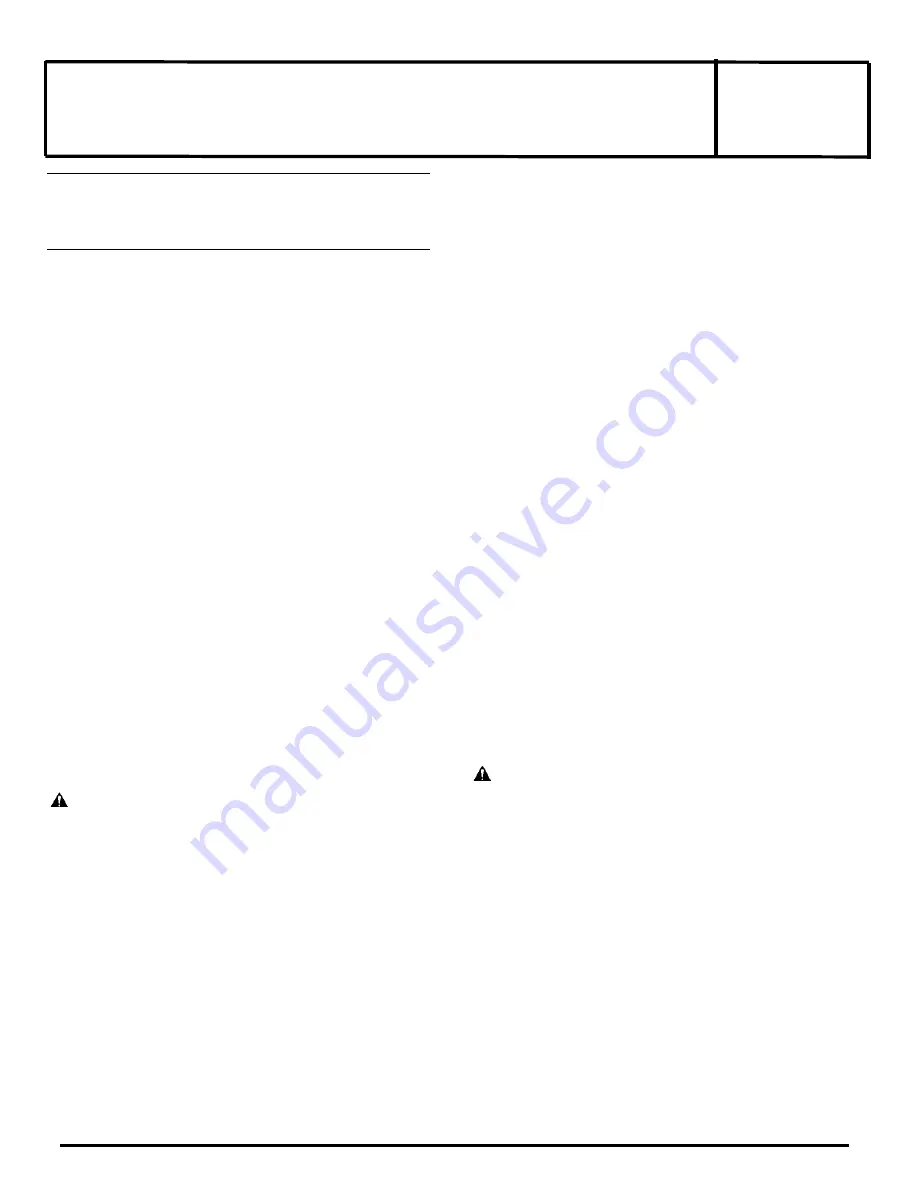
ASCO Valves®
All Rights Reserved.
I&M No. V 5847 R2
©ASCO Valve, Inc.®
50 Hanover Road, Florham Park, New Jersey 07932 www.ascovalve.com
E243264- 2/14
I&M No. V 5847 R2 - T84
Installation & Maintenance Instructions
2-WAY INTERNAL PILOT-OPERATED SOLENOID VALVES
DIAPHRAGM TYPE — 3/8 AND 1/2 NPT
NORMALLY CLOSED OPERATION
Temperature Limitations
•
Max Valve Ambient Temperature: See Solenoid I&M or
Catalog
•
Max Valve Temperature: 175°F
The temperature limitations listed are for UL applications. For non
UL applications, higher ambient and fl uid temperature limitations
are available. Consult factory. Check catalog number on nameplate
to determine maximum temperatures.
Positioning
This valve is designed to perform properly when mounted in any
position. However, for optimum life and performance, the solenoid
should be mounted vertically and upright to reduce the possibility
of foreign matter accumulating in the solenoid base sub
-
assembly
area.
Mounting
For mounting bracket (optional feature) dimensions, refer to Figure
1.
Piping
Connect piping to valve according to markings on valve body.
Apply pipe compound or PTFE tape sparingly to male pipe threads
only. If applied to valve threads, the compound may enter the valve
and cause operational diffi culty. Avoid pipe strain by properly
supporting and aligning piping. When tightening the pipe, do not
use valve or solenoid as a lever. Locate wrenches applied to valve
body or piping as close as possible to connection point.
CAUTION: To protect the solenoid valve, install a strainer
or fi lter suitable for the service involved in the inlet side
as close to the valve as possible. Clean periodically
depending on service conditions. See ASCO Series 8600
and 8601 for strainers.
MAINTENANCE
WARNING: To prevent the possibility of severe
personal injury or property damage, turn off
electrical power, depressurize valve, extinguish
all open fl ames, and avoid any type of sparking
or ignition. Vent hazardous or combustible fl uid
to a safe area before servicing the valve.
NOTE: It is not necessary to remove the valve from the pipeline for
repairs.
Cleaning
All solenoid valves should be cleaned periodically. The time
between cleanings will vary depending on the medium and service
conditions. In general, if the voltage to the coil is correct, sluggish
valve operation, excessive noise or leakage will indicate that
cleaning is required. In the extreme case, faulty valve operation will
occur and the valve may fail to open or close. Clean strainer or fi lter
when cleaning the valve.
SERIES
8210
DESCRIPTION
Series 8210 valves are 2-way normally closed, internal pilot operated
solenoid valves. Valve body and bonnet are of brass construction.
Series 8210 valves may be provided with a general purpose/
watertight, open-frame or explosionproof/watertight solenoid.
Notice: These valves are not certifi ed as lead-free under the
Safe Water Drinking Act SWDA 1417 and are not intended
for use on drinking water systems. They are intended for
control of water in industrial applications. Consult ASCO
for valves rated for use in potable water applications.
OPERATION
Normally Closed:
Valve is closed when solenoid is de-energized;
open when energized.
Manual Operator
(Optional)
Valves with suffi x “MO” in catalog number are provided with a
manual operator which allows manual operation when desired
or during an interruption of electrical power. To operate valve
manually, push in knurled cap and rotate 180°. Disengage manual
operator by rotating knurled cap counterclockwise 180° before
operating electrically.
Manual Operator Location
(Refer to Figure 3)
Manual operator (when shipped from factory) will be located
over the valve outlet. Manual operator may be relocated at 90°
increments by rotating valve bonnet. Remove bonnet screws (4)
and rotate valve bonnet with solenoid to desired position. Replace
bonnet screws (4) and torque in a crisscross manner to 110
±10 inch
pounds.
If valve is installed in the system and is operational, proceed in the
following manner:
WARNING: To prevent the possibility of death,
serious injury or property damage, depressurize
valve and vent fl uid to a safe area before servicing
the valve.
1.
Remove the solenoid - see separate solenoid instructions.
2.
Remove bonnet screws (4) and rotate valve bonnet to desired
position.
3.
Replace bonnet screws (4) and torque in a crisscross manner to
110
±10 inch pounds.
4.
Replace all solenoid parts.
INSTALLATION
Check nameplate for correct catalog number, pressure, voltage,
frequency, and service. Never apply incompatible fl uids or exceed
pressure rating of the valve. Installation and valve maintenance to
be performed by qualifi ed personnel.
NOTICE: See separate solenoid installation and maintenance
instructions for information on: Wiring, Solenoid Temperature,
Cause of Improper Operation, Coil or Solenoid Replacement.
Page 1 of 3
Page 202
Содержание BN 5-12 Series
Страница 13: ...TAB 1 DEVICE DATA SHEETS ...
Страница 18: ...TAB 2 APPROVED SUBMITTAL ...
Страница 23: ...All data subject to change without notice 1 800 ASK 4WEG www weg net 14 ...
Страница 26: ...Your advantages our pumps ...
Страница 45: ...ADV 2 13E And what can we get flowing for you Your nearest contact Or visit www seepex com ...
Страница 117: ...TAB 3 INSTALLATION OPERATIONS AND MAINTENANCE ...
Страница 133: ...Page 37 ...
Страница 233: ...www weg net Manual of Electric Motors 64 ENGLISH Figure 2 1 IEC motor nameplate Page 135 ...
Страница 234: ...www weg net Manual of Electric Motors 65 ENGLISH Figure 2 2 NEMA motor nameplate Page 136 ...
Страница 306: ...TAB 4 AS BUILTS AND SUPPLEMENTAL INFORMATION ...
Страница 307: ...R Page 29 ...
Страница 308: ...R Page 30 ...