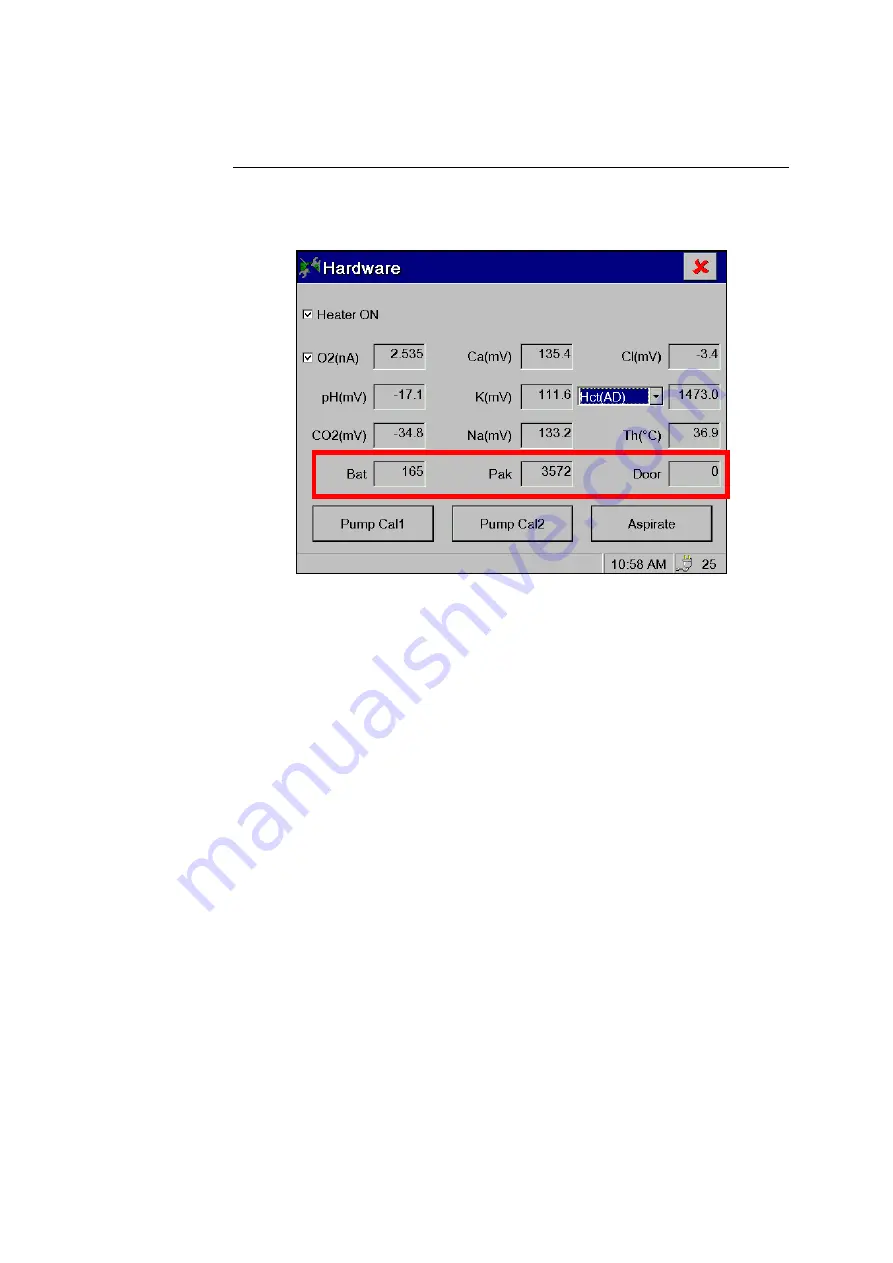
ABL77 Service Manual
Chapter 3: Troubleshooting
Hardware Screen,
Continued
Description of
Hardware
screen
(continued)
•
A relative charge reading for the battery pack is displayed (
Bat
) as well as the
function of the battery charger (
Pak
) (see Figure 3-4). An inlet flap sensor
indicator is also displayed (
Door
).
Figure 3-4
3-7
Содержание ABL 77 Series
Страница 19: ...Chapter 2 Analyzer Description ABL77 Service Manual This page intentionally left blank 2 4 Rev F ...
Страница 26: ...ABL77 Service Manual Chapter 2 Analyzer Description This page intentionally left blank Rev F 2 11 ...
Страница 40: ...ABL77 Service Manual Chapter 2 Analyzer Description This page intentionally left blank Rev F 2 25 ...
Страница 227: ...Chapter 6 Replacements ABL77 Service Manual This page intentionally left blank 6 32 Rev F ...
Страница 333: ...ABL77 Service Manual Chapter 9 Spare Parts Modules and Externals Continued Module diagrams continued Rev F 9 3 ...
Страница 335: ...ABL77 Service Manual Chapter 9 Spare Parts Upper Module Components Continued Upper module component diagram Rev F 9 5 ...
Страница 344: ...Chapter 9 Spare Parts ABL77 Service Manual This page intentionally left blank 9 14 Rev F ...