ENGLISH Figure 2 2 NEMA motor nameplate Page 136 ...
Страница 306: ...TAB 4 AS BUILTS AND SUPPLEMENTAL INFORMATION ...
Страница 307: ...R Page 29 ...
Страница 308: ...R Page 30 ...