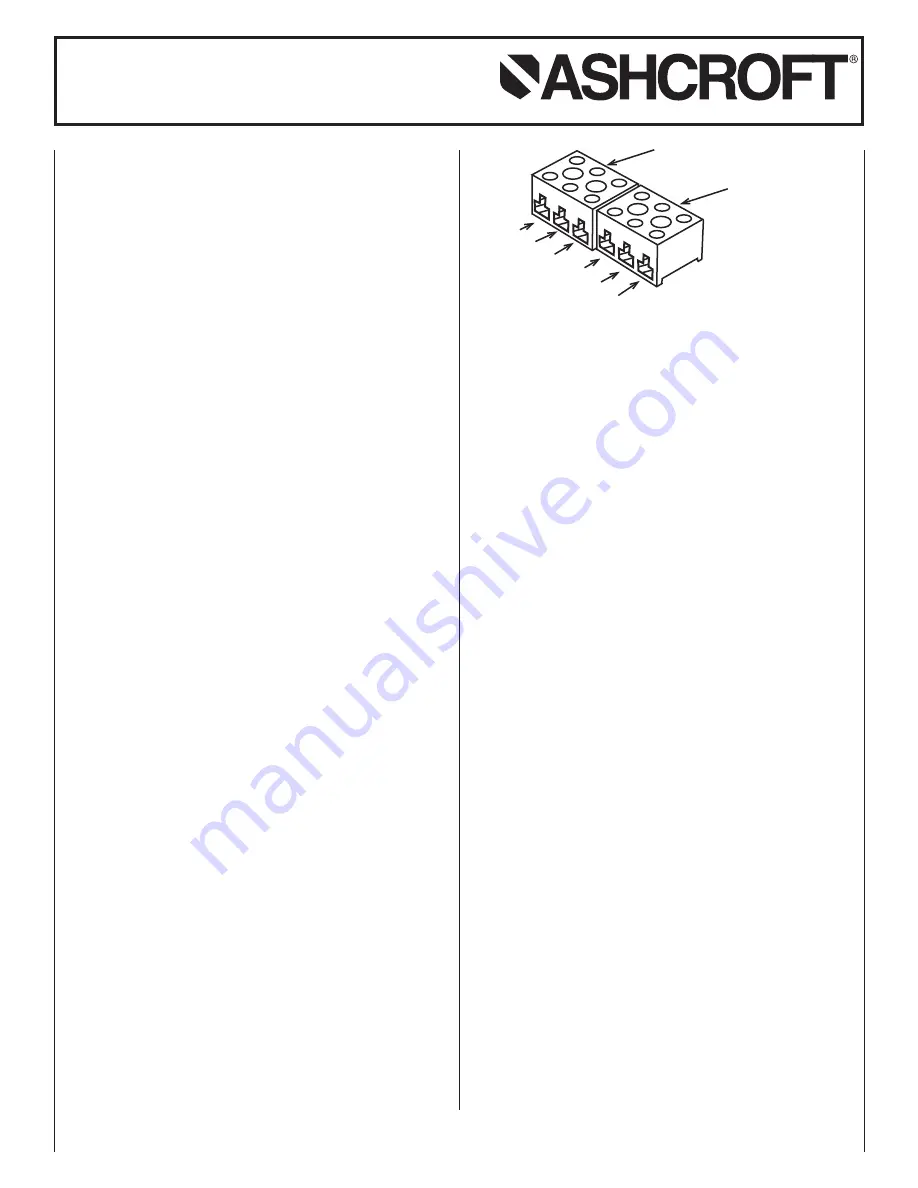
© Instrument Division, Dresser Equipment Group, Inc. All sales subject to standard terms and conditions of sale.
I&M009-10008-10/00 (250-2246E)
Printed in U.S.A
INSTALLATION
These controls are precision instruments and should never be
left with internal components exposed. During installation insure
that covers are in place and conduit openings are closed except
when actually working on the control.
MOUNTING B400 AND B700 SERIES
Three holes external to the enclosure for surface mounting.
Location of these holes is shown on the general dimension
drawing. They may also be mounted directly on pressure line
using the pressure connection.
When tightening control to pres-
sure line, always use the wrench flats or hex on the lower housing.
ELECTRICAL CONNECTIONS
Remove cover
B400 Series
– two screws hold cover to enclosure
B700 Series
– cover unscrews
CONDUIT CONNECTIONS
Note –
It is recommended that Teflon tape or other sealant be
used on conduit, bushing or plug threads to ensure integrity of
the enclosure.
B400 Series standard
– one
3
⁄
4
˝ NPT conduit hole right side.
B700 Series standard
– two
3
⁄
4
˝ N PT conduit holes with one
permanent plug. NEMA 7 & 9 enclosures require proper conduit
seals and breathers as per the National Electrical Code.
B400 & B700 Series
– XJL variation – two
3
⁄
4
˝ NPT conduit
holes with two
3
⁄
4
˝ to
1
⁄
2
˝ NPT reducing bushings.
B400 Series
– XJK variation – two
3
⁄
4
˝ NPT conduit holes.
B400 SERIES
SPDT
– Wire directly to the switch according to circuit require-
ments. On controls with pilot lights wire lights according to circuit
diagram on inside of cover. See special wiring instruction tag for
single switches with two pilot lights and dual switches with one
or more lights.
2 SPDT
– Dual switching elements consist of two SPDT switches
mounted together in a bracket. Switches are calibrated to have
simultaneous operation within 1% of range either on increasing
or decreasing pressure but not in both directions. Wire directly to
the front and rear switch according to circuit requirements.
Leads are provided on rear switch color coded as follows:
Common
– White
Normally Closed – Red
Normally Open
– Blue
See SPDT instructions for pilot light hook-up.
When hermetically sealed switch elements(s) are supplied, the
lead color coding is as follows:
Common
– White
Normally Closed – Red
Normally Open
– Blue
B700 SERIES
SPDT
– Wire directly to the switch according to circuit requirements.
2 SPDT
– Wire to front switch terminal block (left) and rear
switch terminal block (right) as marked. Strip insulation
5
⁄
16
˝,
insert in proper terminal connector and tighten clamping screw
to secure.
ADJUSTMENT OF SETPOINT
B400 & B700 Series
– A single setpoint adjustment nut (
7
⁄
8
˝) is
located centrally at the bottom on the inside of the enclosure.
For accurate setpoint calibration, mount the switch on a cali-
bration stand, a pump or catalog No.1305 deadweight gauge
tester. A suitable reference standard such as an Ashcroft
Duragauge or Test Gauge is necessary to observe convenient
changes in pressure.
As received, the pressure switch will normally be set to
approximately 90% of the indicated range. Pressurize the
system to required setpoint and turn the adjustment nut until
switch changes mode. Direction of turning is indicated on a label
affixed to the inside of the control enclosure. When setpoint has
been achieved raise and lower pressure to insure that setpoint
is correct.
After installation of the control replace cover to insure electri-
cal safety and to protect internal parts from the environment.
B450 and B750 VARIABLE DEADBAND SWITCHES
Deadband is varied by rotating the wheel on the precision
switch. When viewed from the front of the enclosure, rotation to
the left increases deadband – rotation to the right decreases
deadband. Letters on the wheel may be used as a reference.
Deadbands obtainable will vary from 0.5% to 9% of pressure
range depending on range segment and type of diaphragm.
ADJUSTMENT OF SETPOINT
As received, the pressure switch will normally be set to approxi-
mately 90% of range. Rotate the wheel on the MICRO SWITCH
all the way to the right; this will provide smallest deadband.
Pressurize the system to the required setpoint and turn the
adjustment nut until the switch changes mode. Lower the
pressure to reset the switch. Rotate the wheel on the MICRO
SWITCH until the desired deadband is obtained. The upper
setpoint will be changing upward with this adjustment. Lower the
pressure to reset the switch. Then increase the pressure to the
desired setpoint and turn the adjusting nut until the switch
changes mode. Lower the pressure and check resetpoint and
deadband.
Note
– As indicated above, adjustment of setpoint is made by
use of
7
⁄
8
˝ nut. Precision switch element mounting screws
and bracket adjusting screw are factory sealed and
should not be tampered with.
I
nstallation and Maintenance Instructions for
B400 & B700 ASHCROFT
®
Snap Action
Switches for Pressure Control
TERMINAL BLOCK
SWITCH A
TERMINAL BLOCK
SWITCH B
2
1
3
2
1
3
NC
NO
C
NC
NO
C
Note
– Since vacuum models are already above setpoint at
atmosphere, the Normally Open (NO) circuit will be
closed as received.
Page 193
Содержание BN 5-12 Series
Страница 13: ...TAB 1 DEVICE DATA SHEETS ...
Страница 18: ...TAB 2 APPROVED SUBMITTAL ...
Страница 23: ...All data subject to change without notice 1 800 ASK 4WEG www weg net 14 ...
Страница 26: ...Your advantages our pumps ...
Страница 45: ...ADV 2 13E And what can we get flowing for you Your nearest contact Or visit www seepex com ...
Страница 117: ...TAB 3 INSTALLATION OPERATIONS AND MAINTENANCE ...
Страница 133: ...Page 37 ...
Страница 233: ...www weg net Manual of Electric Motors 64 ENGLISH Figure 2 1 IEC motor nameplate Page 135 ...
Страница 234: ...www weg net Manual of Electric Motors 65 ENGLISH Figure 2 2 NEMA motor nameplate Page 136 ...
Страница 306: ...TAB 4 AS BUILTS AND SUPPLEMENTAL INFORMATION ...
Страница 307: ...R Page 29 ...
Страница 308: ...R Page 30 ...